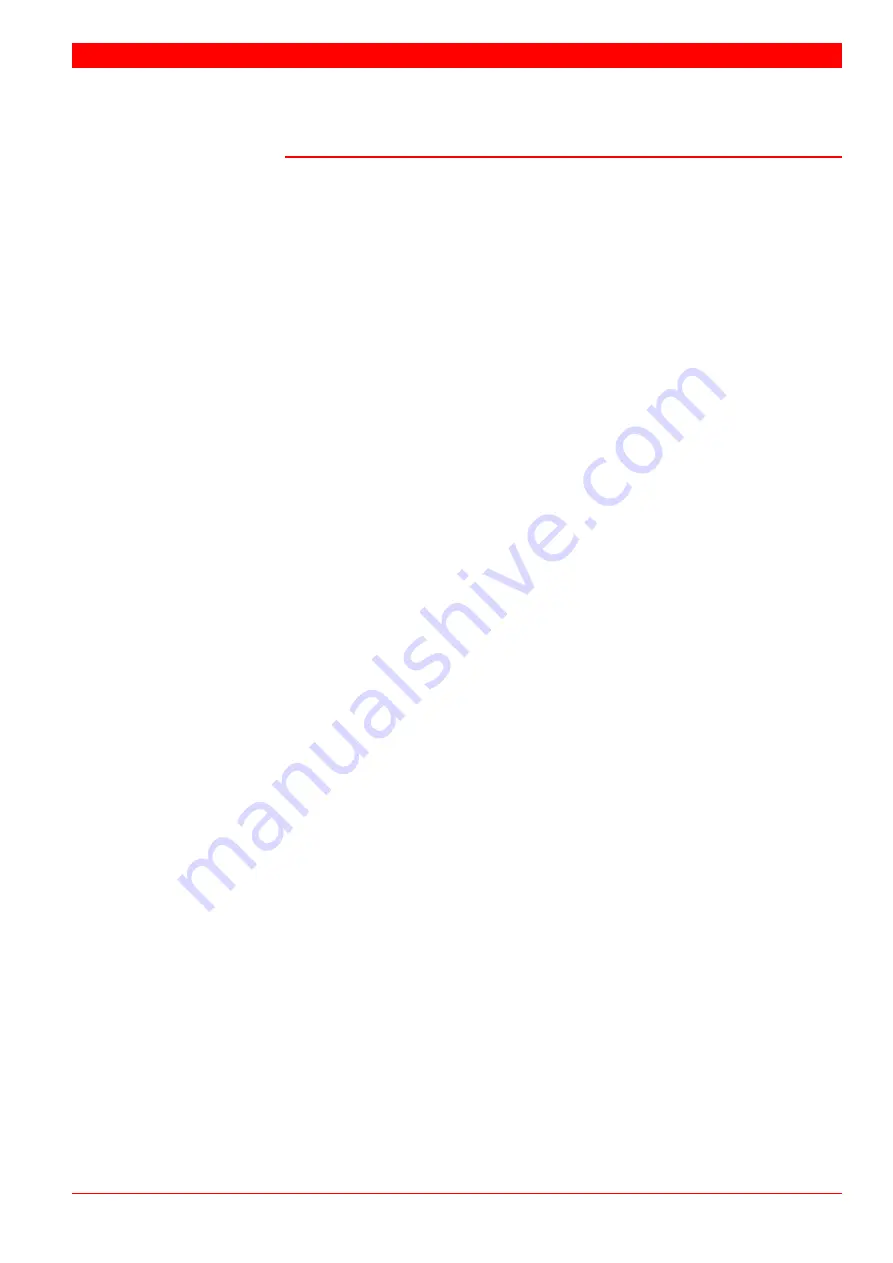
00B.1.2 Main principles:
·
Prevent uncontrolled current loops
·
Prevent radiation
·
Prevent sparkles flying around
·
If convenient, disconnect all global signals like power supply, data
communication etc.
00B.1.2.1
Preventing uncontrolled current loops
Welding current path must always be checked, there should be a
straight route from the welding point back to the return connection
of the welding apparatus.
The main current is always going where it meets the lowest resis-
tance, in certain cases the return current can therefore go via
grounding wires and electronics in the control system.
To avoid this, the distance between the welding point and the return
connection clamp of the welding apparatus should always be
shortest possible and without electronic components in the return-
ing loop path.
Attention must be paid to the connectivity of the return connection
clamp, a bad contact might also cause sparkles and radiation.
00B.1.2.2
Preventing Radiation
The welding current and the arc is emitting a wide spectrum of
electromagnetic radiation. This might cause damages on sensitive
electronic equipment.
To avoid these damages all cabinets and terminal boxes must be
kept closed during the welding. Sensitive equipment can also be
protected by means of shielding with a conductive metal plate.
Also avoid having the cables of the welding apparatus going in
parallel with wires and cables in the control system. The high welding
current is easily inducting secondary currents in other conductive
materials.
00B.1.2.3
Preventing damage due to sparkles
Welding produces sparks. Few materials withstand the heat from
these sparkles. Therefore all cabinets and terminal boxes should be
kept closed during the welding. Sensors, actuators, cables and
other equipment on the engine must be properly protected.
Sparkles can also be a problem after they have cooled down, i.e.
causing short circuits, sealing problems etc.
200640
Welding Precautions
Appendix B
00 - 3
Summary of Contents for PAAE051728
Page 4: ......
Page 18: ...Appendix B Welding Precautions 200640 00 6...
Page 26: ...01 Main Data Operating Data and General Design 32 200634 01 01 8 W RTSIL 32...
Page 60: ...Appendix A Environmental Hazards 200507 02A 10...
Page 68: ...Page 7 7 Document No 4V92A0645 Rev j...
Page 84: ...03 Start Stop and Operation 32 200402 04 03 12 W RTSIL 32...
Page 98: ...04 Maintenance Schedule 32 200623 01 04 14 W RTSIL 32...
Page 154: ...07 Tightening Torques and Use of Hydraulic Tools 32 200643 01 07 30 W RTSIL 32...
Page 162: ...08 Operating Troubles Emergency Operation 32 200402 01 08 8 W RTSIL 32...
Page 164: ...Specific Installation Data 2005 01 09 2...
Page 178: ...10 Engine Block with Bearings Oil Sump and Cylinder Liner 32 200150 10 14 W RTSIL 32 34SG...
Page 216: ...Appendix A Testing of cylinder tightness 32 200142 A 4 W rtsil 20 32 34...
Page 226: ...13 Camshaft Driving Gear 32 200546 02 13 10 W RTSIL 32...
Page 254: ...15 Turbocharging and Air Cooling 32 200549 10 15 20 W RTSIL 32...
Page 274: ...16 Injection System 32 200627 01 16 20 W RTSIL 32...
Page 280: ...Fuel System 32 200508 07 17 6 W RTSIL 32...
Page 314: ...19 Cooling Water System 32 200050 19 14 W RTSIL 32...
Page 394: ...23 Instrumentation and Automation 32 200115 II 23 60 W RTSIL 32...