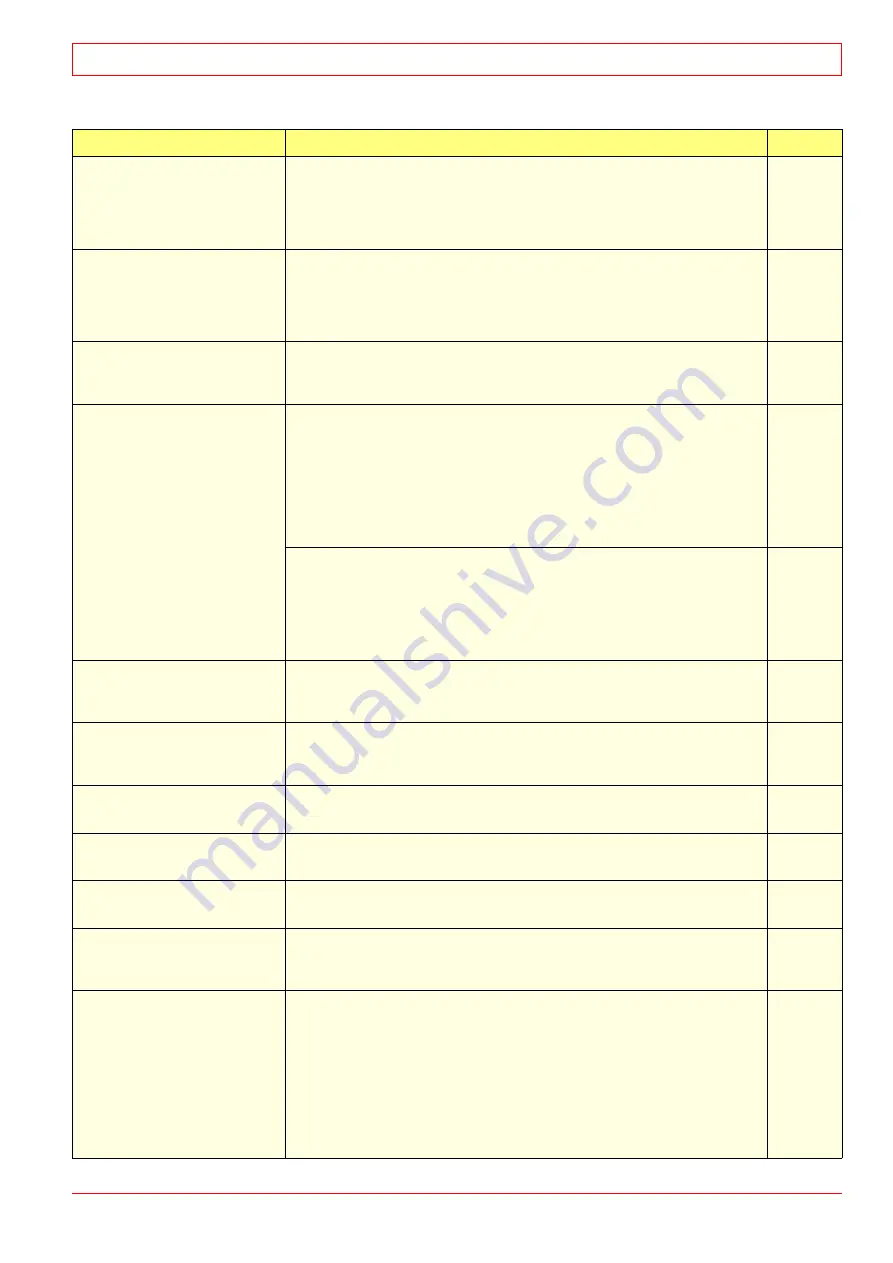
04.9
Interval: 4000 operating hours
Air cooler(s)
Clean charge air cooler(s)
15.5
Clean and pressure test. Look carefully for corrosion. Check for
possible leakage. Replace parts if necessary.
Check accurate pressure difference over the charge air cooler
(air side) by using u-tube.
