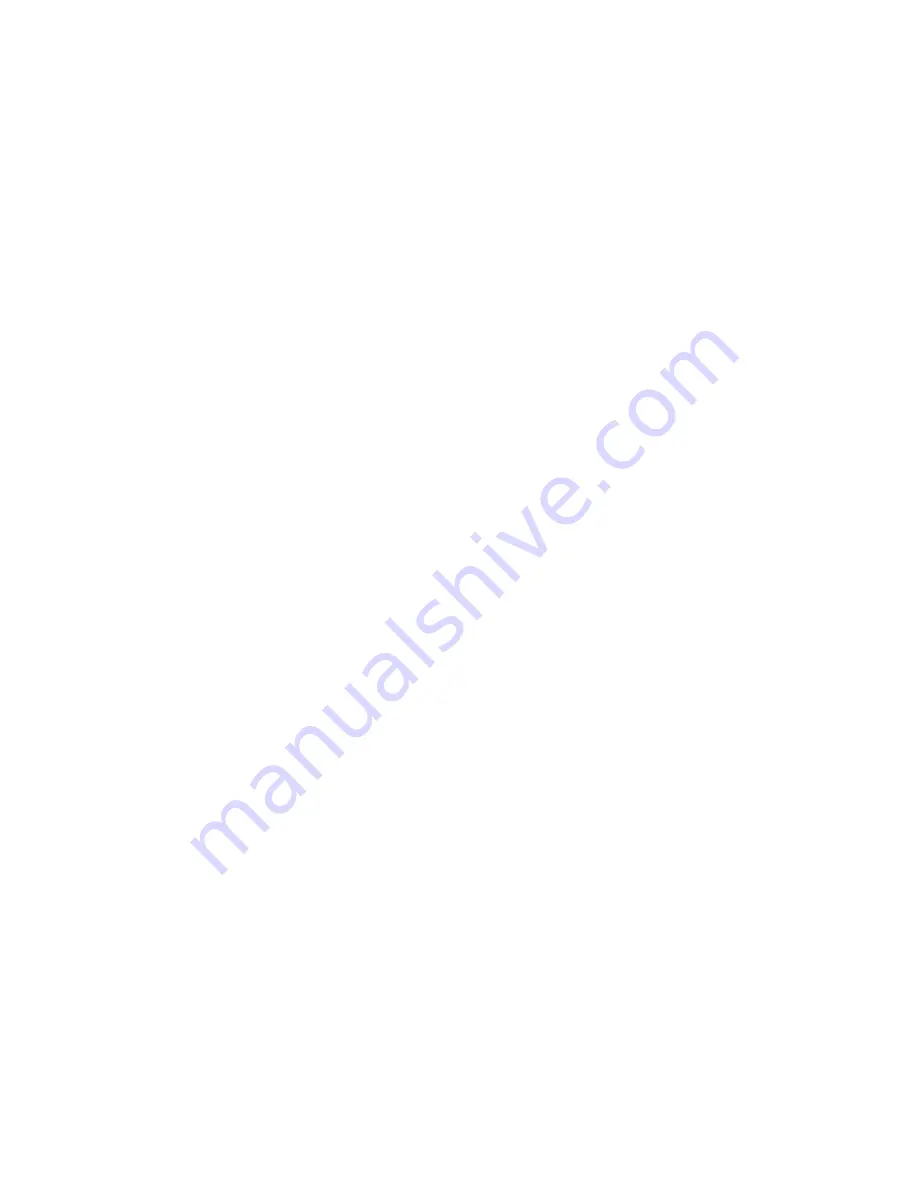
4.12 Water pump 236-1307010-
Б2
4.12.1 Assembling the filler ring 7 (picture 4.11) and 8, bearings 4 should be lubricated with the
grease Litol-
24, and cavity Д between the bearings should be filled with this grease for 4/5 of the
vo
lume (about 60 Г of the grease).
4.12.2 Bearings 4 should be pressed at the roller 5 till the hard stop with the sides without seals
to the cavity
Д.
4.12.3 Face seal 9 should be pressed in the pump body 3 till the hard stop and pressed on the
roller 6 so that the dimensions J was from 10.2 to 10.6 mm. Seal installation should be performed
applying special mandrels bearing at the surfaces
В, Г, Е.
4.12.4 Pulley 5 should be pressed at the roller till the hard stop into the outside bearing.
Pressing on should be performed with the bearing at the roller surface
Б.
4.12.5 Vane 2 should be pressed at the roller so that face surface of the vane was in one flatness
with the roller surface B. Pressing on should be performed with the bearing at the roller surface
Г.
4.12.6 After the pressing of the vane and flange one should control the seating of the specified
parts applying the torque from 47.5 to 52.5 Nwm (from 4.75 to 5.25 kfg m). Rotation of the parts at
the roller is not permitted.
4.12.7 In the assembled pump roller 6 should rotate free without constraints from the manual
effort. Vane contact 2 with the manifold 1 is not permitted.
4.12.8 The pump should be tested for the sealing with the water at a rotation rate of the roller
from 58.2 to 58.4 с–1 (from 3490 to 3500 rmp), at the water temperature no less than 293 К (20
°
C)
and under the water pressure at the pump outlet no less than 0.2 MPa(2 kfg/cm
2
) during 2 min . Water
leakage through the seals and joints of the pump as well as through the inspection hole is not
permitted.
It is allowed to test the pump for sealing during the engine tests under the working pressure in the
cooling system.
Summary of Contents for ???-236
Page 25: ...26...
Page 26: ...27 2...
Page 40: ......
Page 41: ......
Page 53: ......
Page 56: ......
Page 59: ......
Page 64: ...236 238 1003014 3 236 238 1003014 4 236 238 1003014...
Page 65: ......
Page 70: ......
Page 73: ......
Page 81: ......
Page 85: ......
Page 92: ......
Page 95: ......
Page 101: ......
Page 113: ......
Page 119: ......
Page 122: ......
Page 125: ......
Page 128: ......
Page 142: ......
Page 144: ......
Page 150: ......
Page 155: ......
Page 158: ......
Page 160: ......
Page 165: ......
Page 193: ...N u M a r Method defect detection and Dimension and parameter mm...
Page 201: ...4 Thread stripping M16 1 5 6H no more than two threads Inspection To calibrate the thread...