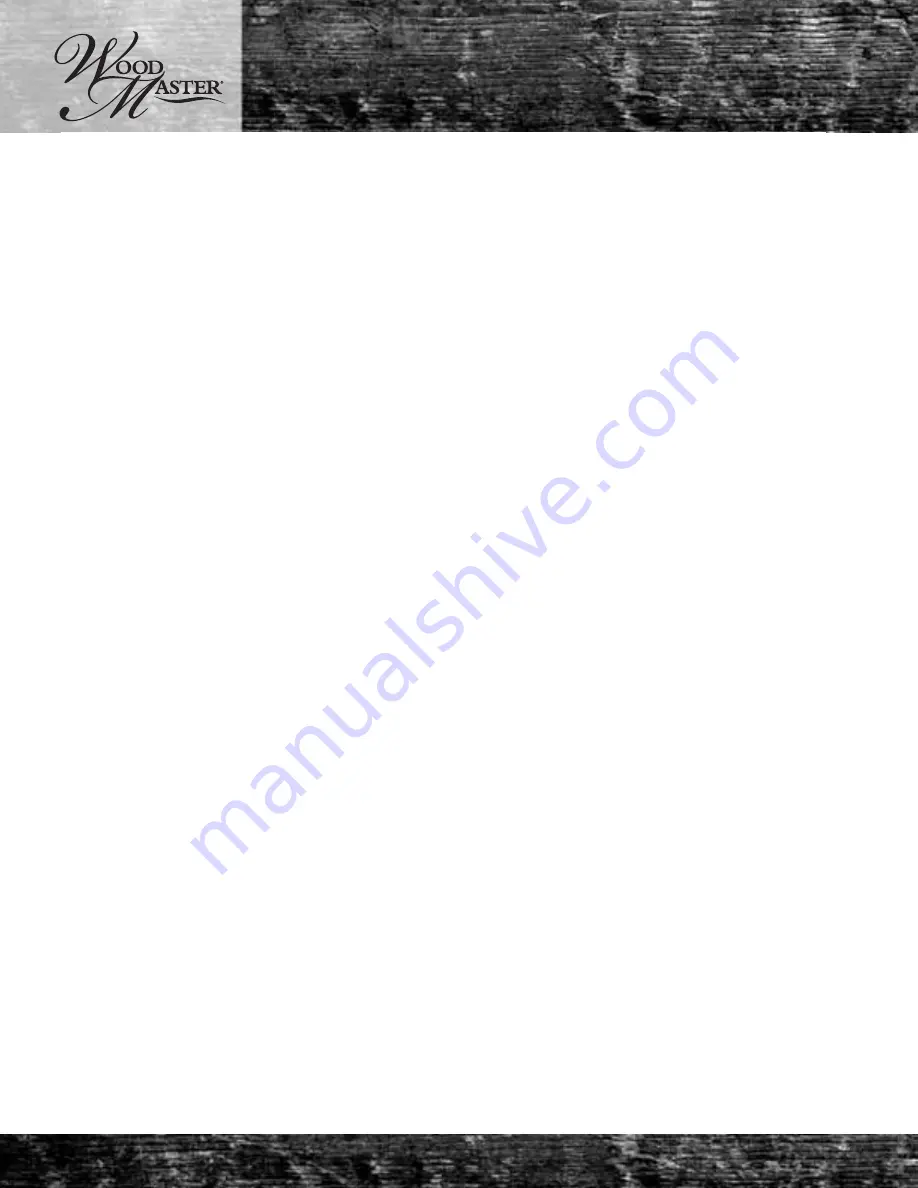
40
CleanFire Owners Manual
2016
Warranty
This Warranty is provided by Northwest Manufacturing, Inc. only for the benefit of the initial purchaser (Original Owner) of the
Northwest Manufacturing, Inc. WoodMaster CleanFire (the “Boiler”) on the original site of installation (the “Site of Original Installa-
tion”). This Warranty provides specific legal rights. You may have other rights depending on where you live.
