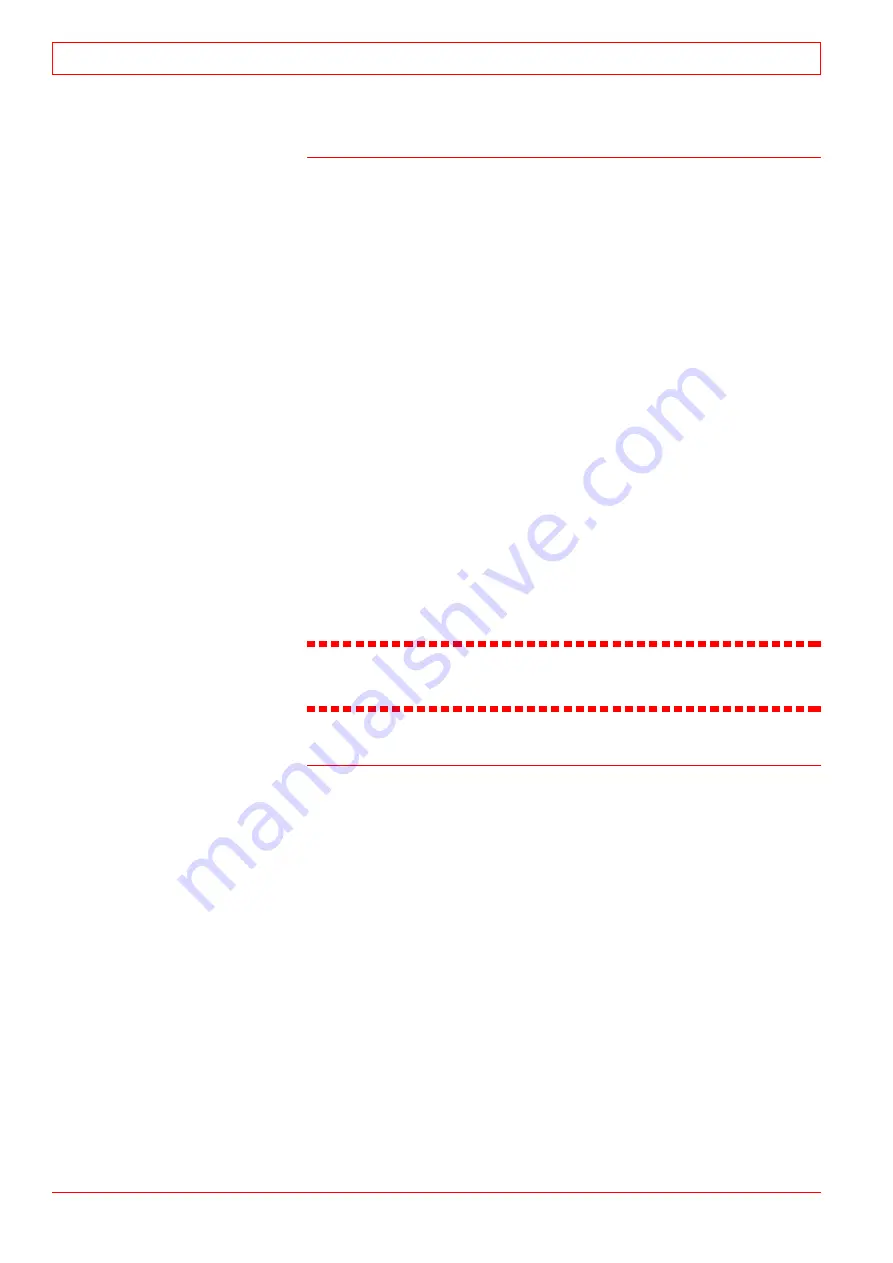
18.5.4 Cleaning of oil side
Fouling of the oil side is normally insignificant. On the other hand,
possible fouling will influence the cooler efficiency very strongly.
Due to the design, the tube stack cannot be cleaned mechani-
cally on the outside. Slight fouling can be removed by blowing
steam through the tube stack.
If the amount of dirt is considerable, use chemical cleaning
solutions available on the market:
Alkaline degreasing agents:
Suitable for normal degreasing, however, not effective for heavy
greases, sludge and oil coke. Requires high temperature. Always
pour degreasing agent slowly into hot water, never the contrary.
Rinse carefully with water after treatment.
Hydrocarbon solvents:
Include the whole range from light petroleum solutions to chlo-
rinated hydrocarbons, e.g. thrichlorethylene. These products
should be handled with care as they are often extremely volatile,
toxic and/or narcotic.
Solvent emulsions:
Heavy fouling, e.g. oil coke, can often be dissolved only by using
these solutions. Several brands are available on the market.
Follow the manufacturer’s instructions to achieve the best
results.
18.5.5 Cleaning of water side
The cleaning should be carried out so that it does not damage the
natural protective layer on the tubes. Use nylon brushes, metallic
brushes can damage the natural protective layer.
Remove loose sludge and deposits with brush 4V84F06. Rinse
with water.
If the deposit in the tubes is hard, e.g. calcium carbonate, it can
be removed chemically by using commercial agents. After this
treatment the tubes should be rinsed and, if necessary, treated
with a solution neutralizing the residual washing agents. Other-
wise, follow the manufacturer’s instructions.
18
Lubricating Oil System
32-200052
18 - 10
WÄRTSILÄ 32
Summary of Contents for VASA 6L32
Page 4: ......
Page 18: ...Appendix B Welding Precautions 200640 00 6...
Page 26: ...01 Main Data Operating Data and General Design 32 200634 01 01 8 W RTSIL 32...
Page 60: ...Appendix A Environmental Hazards 200507 02A 10...
Page 68: ...Page 7 7 Document No 4V92A0645 Rev j...
Page 84: ...03 Start Stop and Operation 32 200402 04 03 12 W RTSIL 32...
Page 98: ...04 Maintenance Schedule 32 200623 01 04 14 W RTSIL 32...
Page 154: ...07 Tightening Torques and Use of Hydraulic Tools 32 200643 01 07 30 W RTSIL 32...
Page 162: ...08 Operating Troubles Emergency Operation 32 200402 01 08 8 W RTSIL 32...
Page 164: ...Specific Installation Data 2005 01 09 2...
Page 178: ...10 Engine Block with Bearings Oil Sump and Cylinder Liner 32 200150 10 14 W RTSIL 32 34SG...
Page 216: ...Appendix A Testing of cylinder tightness 32 200142 A 4 W rtsil 20 32 34...
Page 226: ...13 Camshaft Driving Gear 32 200546 02 13 10 W RTSIL 32...
Page 254: ...15 Turbocharging and Air Cooling 32 200549 10 15 20 W RTSIL 32...
Page 274: ...16 Injection System 32 200627 01 16 20 W RTSIL 32...
Page 280: ...Fuel System 32 200508 07 17 6 W RTSIL 32...
Page 314: ...19 Cooling Water System 32 200050 19 14 W RTSIL 32...
Page 394: ...23 Instrumentation and Automation 32 200115 II 23 60 W RTSIL 32...