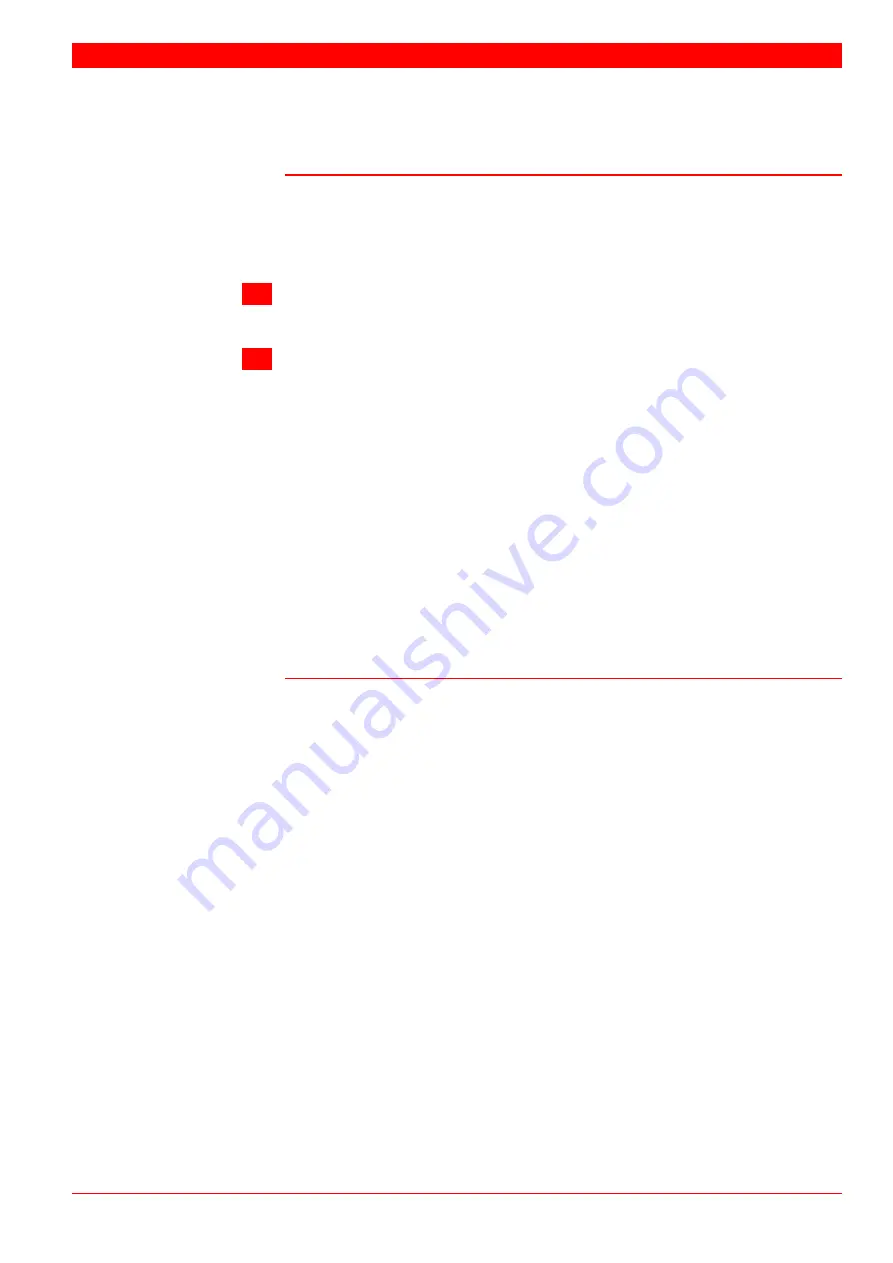
02.1.5 Measures to avoid difficulties when running on
heavy fuel
Poor fuel quality will influence on wear, engine part lifetime and
maintenance intervals adversely.