The rights in this warranty depend on the proper assembly, installation and commissioning of the Boiler by a dealer or installer who
is certified by Northwest Manufacturing, Inc. (the “Certified Contractor”); and proper operation and maintenance. Proper mainte-
nance in accordance with the Maintenance Intervals (as defined in the owners manual) must be performed. Installation by an
uncertified or unqualified contractor or installer and/or improper maintenance, operation, misuse or abuse of the Boiler shall void
this Warranty in whole or in part. All portions of the Warranty are subject to the Warranty Limitations.
LIMITED TWENTY FIVE (25) YEAR WARRANTY FOR THE FIRE CHAMBER
Northwest Manufacturing, Inc. warrants that the Fire Chamber shall be free of defects in material and workmanship for TEN (10)
YEARS from the Date of Original Installation. If there is a defect in your properly delivered and installed WoodMaster CleanFire in
the first Ten (10) years, WoodMaster will replace the Fire Chamber at no cost to the original owner. Northwest Manufacturing,Inc.
will only pay these percentages of costs of warranty work per year, years Eleven (11) through Fifteen (15) – 50% of warranty work.
Years Sixteen through Twenty Five (16-25) 25% of warranty work. Once a defect is determined, repair or replacement of the Fire
Chamber, in a whole or part, will be at the sole discretion of Northwest Manufacturing, Inc..
LIMITED TWENTY FIVE (25) YEAR WARRANTY FOR THE PRESSURE VESSELS
Northwest Manufacturing, Inc. warrants that the Pressure Vessels shall be free of defects in material and workmanship for FIVE (5)
YEARS from the Date of Original Installation. If there is a defect in your properly delivered and installed WoodMaster CleanFire in
the first 5 years, WoodMaster will replace the Pressure Vessel at no cost to the original owner. Northwest Manufacturing, Inc. will
only pay costs of warranty work for year Six (6) – 70% of warranty work, the Seventh (7) year – 60% of warranty work, the Eighth
(8) year – 40% of warranty work, the Ninth (9) year – 20%of warranty work, the Tenth (10) year – 10% of warranty work. Years
eleven through twenty (11-20) WoodMaster will give you a 10% discount on the purchase of a new WoodMaster Boiler. (Boiler
only) Years Twenty One through Twenty Five (21-25) WoodMaster will give you a 5% discount on the purchase of a new Wood-
Master furnace. Once a defect is determined, repair or replacement of the Pressure Vessel, in a whole or part, will be at the sole
discretion of Northwest Manufacturing, Inc..
LIMITED ONE (1) YEAR WARRANTY ON THE ELECTRICAL COMPONENTS
Northwest Manufacturing, Inc. warrants to the Original Owner, that any electrical components are free from defects for the period
of ONE (1) YEAR from the date of installation. Northwest Manufacturing, Inc. will determine whether to repair or replace the defec-
tive parts.
LIMITED ONE (1) YEAR WARRANTY ON CATALYTIC COMBUSTOR
Northwest Manufacturing, Inc. warrants to the original owner only, the Catalytic Combustor during normal usage for a period of
ONE (1) YEAR from the date of installation. This does not cover damage from excessive heat to the Catalytic Combustor, which
will result in visible damage to the Catalytic Combustor.
LIMITED ONE (1) YEAR WARRANTY ON ADDITIONAL COMPONENTS
Northwest Manufacturing, Inc. warrants to the original owner only, any additional components, including, but not limited to the
outer shell, paint, insulation, doors and latches during normal usage for a period of ONE (1) YEAR from the date of installation.
This does not include door seals and other seals on the boiler.
START OF WARRANTY PERIODS
The Warranty Period shall begin on the date the Boiler installation has been completed (the “Original Date of Installation”). In the
event of dispute as to the Date of Original Installation, the shipping date of your Boiler, as recorded by Northwest Manufacturing,
Inc., shall be deemed to be the Date of Original Installation.
WARRANTY LIMITATIONS
I. Damages for unsatisfactory performance caused by improper installation or any damages caused by or as a result of improper
use of the Boiler , incorrect start-up, incorrect or careless handling, improper control adjustment, incorrect chimney installation or
draft, disregard of the operating instructions and proper maintenance or disregard of any other instructions supplied with the
Boiler, improper operation of the Boiler or improper alteration and repairs/service by a third party not affiliated with Northwest
Manufacturing, Inc. will not be covered under this warranty. All repairs must be performed by a Certified Contractor.
