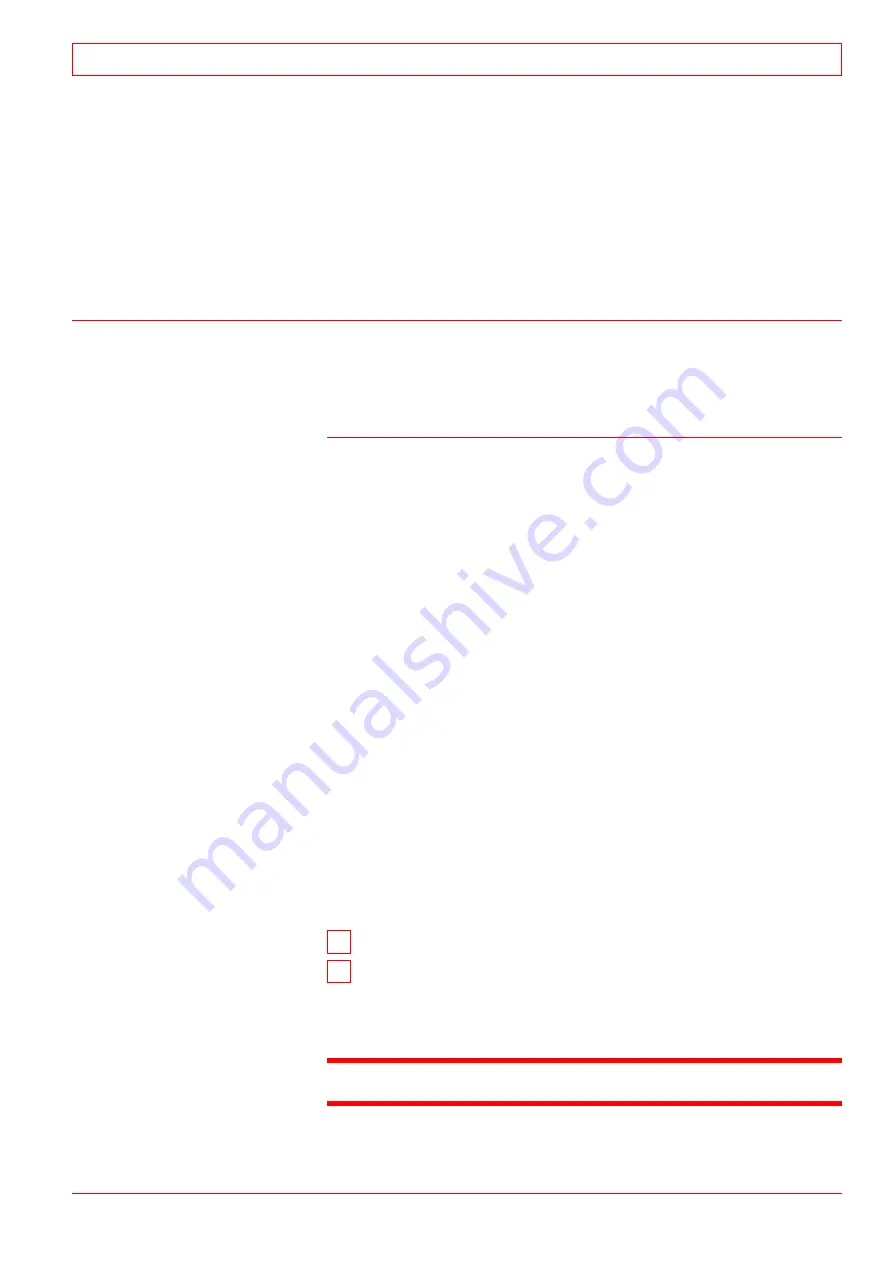
Even if the above mentioned sensors are considered as standard
the amount and type of sensors can in special cases vary, depend-
ing on the needs for various installations. The actual set of sensors
and other electrical equipment mounted on the engine, as well as
alarm, load reduction and shutdown set points, can be found in
the installation specific documentation.
23.3
Functional testing
In this section there are described the procedures for testing of
overspeed trip and pressure sensors.
23.3.1 Testing of overspeed trip
There are two sensors measuring the engine speed. One sensor
(ST173) is connected to DCU1 and the other sensor (ST174) is
connected to the Relay Module. Overspeed is detected by both
sensors.
The overspeed limit set in the DCU is lower than the overspeed
limit set in the Relay Module. The limit of overspeed in the DCU
is 15 % above the engine nominal speed. The limit of overspeed
in the Relay Module is 18% above the engine nominal speed.
The overspeed trip can be tested by actually running the engine
at overspeed if that is possible. Otherwise the testing has to be
done by simulating the engine speed with a signal generator.
The overspeed trip should stop the engine when the overspeed
limit is exceeded. There is one exception to this. If a single main
engine exceeds the 15 % overspeed limit, the stop solenoids will
be activated only until the engine speed is below nominal speed.
The auxiliary engines will be stopped even when the lower
overspeed limit is exceeded. The overspeed limit of the Relay
Module is used as a backup and is always latching.
23.3.1.1 Testing of the overspeed trip by running the
engine
The overspeed trip can be tested by running the engine at
overspeed. The speed of the engine is not allowed to be increased
more than 60 rpm over the overspeed limit.
1 Increase the engine speed.
2 Check at what speed the overspeed is detected.
The limit of overspeed will be first exceeded in the DCU1. When
testing the overspeed trip of the Relay Module the speed sensor
of the DCU1 (ST173) has to be disconnected.
Note!
Do not forget to connect the speed sensor after testing!
32-200115/II
Instrumentation and Automation
23
WÄRTSILÄ 32
23-7
Summary of Contents for VASA 6L32
Page 4: ......
Page 18: ...Appendix B Welding Precautions 200640 00 6...
Page 26: ...01 Main Data Operating Data and General Design 32 200634 01 01 8 W RTSIL 32...
Page 60: ...Appendix A Environmental Hazards 200507 02A 10...
Page 68: ...Page 7 7 Document No 4V92A0645 Rev j...
Page 84: ...03 Start Stop and Operation 32 200402 04 03 12 W RTSIL 32...
Page 98: ...04 Maintenance Schedule 32 200623 01 04 14 W RTSIL 32...
Page 154: ...07 Tightening Torques and Use of Hydraulic Tools 32 200643 01 07 30 W RTSIL 32...
Page 162: ...08 Operating Troubles Emergency Operation 32 200402 01 08 8 W RTSIL 32...
Page 164: ...Specific Installation Data 2005 01 09 2...
Page 178: ...10 Engine Block with Bearings Oil Sump and Cylinder Liner 32 200150 10 14 W RTSIL 32 34SG...
Page 216: ...Appendix A Testing of cylinder tightness 32 200142 A 4 W rtsil 20 32 34...
Page 226: ...13 Camshaft Driving Gear 32 200546 02 13 10 W RTSIL 32...
Page 254: ...15 Turbocharging and Air Cooling 32 200549 10 15 20 W RTSIL 32...
Page 274: ...16 Injection System 32 200627 01 16 20 W RTSIL 32...
Page 280: ...Fuel System 32 200508 07 17 6 W RTSIL 32...
Page 314: ...19 Cooling Water System 32 200050 19 14 W RTSIL 32...
Page 394: ...23 Instrumentation and Automation 32 200115 II 23 60 W RTSIL 32...