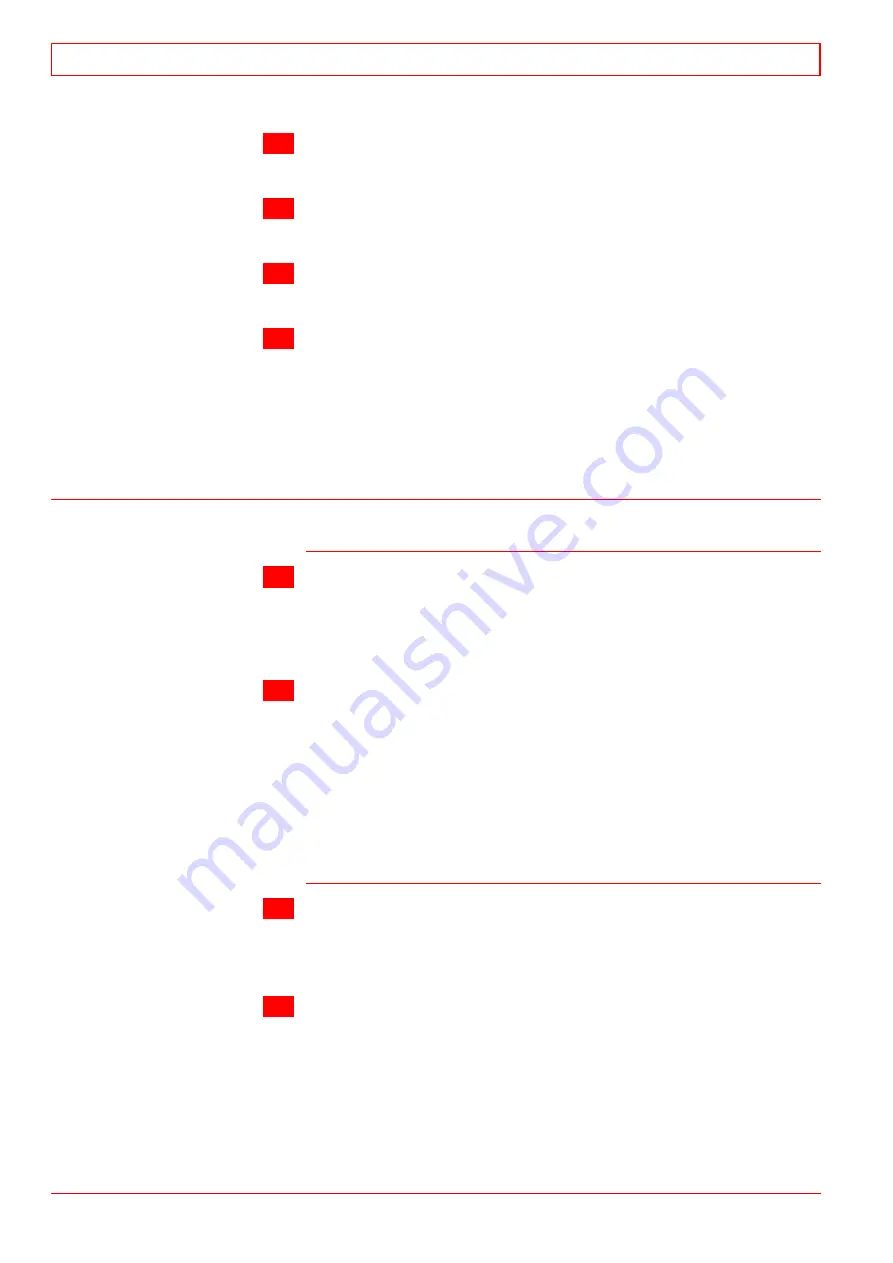
a)
The system should work with minimal friction.
Regularly clean
and lubricate racks, bearings (also self-lubricating bearings
(8)) and ball joints with lubricating oil.
b)
The system should be as free from clearances
as possible.
Check clearances of all connections. Total clearance may cor-
respond to max. 0.5 mm of injection pump fuel rack positions.
c)
Check regularly
(see recommendations in chapter 04.) the
adjustment of the system; stop position, overspeed trip devices
and starting fuel limiter, see section 22.3.
d)
When reassembling the system,
check that all details are
placed in the right position, that all nuts are properly tightened
and to torque, if so prescribed, and that all locking elements
like pins, retainer rings, locking plates are in their positions.
Check according to pos. a) - c).
22.3
Check and adjustment
22.3.1 Stop lever stop position
a)
Check:
·
Set the terminal shaft lever (3) in the maximum fuel position
and the stop lever (16) in the stop position.
·
Check that the fuel rack position of all injection pumps is
maximum 5 mm.
b)
Adjustment:
·
Set the stop lever in the stop position and check that the
lever (9) contacts the dog (18) properly. A small torque can
be set from the governor, but not a too large one, because this
will twist the shaft unnecessarily, although little.
·
Adjust the fuel rack position to 5 mm by adjusting the screws
(14).
22.3.2 Governor stop position
a)
Check:
·
Move stop lever into work position.
·
Set the governor terminal shaft lever in the stop position.
·
Check that the fuel rack positions are 2 mm.
b)
Adjustment:
·
If the fuel rack positions are unequal, adjust first according
to section 22.3.1b).
·
Adjust the link rod so that the fuel rack position of 2 mm is
obtained.
·
If changing the governor, see section 22.4.
22
Control Mechanism
32-200636-01
22 - 2
WÄRTSILÄ 32
Summary of Contents for PAAE051728
Page 4: ......
Page 18: ...Appendix B Welding Precautions 200640 00 6...
Page 26: ...01 Main Data Operating Data and General Design 32 200634 01 01 8 W RTSIL 32...
Page 60: ...Appendix A Environmental Hazards 200507 02A 10...
Page 68: ...Page 7 7 Document No 4V92A0645 Rev j...
Page 84: ...03 Start Stop and Operation 32 200402 04 03 12 W RTSIL 32...
Page 98: ...04 Maintenance Schedule 32 200623 01 04 14 W RTSIL 32...
Page 154: ...07 Tightening Torques and Use of Hydraulic Tools 32 200643 01 07 30 W RTSIL 32...
Page 162: ...08 Operating Troubles Emergency Operation 32 200402 01 08 8 W RTSIL 32...
Page 164: ...Specific Installation Data 2005 01 09 2...
Page 178: ...10 Engine Block with Bearings Oil Sump and Cylinder Liner 32 200150 10 14 W RTSIL 32 34SG...
Page 216: ...Appendix A Testing of cylinder tightness 32 200142 A 4 W rtsil 20 32 34...
Page 226: ...13 Camshaft Driving Gear 32 200546 02 13 10 W RTSIL 32...
Page 254: ...15 Turbocharging and Air Cooling 32 200549 10 15 20 W RTSIL 32...
Page 274: ...16 Injection System 32 200627 01 16 20 W RTSIL 32...
Page 280: ...Fuel System 32 200508 07 17 6 W RTSIL 32...
Page 314: ...19 Cooling Water System 32 200050 19 14 W RTSIL 32...
Page 394: ...23 Instrumentation and Automation 32 200115 II 23 60 W RTSIL 32...