II. The warranty will not cover damage to parts caused by improper installation, improper care or maintenance. The Boiler, and any
installed accessories must be serviced, inspected and cleaned at regular intervals. Northwest Manufacturing, Inc. will NOT warranty
damage to the Boiler due to ash corrosion.
III. The workmanship, repairs or replacement of parts of the Certified Contractor will not be covered under this warranty.
IV. Components of the heating system not furnished by Northwest Manufacturing, Inc. are not covered under this Warranty.
Damages to the Boiler caused by components of the heating system not supplied by Northwest Manufacturing, Inc. will not be
covered under this Warranty.
V. Fuels used in the Boiler must meet the specifications set out in the owners manual by Northwest Manufacturing, Inc.. Damage
caused by the use of any unapproved fuel, or any fuel that does not meet the guidelines set forth by Northwest Manufacturing,
Inc. will not be covered by this warranty. Failure to properly load the Boiler will result in a voided warranty.
VI. Any costs for labor for the examination, removal or reinstallation of allegedly defective parts, transportation of the parts to and
from Northwest Manufacturing, Inc. facilities will not be covered and will be the responsibility of the Original Owner. This includes
any other labor and costs for any material necessary for the said examination, removal or re-installation.
VII. The warranty will not cover damage to the Boiler or any original parts, replacement parts or other accessories or standard
equipment caused by excessive temperatures or pressures, vandalism, fuel or gas explosion, electrical, chemical or electrochemi-
cal reaction, electrical failures, insurrection, riots, war, acts of God, combustion air contaminated externally, air impurities, sulfur or
sulfuric action or reaction, dust particles, corrosive vapors, oxygen corrosion, improper fuel loading and situating the Boiler in an
unsuitable location or continuing use of the Boiler after onset of a malfunction or discovery of a defect.
VIII. The warrany will be void if there is continued use after Catalyst failure.
IV. Consumable parts, and parts in direct contact with the flame, will not be covered under this warranty.
WARRANTY TERMS
The Warranty shall also be subject to the following terms and conditions:
I. The Boiler must have been installed by a Certified Contractor.
II. The Boiler must have been properly maintained, cleaned and serviced during the Warranty Periods in accordance to the manual.
III. This Warranty is non transferable and only covers the Original Owner, at the original site of installation.
IV. Northwest Manufacturing, Inc. shall have the time needed and unobstructed access to the Boiler for the purpose of conducting
tests of the Boiler and for the making of repairs or installation of replacement parts.
V. Repairs, replacement or the repair of replacement parts shall be subject to the terms and conditions of this Warranty as if they
had been installed at the time of original installation.
VI. This Warranty is limited to the provisions previously described and does not extend to any Boiler and Burner, related parts or
products that are (a) not sold in Canada or the United States; (b) not installed in Canada or the United States; or (c) not purchased
from an Authorized Distributor.
VII. Northwest Manufacturing, Inc. shall not be responsible for any consequential damages, direct or indirect caused by the
products described in this Warranty.
VIII. The warranty registration card must be returned within 10 days from installation.
APPLICABLE LAW
All disputes or claims on the Warranty shall be determined in accordance with the laws of Red Lake County, Minnesota.
WARRANTY CLAIM/SERVICE
Notify the Certified Contractor who installed your Boiler. The Contractor will then notify Northwest Manufacturing, Inc. who will
make all warranty decisions. No warranty work can be carried out without approval from Northwest Manufacturing, Inc.. If the
Certified Contractor fails to make a warranty claim, contact Northwest Manufacturing, Inc. directly. Allegedly defective parts MUST
be returned to Northwest Manufacturing, Inc. for the purpose of inspection to determine cause of failure.
Northwest Manufacturing, Inc. / 600 Polk Ave. SW / Red Lake Falls, MN 56750-5002
(800) 932-3629 • Fax: (218) 253-4409 / www.woodmaster.com