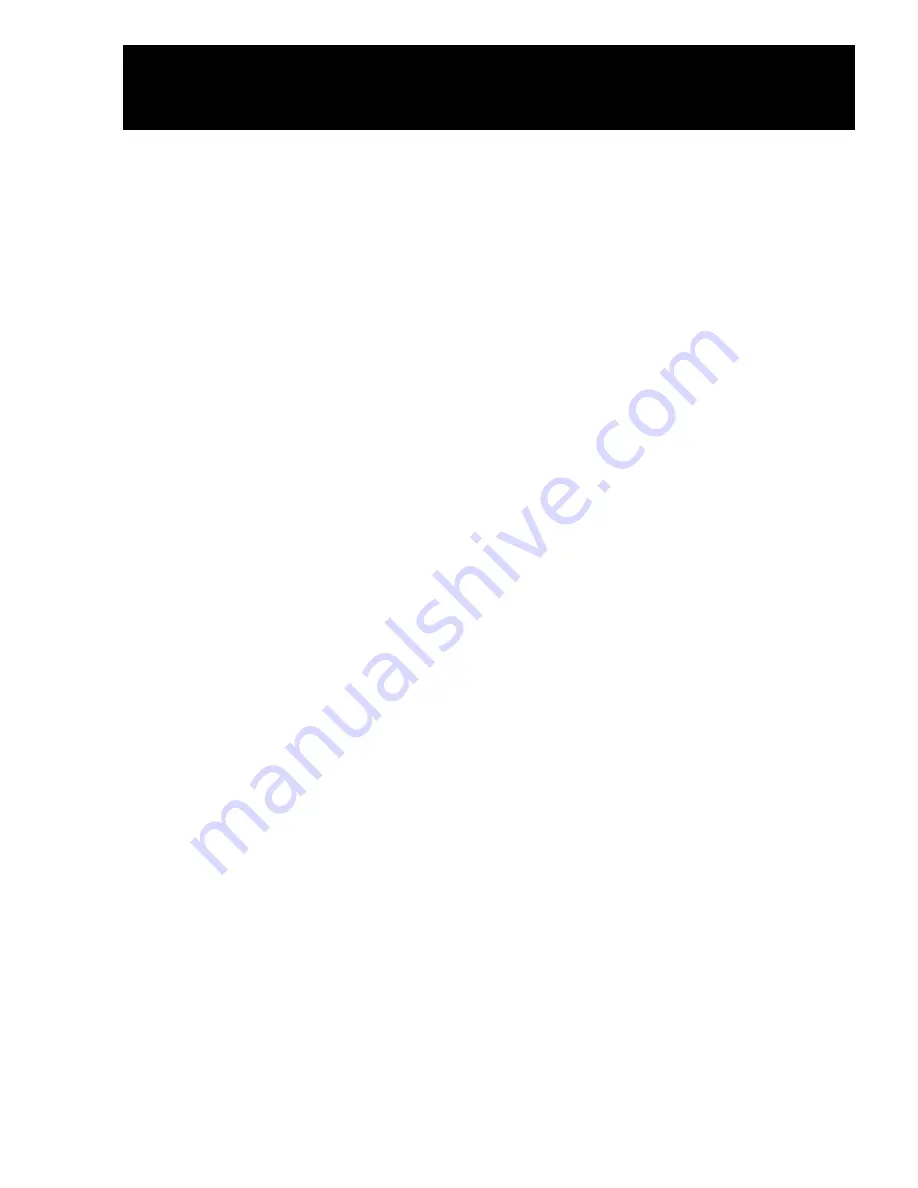
CONTENTS
SERVICING
1. TROUBLESHOOTING ....................................................................................3-S1
2. SERVICING SPECIFICATIONS ....................................................................3-S2
3. TIGHTENING TORQUES ..............................................................................3-S4
4. CHECKING, DISASSEMBLING AND SERVICING......................................3-S5
[1] CLUTCH HOUSING CASE .....................................................................3-S5
(1) Disassembling and Assembling ..........................................................3-S5
(2) Servicing ...........................................................................................3-S29
[2] TRANSMISSION CASE .........................................................................3-S31
(1) Disassembling and Assembling ........................................................3-S31
(2) Servicing ...........................................................................................3-S47
KiSC issued 03, 2007 A
Summary of Contents for ME8200
Page 1: ...WORKSHOP MANUAL TRACTOR ME8200 ME9000 KiSC issued 03 2007 A...
Page 7: ...5 ME8200 ME9000 WSM SAFETY INSTRUCTIONS KiSC issued 03 2007 A...
Page 8: ...6 ME8200 ME9000 WSM SAFETY INSTRUCTIONS KiSC issued 03 2007 A...
Page 9: ...7 ME8200 ME9000 WSM SAFETY INSTRUCTIONS KiSC issued 03 2007 A...
Page 10: ...8 ME8200 ME9000 WSM SAFETY INSTRUCTIONS KiSC issued 03 2007 A...
Page 11: ...9 ME8200 ME9000 WSM SAFETY INSTRUCTIONS CABIN TYPE KiSC issued 03 2007 A...
Page 12: ...10 ME8200 ME9000 WSM SAFETY INSTRUCTIONS KiSC issued 03 2007 A...
Page 13: ...11 ME8200 ME9000 WSM SAFETY INSTRUCTIONS KiSC issued 03 2007 A...
Page 16: ...14 ME8200 ME9000 WSM DIMENSIONS DIMENSIONS ROPS TYPE KiSC issued 03 2007 A...
Page 17: ...15 ME8200 ME9000 WSM DIMENSIONS CABIN TYPE KiSC issued 03 2007 A...
Page 18: ...G GENERAL KiSC issued 03 2007 A...
Page 94: ...1 ENGINE KiSC issued 03 2007 A...
Page 178: ...2 CLUTCH KiSC issued 03 2007 A...
Page 213: ...3 TRANSMISSION KiSC issued 03 2007 A...
Page 273: ...4 REAR AXLE KiSC issued 03 2007 A...
Page 274: ...CONTENTS MECHANISM 1 STRUCTURE 4 M1 KiSC issued 03 2007 A...
Page 290: ...5 BRAKES KiSC issued 03 2007 A...
Page 308: ...6 FRONT AXLE KiSC issued 03 2007 A...
Page 309: ...CONTENTS MECHANISM 1 STRUCTURE 6 M1 2 FRONT WHEEL ALIGNMENT 6 M2 KiSC issued 03 2007 A...
Page 333: ...7 STEERING KiSC issued 03 2007 A...
Page 334: ...CONTENTS MECHANISM 1 STEERING MECHANISM 7 M1 KiSC issued 03 2007 A...
Page 342: ...8 HYDRAULIC SYSTEM KiSC issued 03 2007 A...
Page 429: ...9 ELECTRICAL SYSTEM KiSC issued 03 2007 A...
Page 483: ...10 CABIN KiSC issued 03 2007 A...
Page 494: ...10 S3 ME8200 ME9000 WSM CABIN Air Conditioning System Continued KiSC issued 03 2007 A...
Page 495: ...10 S4 ME8200 ME9000 WSM CABIN KiSC issued 03 2007 A...
Page 496: ...10 S5 ME8200 ME9000 WSM CABIN KiSC issued 03 2007 A...