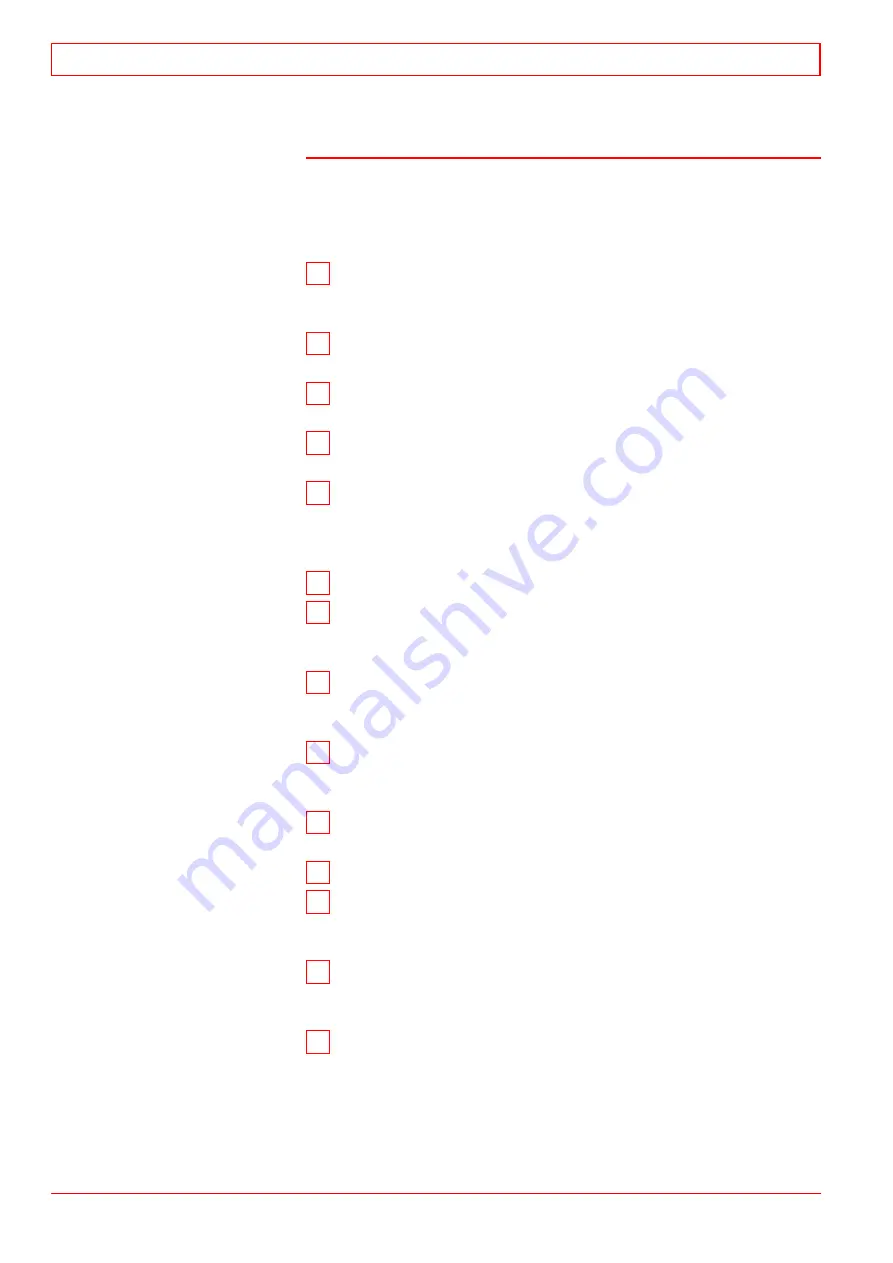
21.3.2 Maintenance
Normally, the starting air distributor does not need maintenance.
If it has to be opened for control and cleaning, remove the complete
distributor from the engine. Certain pistons can be checked in
situ.
1 Remove the end plate (11).
Loosen all pipes from the
distributor. Remove the fastening screws and lift the distribu-
tor off.
2 Remove the plugs (17)
at which the pistons (15) will
come out forced by the springs (14).
3 Take care not to damage the sliding surfaces of pistons
and liners.
4 In case of a stuck piston, use thread M8
at the end of
the piston to get it out, if necessary.
5 It is recommended not to change the place of the
pistons,
although they are precision machined to be inter-
changeable. Utilize cylinder numbers stamped at the control
air connections.
6 Clean the parts and check for wear.
7 If a liner is worn, press it out.
It may be necessary to heat
the distributor up to about 200°C as Loctite is used for fixation
and sealing.
8 Clean the bore
carefully so that the new liner can be
inserted by hand. Otherwise there is a risk of deformation of
the liner and sticking of the piston.
9 Apply Loctite 242
on the outside surfaces when mounting
the liner. Check that the openings in the liner correspond to
those in the housing.
10 Check that there is no Loctite
on the inside sliding sur-
faces.
11 Renew the O-rings
inside the liners.
12 Apply Molykote Paste G
to the piston sliding surfaces
before reassembly. Wipe off surplus paste. Check that pistons
do not stick.
13 Apply silicon sealant
to both sides of the intermediate
plate (13). Do not use too much as surplus sealant will be forced
into the system when tightening the fastening screws.
14 After mounting the distributor
to the engine but before
connecting the control air pipes and end plate (11), check that
all pistons work satisfactorily, e.g. by connecting compressed
air (working air of 6 bar) to the distributor air inlet and by
turning the crankshaft. It is then possible to see whether the
pistons follow the cam profile.
21
Starting Air System
32-200202-01
21 - 4
WÄRTSILÄ 32
Summary of Contents for VASA 6L32
Page 4: ......
Page 18: ...Appendix B Welding Precautions 200640 00 6...
Page 26: ...01 Main Data Operating Data and General Design 32 200634 01 01 8 W RTSIL 32...
Page 60: ...Appendix A Environmental Hazards 200507 02A 10...
Page 68: ...Page 7 7 Document No 4V92A0645 Rev j...
Page 84: ...03 Start Stop and Operation 32 200402 04 03 12 W RTSIL 32...
Page 98: ...04 Maintenance Schedule 32 200623 01 04 14 W RTSIL 32...
Page 154: ...07 Tightening Torques and Use of Hydraulic Tools 32 200643 01 07 30 W RTSIL 32...
Page 162: ...08 Operating Troubles Emergency Operation 32 200402 01 08 8 W RTSIL 32...
Page 164: ...Specific Installation Data 2005 01 09 2...
Page 178: ...10 Engine Block with Bearings Oil Sump and Cylinder Liner 32 200150 10 14 W RTSIL 32 34SG...
Page 216: ...Appendix A Testing of cylinder tightness 32 200142 A 4 W rtsil 20 32 34...
Page 226: ...13 Camshaft Driving Gear 32 200546 02 13 10 W RTSIL 32...
Page 254: ...15 Turbocharging and Air Cooling 32 200549 10 15 20 W RTSIL 32...
Page 274: ...16 Injection System 32 200627 01 16 20 W RTSIL 32...
Page 280: ...Fuel System 32 200508 07 17 6 W RTSIL 32...
Page 314: ...19 Cooling Water System 32 200050 19 14 W RTSIL 32...
Page 394: ...23 Instrumentation and Automation 32 200115 II 23 60 W RTSIL 32...