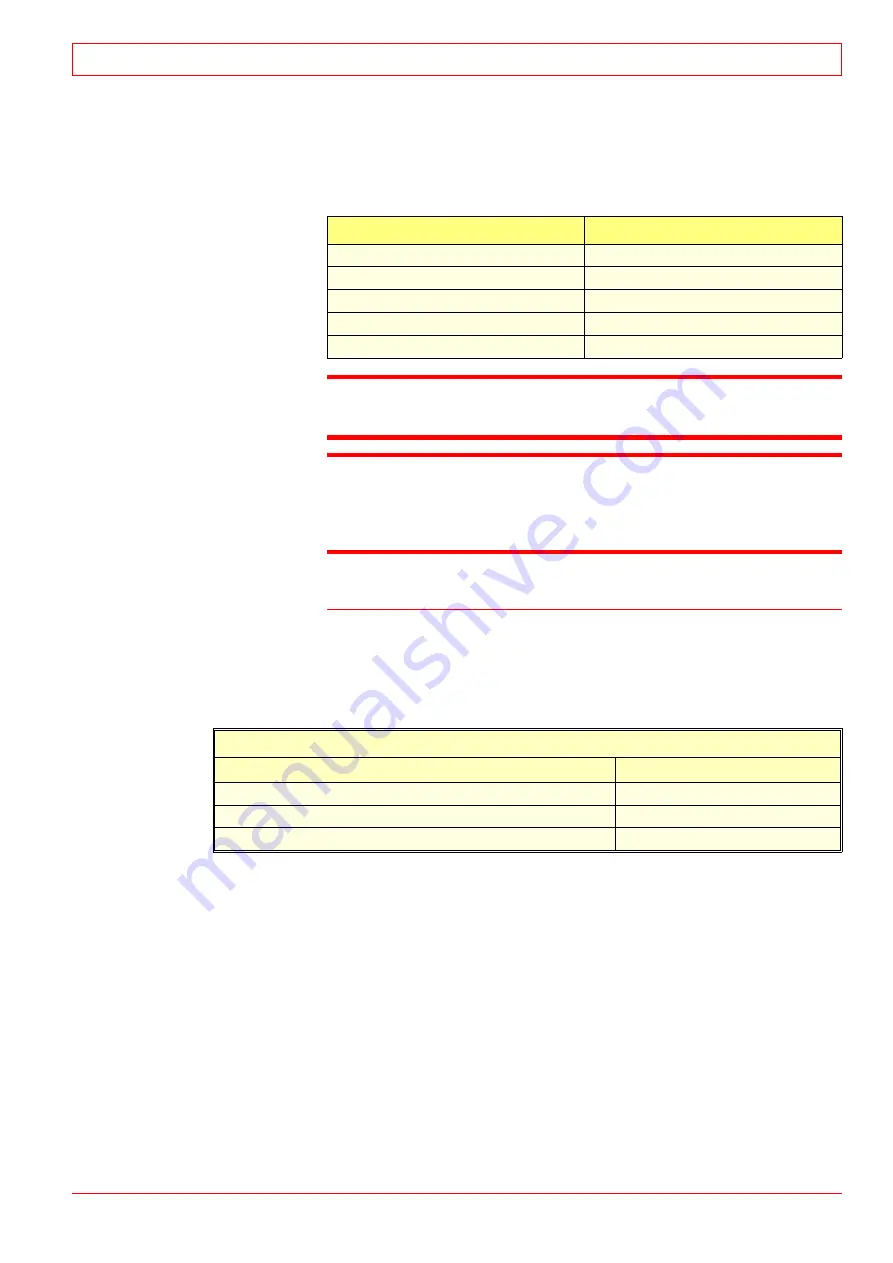
x)
Pos. 6 see installation instructions.
The stud bolts are tightened to the casting at the following
torques:
Screw dimension
Tightening torque (Nm)
M56 Cylinder head
400
±
20
M56 Main Bearing
300
±
10
All M27 studs on connecting rod
100
±
10
M42 and M48 x 3
200
±
10
M80 Intermediate gear
200
±
10
Exception!
Screws acc. to pos. 3 and 6.
Pos. 3 see chapter 10, section 10.3.3.
Caution!
The screws will be overloaded if the maximum hydraulic
pressure is exceeded.
It is recommended to change the screws if maximum hydrau-
lic pressure is exceeded for some reason.
07.3.2 Hydraulic Tool Safety Instructions
Since the hydraulic tools operate under high pressure and pro-
duce great force, proper safety precautions must be taken to
reduce the risk of injury to persons and damage to material during
work on the engine and in the workshop.
Hydraulic tool lifetime
Tool Load
cycles
(approx.)
Piston in cylindrical hydraulic tools (see Fig 07-24)
1 000
Screws in "twin cylinder" hydraulic tool (see Fig 07-23)
1 000
Hydraulic hoses and couplings
10 000
There are two types of hydraulic tools for the connecting rod shank
screws, see Fig 07-23. The screws and nuts in the tool of
new
design
(introduced in year 2001) should be replaced before
reaching
1000
loading cycles, i.e raising the pressure to nominal
value 1000 times)
The screws and nuts of
previous design,
see
Fig 07-23, should
be replaced before reaching
250
loading cycles.
If the hydraulically tensioned nuts not easily can be turned when
the maximum hydraulic pressure is reached: check for corrosion
in threads; check tool condition and manometer error.
32-200643-01
Tightening Torques and Use of Hydraulic Tools
07
WÄRTSILÄ 32
07 - 23
Summary of Contents for VASA 6L32
Page 4: ......
Page 18: ...Appendix B Welding Precautions 200640 00 6...
Page 26: ...01 Main Data Operating Data and General Design 32 200634 01 01 8 W RTSIL 32...
Page 60: ...Appendix A Environmental Hazards 200507 02A 10...
Page 68: ...Page 7 7 Document No 4V92A0645 Rev j...
Page 84: ...03 Start Stop and Operation 32 200402 04 03 12 W RTSIL 32...
Page 98: ...04 Maintenance Schedule 32 200623 01 04 14 W RTSIL 32...
Page 154: ...07 Tightening Torques and Use of Hydraulic Tools 32 200643 01 07 30 W RTSIL 32...
Page 162: ...08 Operating Troubles Emergency Operation 32 200402 01 08 8 W RTSIL 32...
Page 164: ...Specific Installation Data 2005 01 09 2...
Page 178: ...10 Engine Block with Bearings Oil Sump and Cylinder Liner 32 200150 10 14 W RTSIL 32 34SG...
Page 216: ...Appendix A Testing of cylinder tightness 32 200142 A 4 W rtsil 20 32 34...
Page 226: ...13 Camshaft Driving Gear 32 200546 02 13 10 W RTSIL 32...
Page 254: ...15 Turbocharging and Air Cooling 32 200549 10 15 20 W RTSIL 32...
Page 274: ...16 Injection System 32 200627 01 16 20 W RTSIL 32...
Page 280: ...Fuel System 32 200508 07 17 6 W RTSIL 32...
Page 314: ...19 Cooling Water System 32 200050 19 14 W RTSIL 32...
Page 394: ...23 Instrumentation and Automation 32 200115 II 23 60 W RTSIL 32...