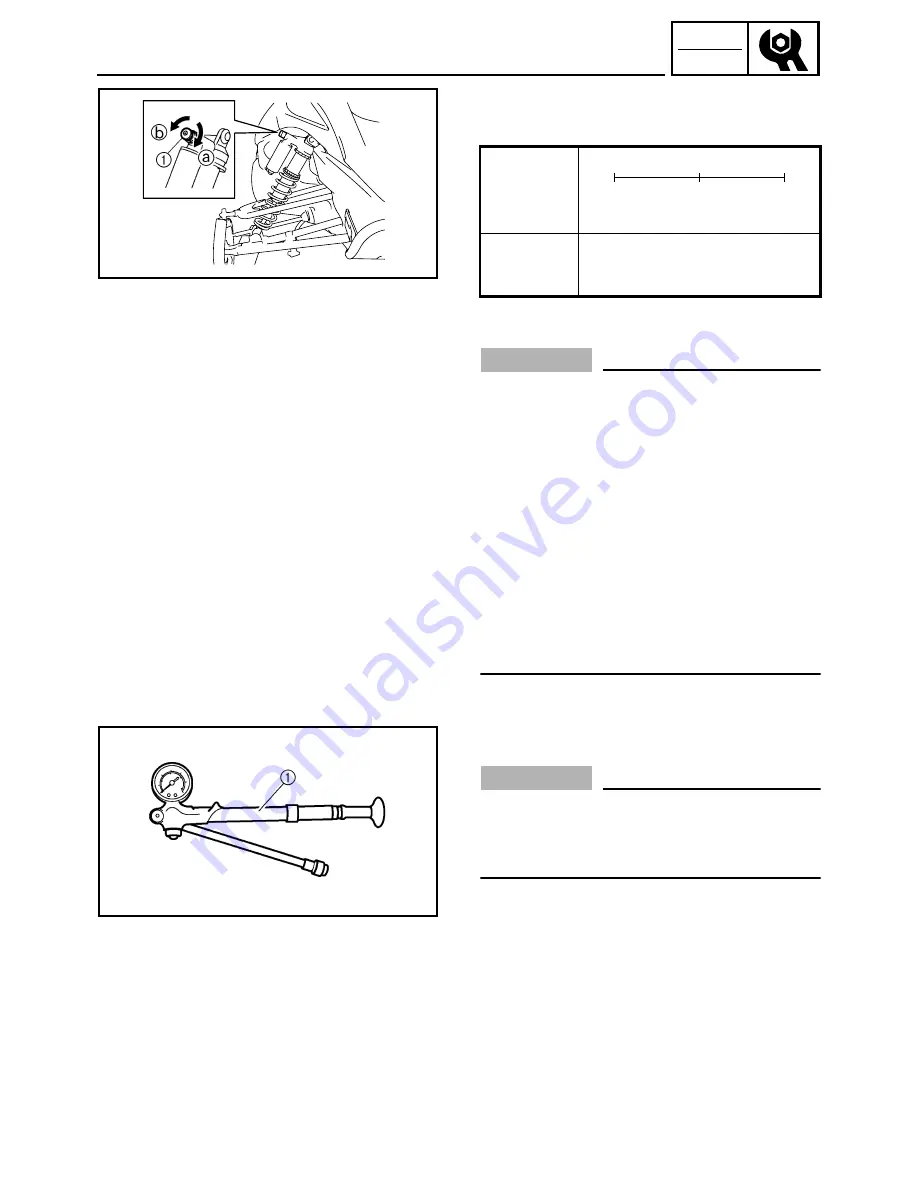
2-65
INSP
ADJ
Compression damping force adjustment (FX10)
The compression damping force can be adjusted
by turning the adjusting knob
1
.
* With the adjusting knob fully turned lightly in
direction
a
CAUTION:
• Do not continue to turn the adjusting knob in
direction
a
after it stops. The shock absorber
can be damaged and compression damping
force adjustments cannot be made.
• Do not turn the adjusting knob in direction
b
more than 12 clicks. Even if the adjusting
knob is continually turned after 12 clicks,
there will be no change in the compression
damping force.
• Be sure to stop the adjusting knob at a posi-
tion where there is a click.
• The damping forces for the left and right ski
shock absorbers must be adjusted to the
same settings. Uneven settings can cause
poor handling and loss of stability.
Adjusting
knob
position
12 clicks out
6 clicks out
2 clicks out
Minimum
Standard
Maximum
Direction
b
*
←
→
Direction
a
Compres-
sion damp-
ing force
Soft
←
→
Hard
Air pressure adjustment (FX10RT/FX10RTR/
FX10RTRA)
CAUTION:
The left and right shock absorber air pressure
must be set to the same setting. Uneven set-
tings can cause poor handling and loss of sta-
bility.
This snowmobile is equipped with FOX shock
absorbers as standard equipment.
The air pressure of the shock absorbers can be
adjusted using the shock absorber pump
1
included with your snowmobile.
Summary of Contents for FX10X 2008
Page 2: ......
Page 312: ...7 36 FI ...
Page 333: ...8 21 ELEC CHARGING SYSTEM ...
Page 341: ...8 29 ELEC LIGHTING SYSTEM ...
Page 404: ...9 43 SPEC CABLE ROUTING 9 1 2 3 4 5 6 6 7 7 8 ...
Page 406: ......
Page 407: ......