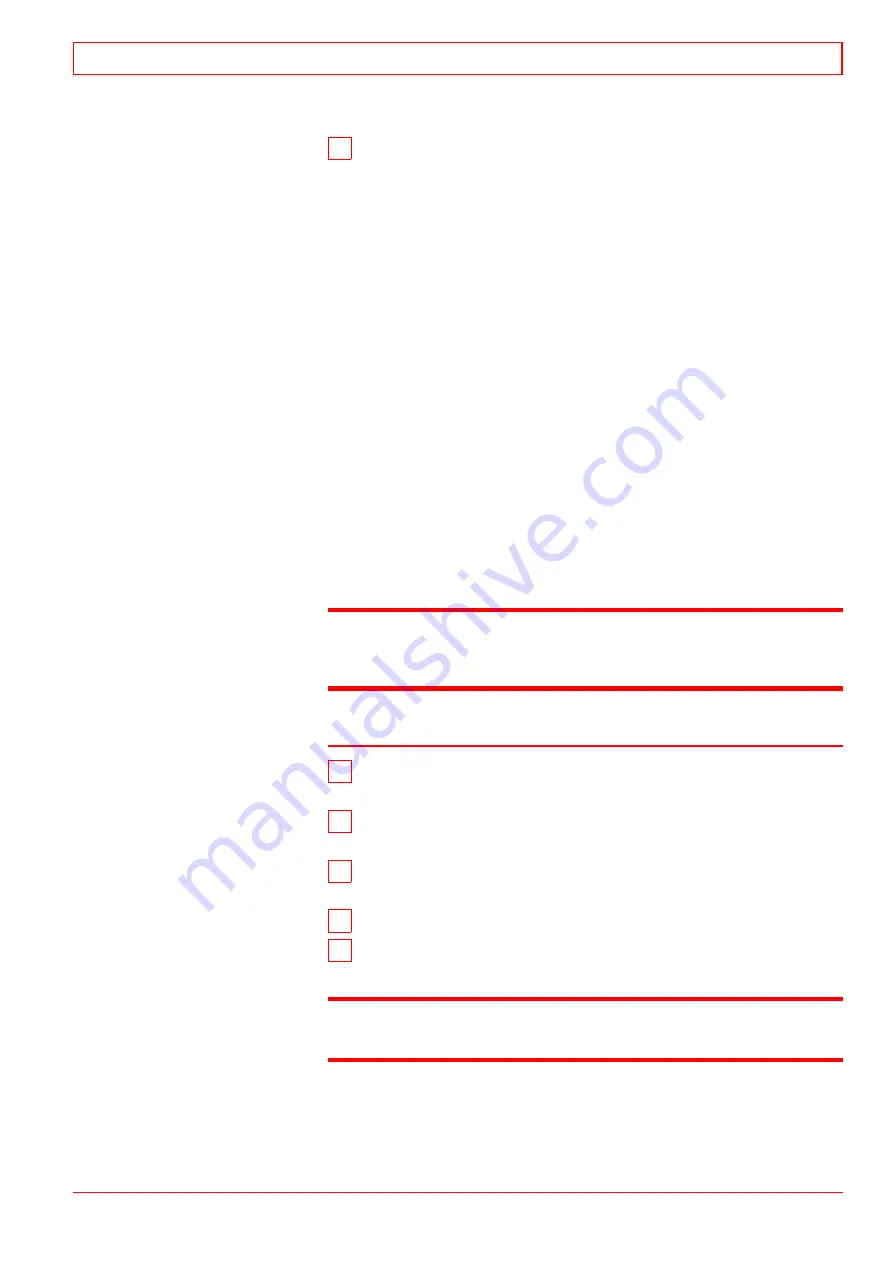
9 Following limits of misalignment
are stated for an engine
having normal running temperature (within 10 min after run-
ning at 60 % load, or higher, for 6 h, or more):
For evaluating the vertical alignment should the difference be-
tween C and it’s opposite reading, i.e. the mean value E and A be
used.
a)
on the same crank, the difference between two diametrically
opposed readings must not exceed 0.08 mm after installing or
re-aligning. Re-alignment is necessary if this limit is exceeded by
more than 0.04 mm. Except the cranks in the both ends.
b)
on two adjacent cranks, the difference between two corre-
sponding readings must not exceed 0.06 mm, for crank No.1 to
No.2 0.08 mm if flex. coupling and 0.06 mm if fixed coupling.
Re-alignment is necessary if these limits are exceeded by more
than 0.02 mm.
c)
when the crank pin for cyl.1 is at TDC, the reading should
be negative, max. -0.12 mm (-0.13 mm if flex. coupling).
d)
when the last crank pin in the free end is at TDC in case
of PTO with support bearing, should the reading be positive
max. 0.13 mm.
Before re-aligning the engine and the driven machinery, a
control measurement of the main bearings should be made.
Note!
In an engine having a normal ambient temperature, the cor-
responding values must be based on experiences from the
particular installation.
11.2.3 Measurement of thrust bearing axial clearance
1 Lubricate the bearings
by running the prelubricating
pump for a few minutes.
2 Apply a measure gauge,
for instance, against the plane
end surface of the flywheel.
3 Move the crankshaft
by a suitable lever in either direc-
tion until contact is established with the thrust bearing.
4 Set the measure gauge at zero.
5 Move the crankshaft
in the opposite direction, and read
the axial clearance from the measure gauge.
Note!
Repeat the movement of crankshaft to ensure that correct
clearance is measured.
32-200020
Crank Mechanism: Crankshaft, Connecting Rod, Piston
11
WÄRTSILÄ 32
11 - 3
Summary of Contents for VASA 6L32
Page 4: ......
Page 18: ...Appendix B Welding Precautions 200640 00 6...
Page 26: ...01 Main Data Operating Data and General Design 32 200634 01 01 8 W RTSIL 32...
Page 60: ...Appendix A Environmental Hazards 200507 02A 10...
Page 68: ...Page 7 7 Document No 4V92A0645 Rev j...
Page 84: ...03 Start Stop and Operation 32 200402 04 03 12 W RTSIL 32...
Page 98: ...04 Maintenance Schedule 32 200623 01 04 14 W RTSIL 32...
Page 154: ...07 Tightening Torques and Use of Hydraulic Tools 32 200643 01 07 30 W RTSIL 32...
Page 162: ...08 Operating Troubles Emergency Operation 32 200402 01 08 8 W RTSIL 32...
Page 164: ...Specific Installation Data 2005 01 09 2...
Page 178: ...10 Engine Block with Bearings Oil Sump and Cylinder Liner 32 200150 10 14 W RTSIL 32 34SG...
Page 216: ...Appendix A Testing of cylinder tightness 32 200142 A 4 W rtsil 20 32 34...
Page 226: ...13 Camshaft Driving Gear 32 200546 02 13 10 W RTSIL 32...
Page 254: ...15 Turbocharging and Air Cooling 32 200549 10 15 20 W RTSIL 32...
Page 274: ...16 Injection System 32 200627 01 16 20 W RTSIL 32...
Page 280: ...Fuel System 32 200508 07 17 6 W RTSIL 32...
Page 314: ...19 Cooling Water System 32 200050 19 14 W RTSIL 32...
Page 394: ...23 Instrumentation and Automation 32 200115 II 23 60 W RTSIL 32...