In order to obtain maximum operating economy it is recommend-
able:
a)
to limit maximum continuous output
as much as operating condi-
tions allow if fuel is known or suspected to have high vanadium
content (above 200 ppm) and sodium content.
b)
to limit low load operation
as much as operating conditions al-
low if fuel is known or suspected to have high sulphur content
(above 3 mass-%), carbon content (Conradson carbon above
12 mass-%) and/or asphaltene content (above 8 mass-%).
Operating below 20% of rated output should be limited to max. 100
hours continuously, by loading the engine above 70% of rated load for
one hour before continuing the low load operation or shutting down
the engine.
Idling (i.e. main engine declutched, generator set disconnected)
should be limited as much as possible. Warming-up of the engine
at no load for more than 3 - 5 minutes before loading, as well as
idling for more than 3 minutes before stopping is unnecessary and
should be avoided.
02.1.6 General advice
To avoid stability and incompatibility problems (precipitation of
heavy components in the fuel), avoid, if possible, blending of fuels
from different bunker stations, unless the fuels are known to be
compatible.
If stability and compatibility problems occur, never add distillate
fuel, as this will probably increase precipitation. A fuel additive with
a highly powerful dispersing characteristics can be of help until a
new fuel delivery takes place.
The characteristics of heavy fuels blended from residuals from
modern refinery processes like catalytic cracking and visbreaking
may approach at least some of the limits of fuel characteristics given
in the chapter 02., sect. 02.1.3.
Compared with “traditional” heavy fuels blended from straight
run residuals, the “modern” heavy fuels may have reduced ignition
and combustion quality.
Fuels blended from catalytic cracking residuals may contain very
abrasive catalytic fines (silicon and aluminium oxides) which, if
allowed to enter the injection system, may wear down injection
pumps and nozzles in a few hours.
Some of the difficulties that may occur when operating on heavy
fuels blended from cracked residuals can be avoided by:
·
Sufficient centrifuging capacity. The best and most distur-
bance-free results are obtained with the purifier and clarifier
200549-01
Fuel, Lubricating Oil, Cooling Water
W20/W32/W46, W46F, 32, 32LN
02 - 11
Summary of Contents for PAAE051728
Page 4: ......
Page 18: ...Appendix B Welding Precautions 200640 00 6...
Page 26: ...01 Main Data Operating Data and General Design 32 200634 01 01 8 W RTSIL 32...
Page 60: ...Appendix A Environmental Hazards 200507 02A 10...
Page 68: ...Page 7 7 Document No 4V92A0645 Rev j...
Page 84: ...03 Start Stop and Operation 32 200402 04 03 12 W RTSIL 32...
Page 98: ...04 Maintenance Schedule 32 200623 01 04 14 W RTSIL 32...
Page 154: ...07 Tightening Torques and Use of Hydraulic Tools 32 200643 01 07 30 W RTSIL 32...
Page 162: ...08 Operating Troubles Emergency Operation 32 200402 01 08 8 W RTSIL 32...
Page 164: ...Specific Installation Data 2005 01 09 2...
Page 178: ...10 Engine Block with Bearings Oil Sump and Cylinder Liner 32 200150 10 14 W RTSIL 32 34SG...
Page 216: ...Appendix A Testing of cylinder tightness 32 200142 A 4 W rtsil 20 32 34...
Page 226: ...13 Camshaft Driving Gear 32 200546 02 13 10 W RTSIL 32...
Page 254: ...15 Turbocharging and Air Cooling 32 200549 10 15 20 W RTSIL 32...
Page 274: ...16 Injection System 32 200627 01 16 20 W RTSIL 32...
Page 280: ...Fuel System 32 200508 07 17 6 W RTSIL 32...
Page 314: ...19 Cooling Water System 32 200050 19 14 W RTSIL 32...
Page 394: ...23 Instrumentation and Automation 32 200115 II 23 60 W RTSIL 32...