Automation
Check connectors and cables
23.8
Check mounting and connections. Apply contact lubricant to
contact surfaces. Check tightness of connections. Check condition
of cables, wires and cable glands. Replace damaged connectors
and cables.
Camshaft
Inspect contact faces of camshaft
14.1.3
Check the contact faces of the cams and tappet rollers. Check that the
rollers rotate. Rotate the engine with the turning gear.
03.1
Cooling water spaces
Inspect HT-water spaces on engine with cooled
turbocharger
15.2
Inspect turbocharger cooling water ducts for possible deposits.
Clean if the deposits are 1mm or thicker.
Remove air venting pipe and adapter plug on the multiduct, inspect
the water side of one duct . If the deposits are thicker than 1 mm, clean
all liners and engine block water space. Improve the cooling water
treatment.
19.2
19.1.2
02.3
10.5
Inspect HT-water spaces on engine with uncooled
turbocharger
15.2
Remove air venting pipe and adapter plug on the multiduct, inspect
the water side of one duct . If the deposits are thicker than 1 mm, clean
all liners and engine block water space. Improve the cooling water
treatment.
19.2
19.1.2
02.3
10.5
Control mechanism
Check control mechanism
22.2
Check for wear in all connecting links between the governor and all
injection pumps.
Crankshaft
Check crankshaft alignment
11.2.2
Check alignment, use form WV98V036. Alignment check is
performed on a warm engine.
Crankshaft
Check thrust bearing clearance
11.2.3
Check axial clearance
06.2
Exhaust manifold
Check for leaks
20.
Check for leaks once a year. Replace parts if necessary.
Flexible coupling
Oil change of the coupling
Geislinger (Oil filled)
Change oil of the coupling. See manufacturers instructions.
Fuel system
Check and adjust fuel system
17.
Check the adjustment of fuel system. Check for possible leakage.
Replace parts if necessary.
Injection valves
Inspect injection valves
16.4.4
Test the opening pressure. Dismantle and clean nozzles. Check the
effective needle lift. Check the springs.
Check and change the push rod if necessary. Replace the O-rings.
Check the nozzle condition in a test pump.
HFO: Recommendation:
Replace the nozzle by new ones on
6000h at the latest.
DO (LFO): Recommendation:
Replace the nozzle by new ones on
8000h at the latest.
Continue
32-200623-01
Maintenance Schedule
04
WÄRTSILÄ 32
04 - 7
Summary of Contents for VASA 6L32
Page 4: ......
Page 18: ...Appendix B Welding Precautions 200640 00 6...
Page 26: ...01 Main Data Operating Data and General Design 32 200634 01 01 8 W RTSIL 32...
Page 60: ...Appendix A Environmental Hazards 200507 02A 10...
Page 68: ...Page 7 7 Document No 4V92A0645 Rev j...
Page 84: ...03 Start Stop and Operation 32 200402 04 03 12 W RTSIL 32...
Page 98: ...04 Maintenance Schedule 32 200623 01 04 14 W RTSIL 32...
Page 154: ...07 Tightening Torques and Use of Hydraulic Tools 32 200643 01 07 30 W RTSIL 32...
Page 162: ...08 Operating Troubles Emergency Operation 32 200402 01 08 8 W RTSIL 32...
Page 164: ...Specific Installation Data 2005 01 09 2...
Page 178: ...10 Engine Block with Bearings Oil Sump and Cylinder Liner 32 200150 10 14 W RTSIL 32 34SG...
Page 216: ...Appendix A Testing of cylinder tightness 32 200142 A 4 W rtsil 20 32 34...
Page 226: ...13 Camshaft Driving Gear 32 200546 02 13 10 W RTSIL 32...
Page 254: ...15 Turbocharging and Air Cooling 32 200549 10 15 20 W RTSIL 32...
Page 274: ...16 Injection System 32 200627 01 16 20 W RTSIL 32...
Page 280: ...Fuel System 32 200508 07 17 6 W RTSIL 32...
Page 314: ...19 Cooling Water System 32 200050 19 14 W RTSIL 32...
Page 394: ...23 Instrumentation and Automation 32 200115 II 23 60 W RTSIL 32...