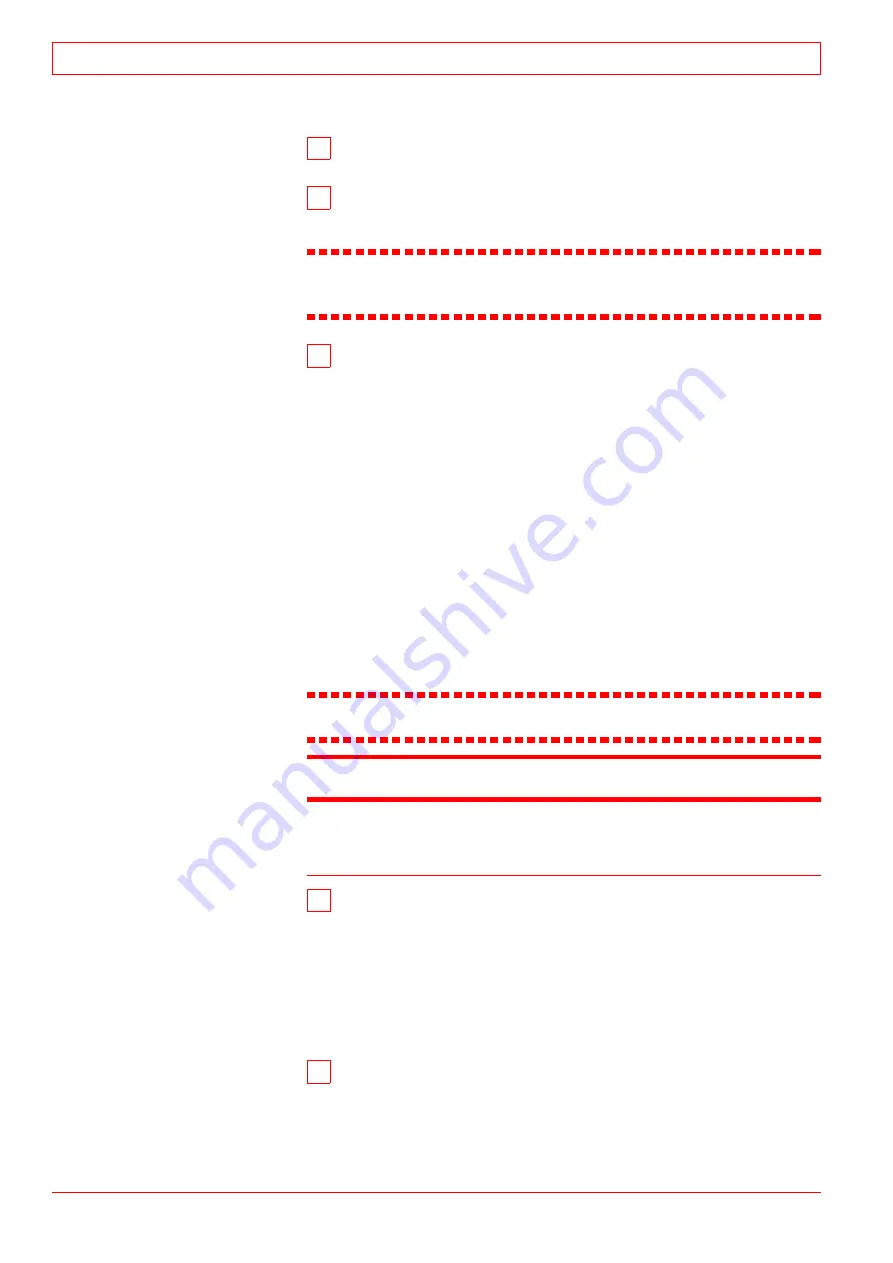
5 Measure the height
of the piston ring grooves, e.g. with
an inside micrometer.
6 Inspect anti-polishing ring.
Turn ring upside down after
first period. Change the ring every second period.
When mounting a new cylinder liner, or honing the old liner, all
rings are to be replaced by new ones, acc. to chapter 04.
7 Check the gudgeon pin and big end bearing clear-
ances
by measuring the pin diameters and assembled bear-
ing bores separately. When measuring the big end bearing bore
all the connecting rod screws (upper and lower) must be tight-
ened to the stated pressure.
a) Big end bearings of trimetal type
can be used until the overlay
is worn through. When the underlaying nickel barrier of the lining
material is exposed the bearing must be replaced.
b) Wear of bimetal bearing shells
can be settled by measuring
thickness. For this purpose a ball anvil micrometer should be
used.
For bimetal-type bearing, the wear limits given in chapter 06.2
must be applied.
When replacing a big end bearing both the upper and the lower
bearing shell must be renewed.
Only bearings of same type to be used as a pair.
Mark new bearings with the bearing number.
Note!
It is very important that the bearing shells are mounted straight.
11.3.5 Assembling and mounting of piston and
connecting rod
1 Lubricate the gudgeon pin,
and mount it from the same
side from where it was removed, with the end marked with the
drawing number in the same direction. The cylinder number
is stamped on the piston crown and connecting rod, Fig 11-3.
When changing the piston, mark the new piston with the same
cylinder number in the same place as on the replaced one.
At low temperatures, the gudgeon pin may stick but will be
easily fitted after heating the piston to about 30°C, e.g. in oil.
2 Mount the securing ring (7).
11
Crank Mechanism: Crankshaft, Connecting Rod, Piston
32-200020
11 - 10
WÄRTSILÄ 32
Summary of Contents for VASA 6L32
Page 4: ......
Page 18: ...Appendix B Welding Precautions 200640 00 6...
Page 26: ...01 Main Data Operating Data and General Design 32 200634 01 01 8 W RTSIL 32...
Page 60: ...Appendix A Environmental Hazards 200507 02A 10...
Page 68: ...Page 7 7 Document No 4V92A0645 Rev j...
Page 84: ...03 Start Stop and Operation 32 200402 04 03 12 W RTSIL 32...
Page 98: ...04 Maintenance Schedule 32 200623 01 04 14 W RTSIL 32...
Page 154: ...07 Tightening Torques and Use of Hydraulic Tools 32 200643 01 07 30 W RTSIL 32...
Page 162: ...08 Operating Troubles Emergency Operation 32 200402 01 08 8 W RTSIL 32...
Page 164: ...Specific Installation Data 2005 01 09 2...
Page 178: ...10 Engine Block with Bearings Oil Sump and Cylinder Liner 32 200150 10 14 W RTSIL 32 34SG...
Page 216: ...Appendix A Testing of cylinder tightness 32 200142 A 4 W rtsil 20 32 34...
Page 226: ...13 Camshaft Driving Gear 32 200546 02 13 10 W RTSIL 32...
Page 254: ...15 Turbocharging and Air Cooling 32 200549 10 15 20 W RTSIL 32...
Page 274: ...16 Injection System 32 200627 01 16 20 W RTSIL 32...
Page 280: ...Fuel System 32 200508 07 17 6 W RTSIL 32...
Page 314: ...19 Cooling Water System 32 200050 19 14 W RTSIL 32...
Page 394: ...23 Instrumentation and Automation 32 200115 II 23 60 W RTSIL 32...