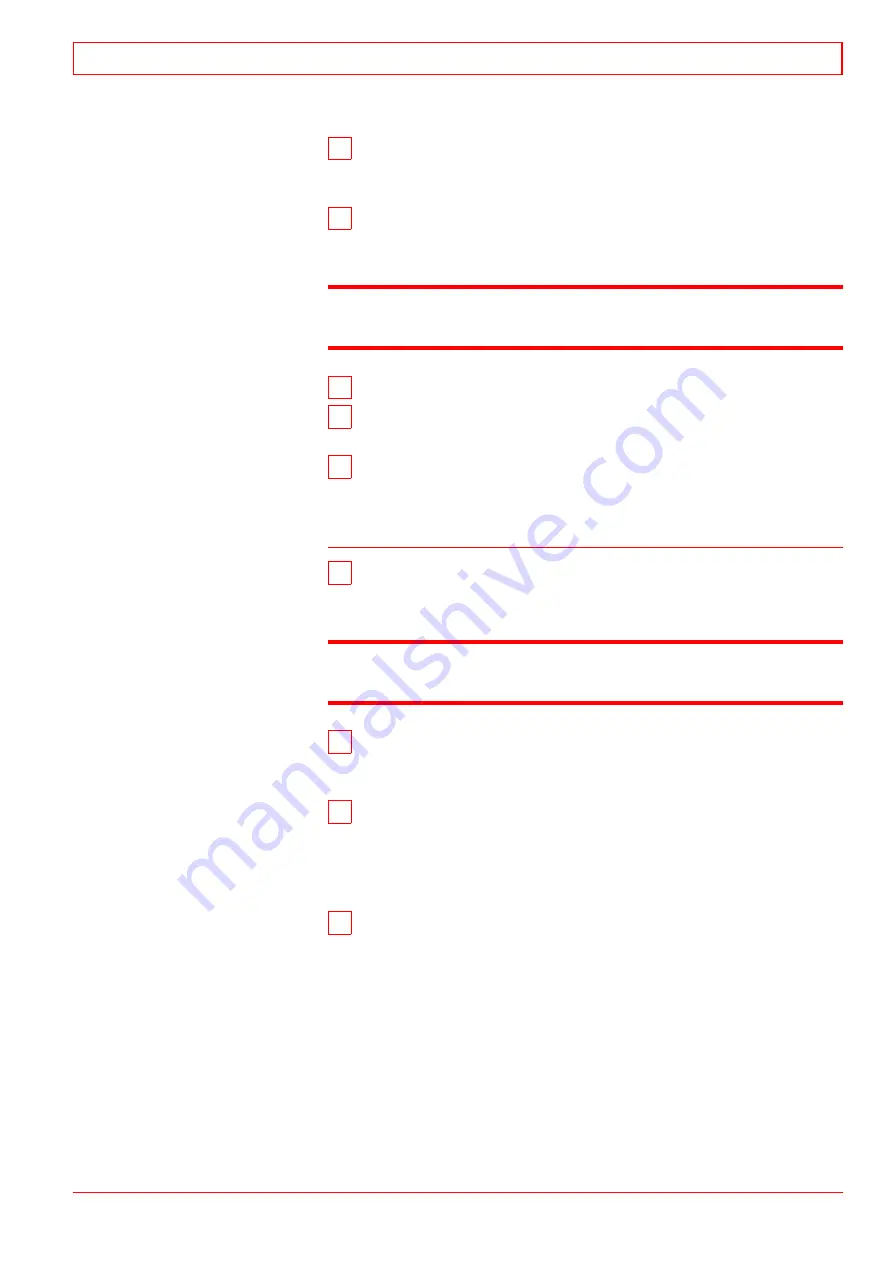
24 Pull lower part of the big end bearing cap out
of the
crankcase, by using the sledge. Take care not to damage the
crank pin. Support the lower half sideways and don’t drop it.
25 Pull the upper part of the big end bearing cap out
of
the crankcase rear side of the engine, by using the sledge.
Support the upper half sideways and don’t drop it.
Note!
Take care not to damage the crank pin or the threads of the
studs.
26 Remove the mounting flute.
27 Cover the crank pin and oil holes
with clean plastic
and tape.
28 For mounting, see section 11.3.5.
11.3.4 Maintenance of piston, rings and connecting
rod bearings
1 Remove the securing ring (7)
from the gudgeon pin hole
in the piston, on the side where the gudgeon pin drawing
number is located, by using the pliers 800002.
Note!
Never compress the securing ring more than necessary to
remove it from the groove.
2 Drive out the gudgeon pin
from the opposite side. In low
temperatures the gudgeon pin may stick but will be easily
removed after heating the piston to about 30°C.
3 If the rings and grooves require cleaning, measuring
etc.,
remove the piston rings by using the pliers 320D12/6-S7/8.
Before removing, note the positions of the rings to ensure mounting
in the same grooves. The design of the pliers prevents overstressing
of the rings. Using other means may overstress the rings.
4 Clean all the parts carefully.
Remove the piston rings,
and remove burned carbon deposits from the piston and piston
ring grooves e.g. by using an old piston ring. Special care
should be taken not to damage the piston material. Never use
emery cloth on the piston skirt.
The cleaning is facilitated if coked parts are soaked in kero-
sene or fuel oil. An efficient carbon solvent — e.g. ARDROX
No. 668 or similar — should preferably be used to facilitate
cleaning of the piston crown. When using chemical cleaning
agents, take care not to clean piston skirt with such agents
because the phosphate/graphite overlay may be damaged.
32-200020
Crank Mechanism: Crankshaft, Connecting Rod, Piston
11
WÄRTSILÄ 32
11 - 9
Summary of Contents for VASA 6L32
Page 4: ......
Page 18: ...Appendix B Welding Precautions 200640 00 6...
Page 26: ...01 Main Data Operating Data and General Design 32 200634 01 01 8 W RTSIL 32...
Page 60: ...Appendix A Environmental Hazards 200507 02A 10...
Page 68: ...Page 7 7 Document No 4V92A0645 Rev j...
Page 84: ...03 Start Stop and Operation 32 200402 04 03 12 W RTSIL 32...
Page 98: ...04 Maintenance Schedule 32 200623 01 04 14 W RTSIL 32...
Page 154: ...07 Tightening Torques and Use of Hydraulic Tools 32 200643 01 07 30 W RTSIL 32...
Page 162: ...08 Operating Troubles Emergency Operation 32 200402 01 08 8 W RTSIL 32...
Page 164: ...Specific Installation Data 2005 01 09 2...
Page 178: ...10 Engine Block with Bearings Oil Sump and Cylinder Liner 32 200150 10 14 W RTSIL 32 34SG...
Page 216: ...Appendix A Testing of cylinder tightness 32 200142 A 4 W rtsil 20 32 34...
Page 226: ...13 Camshaft Driving Gear 32 200546 02 13 10 W RTSIL 32...
Page 254: ...15 Turbocharging and Air Cooling 32 200549 10 15 20 W RTSIL 32...
Page 274: ...16 Injection System 32 200627 01 16 20 W RTSIL 32...
Page 280: ...Fuel System 32 200508 07 17 6 W RTSIL 32...
Page 314: ...19 Cooling Water System 32 200050 19 14 W RTSIL 32...
Page 394: ...23 Instrumentation and Automation 32 200115 II 23 60 W RTSIL 32...