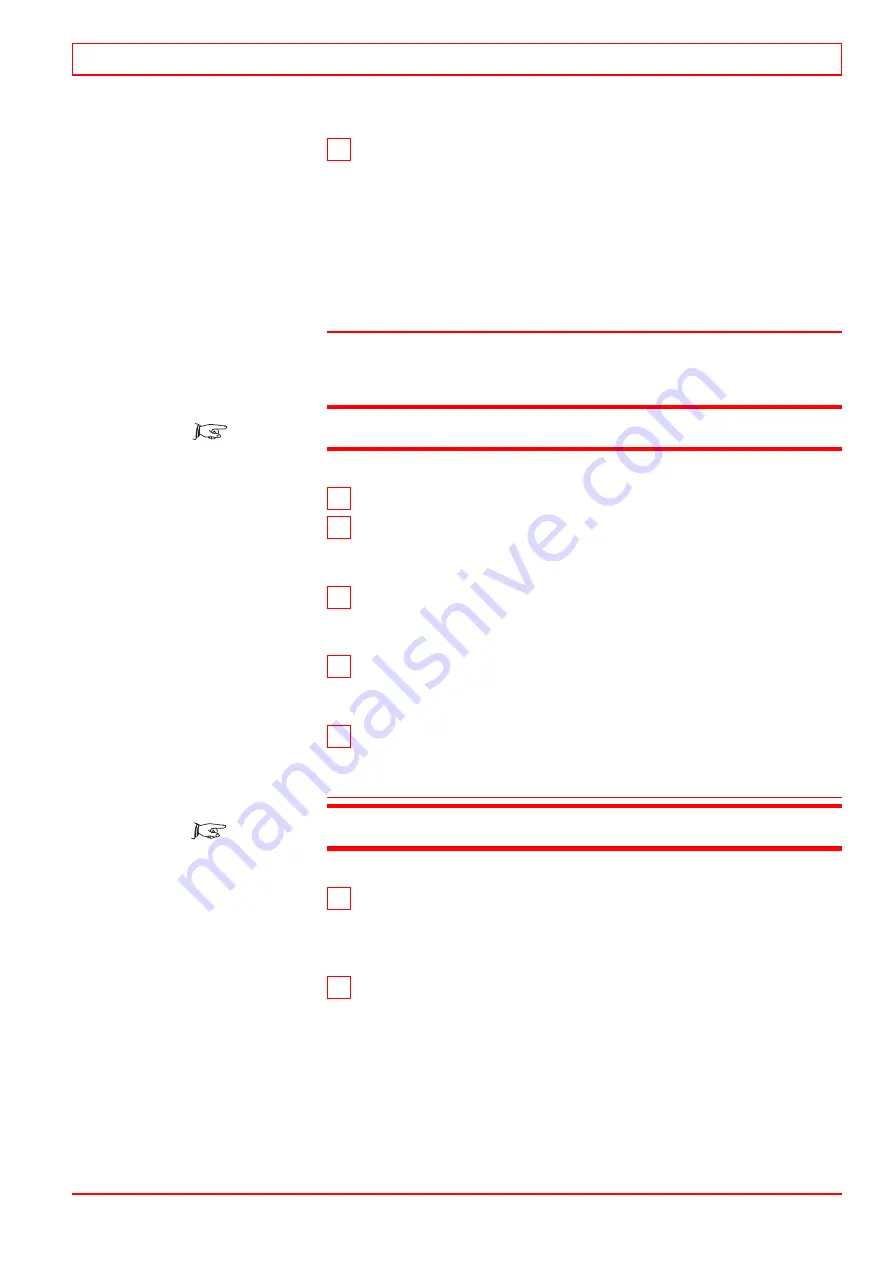
5 Before grinding, check the valve stem clearance.
If
the clearance is too large, measure the stem and guide, and
change the worn part; the valve guide can be pressed out.
Check the bore in the cylinder head. When refitting, cooling in
with liquid nitrogen is recommended, but pressing in with oil
lubrication can also be accepted. After fitting in, check the
guide bore and calibrate, if necessary.
12.3.4 Lapping of inlet valves
If there are slight pits on the sealing faces they can be lapped by
hand:
Note!
Lapping is not allowed for exhaust valves.
1 Fit the turning tool
to the valve.
2 Apply a thin layer of lapping compound
to the sealing
surface of the valve; No.1 for coarse lapping, No.3 for fine
lapping.
3 Rotate the valve to and fro
towards the seat with the
turning tool 800028. Lift the valve from the seat at intervals
while lapping.
4 Remove the smallest possible amount of material
because the sealing faces have hardened during operation and
are valuable. It is not necessary to grind off all pits.
5 Clean the valve and seat
carefully after lapping.
12.3.5 Machine grinding of exhaust and inlet valves
Note!
The valve should be cooled by water during the grinding.
1 Seat face of the inlet valve:
The seat angle of the inlet
valve is 20° with a tolerance of 0°- +0.10°. Minimum allowable
inner diameter “X” of the seat face after grinding is 85 mm, see
Fig 12-6; after that, the valve must be replaced by a new one.
2 Seat face of the exhaust valve:
The seat angle of the ex-
haust valve is 40° with a tolerance of 0.10°- +0.20° to achieve
contact to the seat ring at the periphery of the valve. Minimum
allowable inner diameter “X” of the seat face after grinding is
82 mm, see Fig 12-6; after that, the valve must be replaced by a
new one.
32-200646-01
Cylinder Head with Valves
12
WÄRTSILÄ 32
12 - 9
Summary of Contents for PAAE051728
Page 4: ......
Page 18: ...Appendix B Welding Precautions 200640 00 6...
Page 26: ...01 Main Data Operating Data and General Design 32 200634 01 01 8 W RTSIL 32...
Page 60: ...Appendix A Environmental Hazards 200507 02A 10...
Page 68: ...Page 7 7 Document No 4V92A0645 Rev j...
Page 84: ...03 Start Stop and Operation 32 200402 04 03 12 W RTSIL 32...
Page 98: ...04 Maintenance Schedule 32 200623 01 04 14 W RTSIL 32...
Page 154: ...07 Tightening Torques and Use of Hydraulic Tools 32 200643 01 07 30 W RTSIL 32...
Page 162: ...08 Operating Troubles Emergency Operation 32 200402 01 08 8 W RTSIL 32...
Page 164: ...Specific Installation Data 2005 01 09 2...
Page 178: ...10 Engine Block with Bearings Oil Sump and Cylinder Liner 32 200150 10 14 W RTSIL 32 34SG...
Page 216: ...Appendix A Testing of cylinder tightness 32 200142 A 4 W rtsil 20 32 34...
Page 226: ...13 Camshaft Driving Gear 32 200546 02 13 10 W RTSIL 32...
Page 254: ...15 Turbocharging and Air Cooling 32 200549 10 15 20 W RTSIL 32...
Page 274: ...16 Injection System 32 200627 01 16 20 W RTSIL 32...
Page 280: ...Fuel System 32 200508 07 17 6 W RTSIL 32...
Page 314: ...19 Cooling Water System 32 200050 19 14 W RTSIL 32...
Page 394: ...23 Instrumentation and Automation 32 200115 II 23 60 W RTSIL 32...