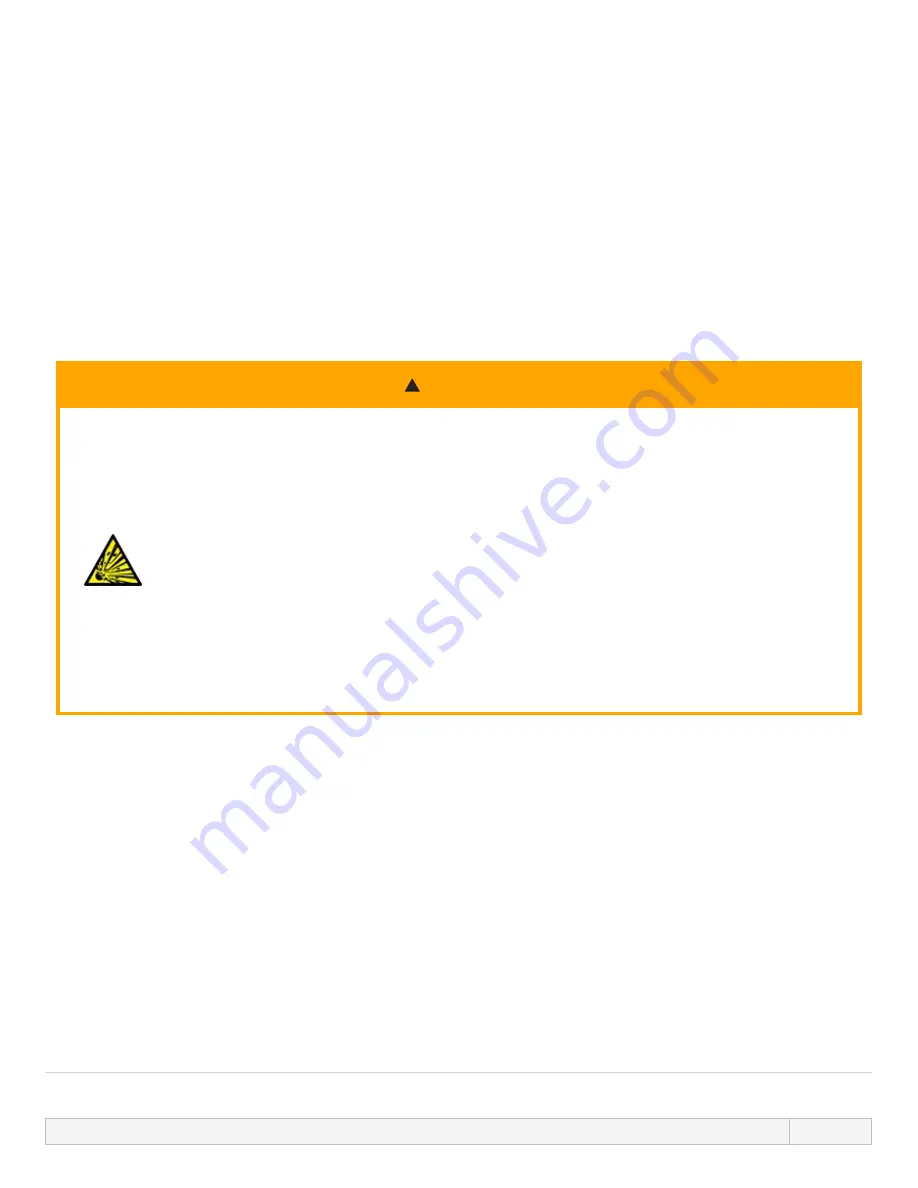
18.3.3 Leak detection procedure
As soon as a leak is detected either as a result of a message on the screen, the remote model icons, or due to
observing a fluid leak from the pumphead. The following procedure must be immediately followed
1. Isolate the pump from electrical power
2. Remove the pump from service in accordance with the users organisations procedure
3. Determine the cause of the leak
4. Follow the procedure provided in maintenance to replace the pump head. This procedure includes an
inspection for chemical residue.
5. Bring the pump back into service
6. Reconnect electrical power to the pump
7. Reset the leak detection message
!
WARNING
Operating the pumphead to the point of failure may result in a flow of chemicals into the
pumphead to drive interface area, as a result of aggressive chemicals which are not
compatible with the internal pumphead materials.
Chemicals could attack the materials in this area and enter the drive. The internal parts of the
drive unit contain Aluminium which may react with some aggressive chemicals to form an
explosive gas.
If you are pumping a chemical that may react with Aluminium to form an explosive gas, do not
operate the pump to the point of pumphead failure. In addition, you must ensure the
chemicals being pumped are chemically compatible with the materials in the pumphead to
drive interface area: Drive casework, Drive casework seals, Drive shaft, Drive shaft seal.
In the event of a pumphead failure or a leak detection notification event. Stop the pump,
remove from service and follow the pumphead replacement procedure in
.
18 ERRORS, BREAKDOWN AND TROUBLESHOOTING
197