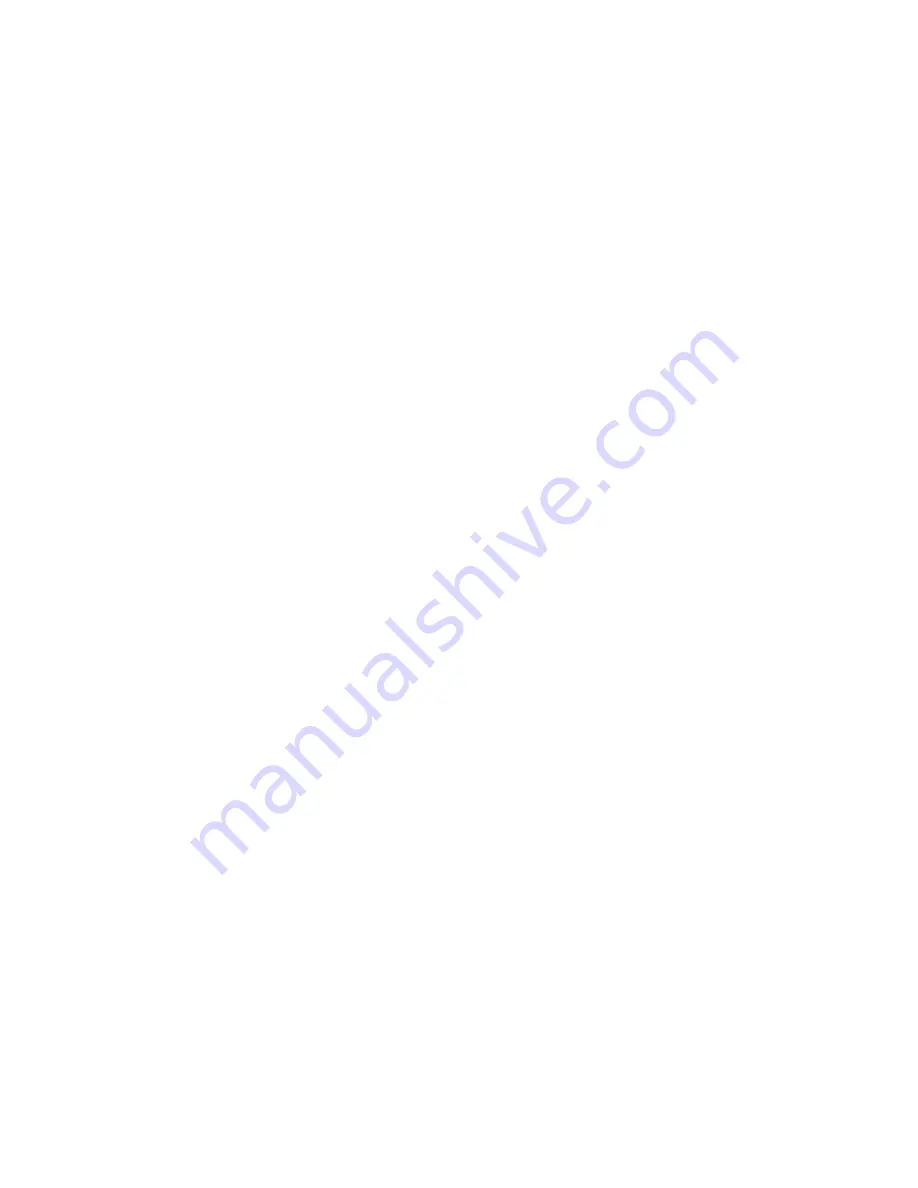
29
holes for the crankshaft bearing liners, measuring crankshaft - crank and main bearings.
2.7.7 Measurements should be made in the sections and directions of the biggest wears.
2.7.8 Parts and assembly units are considered to be applicable without repair if their
dimensions and other parameters comply with the dimensions and parameters specified in the
inspection sheets. Exceeding the allowable limits the part should be recovered or rejected
according to the technical facilities of the enterprise, economic efficiency of the recovery and
provision of the quality of repair works and guaranteed operation resource.
2.7.9
According to the results of the inspection their parts should be divided into the
groups and marked with quick drying paint:
- accepted for the engine assembly without repair with the inspection stamp and green
colour;
- repairable - with the yellow colour on the surface next to the defect;
- rejected, non-repairable, parts which should be 100% replaced during the repair (spring and
copper washers, bushings, filler rings, gaskets) - with the red colour;
Small parts need not to be marked with red colour, in this case the tare with the part should be
marked with a stamp of quality, specifying the degree of fitness.
2.7.10 During the inspection it is recommended to take measures and means of the
technological equipment that provide objective estimation of the technological condition,
accuracy of the measurements and availability of application for this enterprise. The following
methods are applied for the determination of the defects: organoleptic method (inspection, that
helps to find out visible mechanical damages, changes of the form), dimensions or gaps
measurement due to the wear, for the hidden defects such as cracks, pockets, interstices, capillary,
luminescent, acoustic methods, hydraulic pressure test, magnetic detection test are used. Date of
detection of the cracks of the crankshaft at the magnetic detection tester recommended current
rate -800 A, composition of magnetic suspension: at 1 l of water - 25 g of magnetic powder, 5 g of
glycerine, 5 g of surface active agent, 10 g of sodium carbonate). Parts should be demagnetized
after the test.
2.7.11 To estimate the dimensions, their deviation and permissible variations, gaps
between the joint surfaces, deviations of the form and relative position it is recommended to use
"Go-No-Go" plug gauge (plugs. clamps, templates).
It is also allowed to apply the general
calibre. The choice of the measuring instrument is determined by the controlled dimension and its
tolerance, providing condition at which accuracy of measuring instrument will be less than 1/3
tolerance capability.
2.7.12
To estimate the condition of the working surfaces as well as to check the
Summary of Contents for ???-236
Page 25: ...26...
Page 26: ...27 2...
Page 40: ......
Page 41: ......
Page 53: ......
Page 56: ......
Page 59: ......
Page 64: ...236 238 1003014 3 236 238 1003014 4 236 238 1003014...
Page 65: ......
Page 70: ......
Page 73: ......
Page 81: ......
Page 85: ......
Page 92: ......
Page 95: ......
Page 101: ......
Page 113: ......
Page 119: ......
Page 122: ......
Page 125: ......
Page 128: ......
Page 142: ......
Page 144: ......
Page 150: ......
Page 155: ......
Page 158: ......
Page 160: ......
Page 165: ......
Page 193: ...N u M a r Method defect detection and Dimension and parameter mm...
Page 201: ...4 Thread stripping M16 1 5 6H no more than two threads Inspection To calibrate the thread...