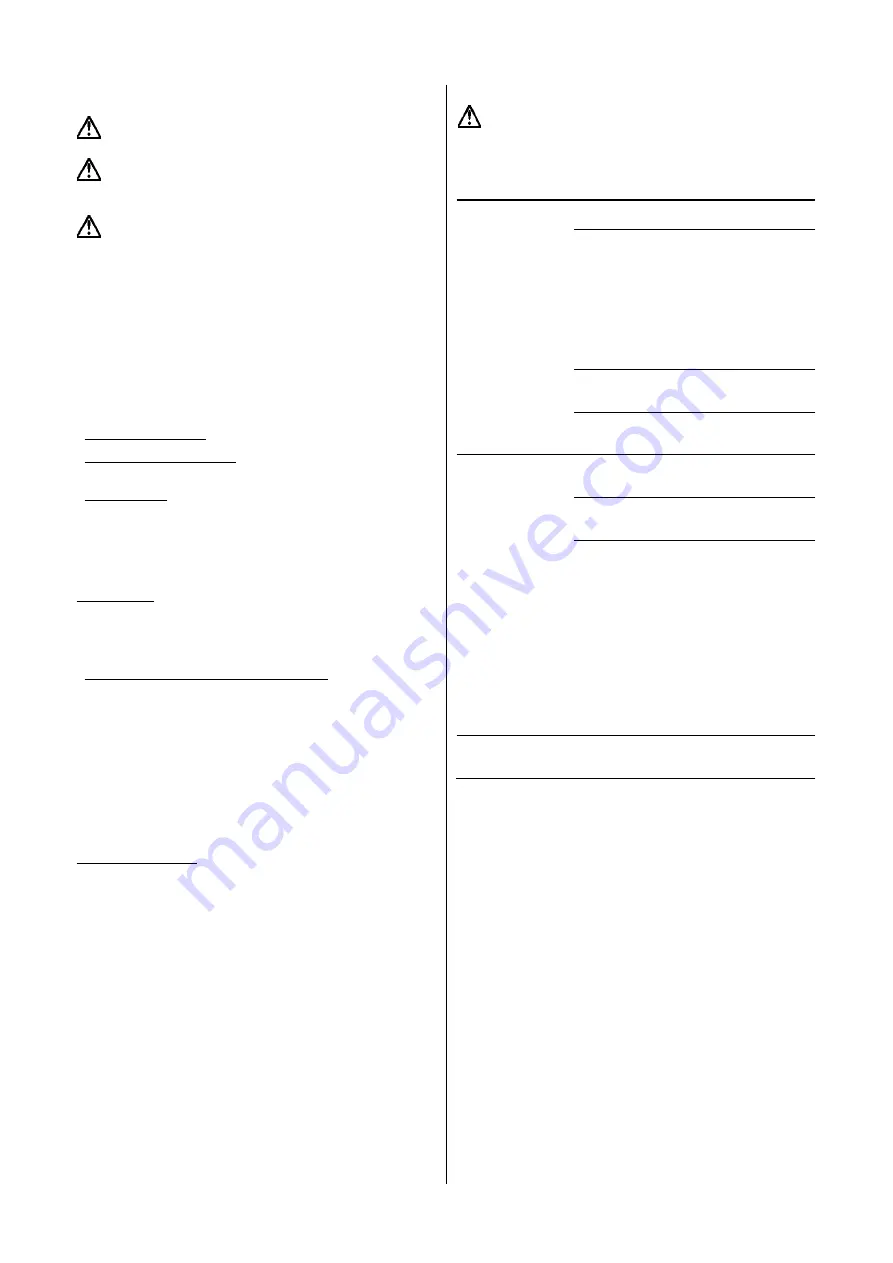
18
from the power supply to avoid accidental starting of the
pump!
Before maintenance or repair make sure that all
rotating parts stand still!
Before carrying out maintenance and service, the pump
must be thoroughly flushed with clean water. Rinse the
pump parts in clean water after dismanteling.
At pump types with oil chamber an overpressure can
escape with loosening of the oil chamber control screw.
Screw only when pressure balance took place.
Pumps running under normal operation conditions should
be inspected at least once a year. If the pumped liquid is
very muddy or sandy or if the pump is operating
continuously, the pump should be inspected every 1.000
operating hours.
For long and trouble-free operation of the pump, following
points should be checked regularly:
- Nominal current (A): Check with amp-meter.
- Pump parts and impeller: Check for possible wear.
Replace defective parts.
- Ball bearings: Check the shaft for noisy or heavy
operation (turn the shaft by hand). Replace defective ball
bearings. A general overhaul of the pump is usally required
in case of defective ball bearings or poor motor function.
This work must be carried out by an authorized service
workshop.
- Cable entry: Make sure that the cable entry is watertight
and that the cables are not bent sharply and/or pinched.
Additionally at pump types with oil chamber:
- Oil level and oil condition in oil chamber:
Put the pump in horizontal position, so that the screw of the
oil chamber is above (at larger pumps: one of both screws).
Remove the screw and infer a small quantity of oil. The oil
becomes greyish white like milk if it contains water. This
may be the result of defective shaft seal.
In this case contact our Sales and Service Department.
The oil should be replaced after 3000 operating hours.
Oil type: Shell Tellus C22. Used oil is to be disposed
accordingly.
Servicing Contract
For a regular expert execution of all necessary
maintenance and inspection we recommend the conclusion
of a servicing contract by our Sales and Service
Department.
9. Fault Finding Chart
Before maintenance or repair disconnect the pump
from the power supply to avoid accidental starting of the
pump!
Fault
Cause
Remedy
Pump does not
start
Supply failure
Check the voltage
Impeller blocked by
impurities
Close the incoming
sewer, emptying
the tank with the
diaphragm pump,
open the clening
cover, clean the
tank by hand and
remove solids
which may block
the pump
Pressure hose is
leaky or clogging
Check the hose
and clean or
replace
Fuses blow due to
use of wrong type of
fuse
Install fuses of the
correct type
Pump does not
stop
Pressure hose is
leaky or clogging
Check the hose
and clean or
replace
Control box failure
Check the control
box and replace it
if necessary
Swing check valve is
blocked or leaky
For emptying the
dischrage pipe
tightened the
drainscrew at the
swing check valve
housing. Loose the
elastic union piece
and screw off the
gate valve. Check
and clean the
swing check valve.
Never take off the
housing from the
tank.
Failure advice or
alarm advice at the
control box
see 5.2.
Summary of Contents for LOWARA Sekamatik 50 E
Page 117: ...117 1 1 1 6 1 2 1 3 DIN 4844 1 4...
Page 118: ...118 2 2 1 SEKAMATIK 50 E SEKAMATIK 50 D 2 2 SEKAMATIK 50 E SEKAMATIK 50 D 50 PC 15 100...
Page 123: ...123 A 3000 Shell Tellus C22 9 5 2...
Page 146: ...146 1 1 1 6 1 2 1 3 DIN 4844 1 4...
Page 152: ...152 3000 Shell Tellus C22 9 5 2...
Page 154: ...154 1 1 1 6 1 2 1 3 DIN 4844 1 4...
Page 155: ...155 2 2 1 SEKAMATIK 50 E SEKAMATIK 50 D 2 2 SEKAMATIK 50 E SEKAMATIK 50 D 50...
Page 157: ...157 6 10 250 5 1 DOL 5 2 5 2 1 Manu Aus Off Off Reset Auto Reset 3 2...
Page 160: ...160 1 1 7 3 5 3 8 1000 3000 Shell Tellus C22...
Page 161: ...161 9 5 2...
Page 167: ...167...