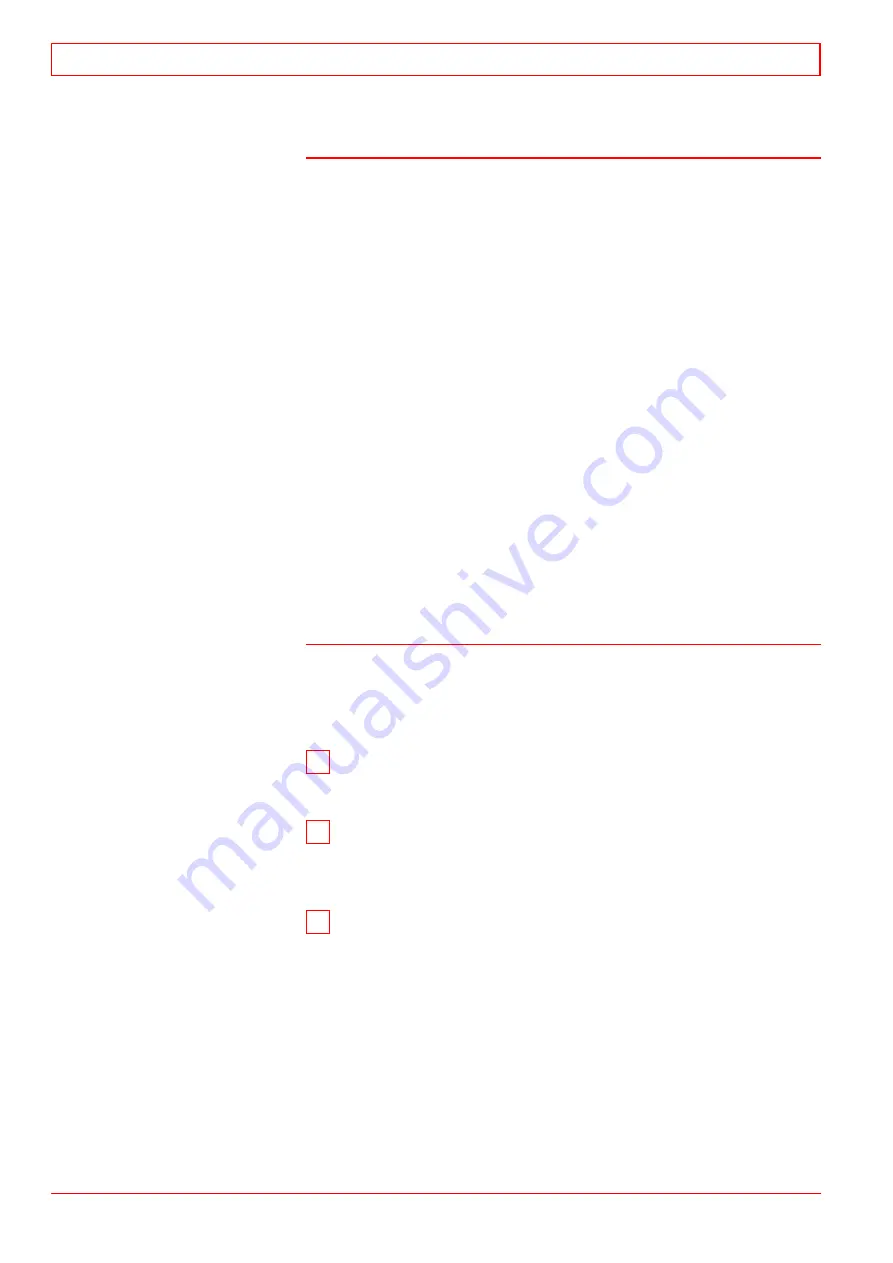
16.4.4 Testing of nozzle function in general
·
If abnormal running parameters are observed (abnormally
high or low exh. gas temperatures, low firing pressure) one
reason can be leaking or blocked fuel injector(s).
·
The nozzle holes can be checked with the hand test pump by
giving a quick and heavy blow and using a paper under the
nozzle tip,
but keep your hands away
. All sprays should give
an equal impression on paper; the number of impressions
should correspond to the hole configuration (10 holes). An
irregular form tells that the hole is partly blocked and should
be cleaned.
·
Testing of nozzle atomization with the hand test pump
however is not completely reliable. When using hand test
pump, the injected fuel amount is very small. Therefore, the
needle stroke is very short and may give an impression of
bad atomization.
A nozzle that gives bad atomization on the test pump can give
good performance on an engine.
Fot tests of the nozzle function with fully amount of fuel injected,
a special booster unit is developed and can be ordered as an
optional tool.
16.4.5 Function of the booster unit
The aim with the booster unit after the hand test pump is to
provide waving fuel pressure with a right quantity to the nozzle.
The booster unit is operating as follows:
1 Fuel is supplied
from the hand test pump device through
the port (1) to the chamber (2). see Fig 16-6.The first filling of
the booster requires about 80 strokes.
2 If the booster unit
has not been used, the trapped air is
pumped out (requires 5-8 strokes) through the lower valve (3)
to the leak channel. Close the valve (3) after venting the booster
unit.
3 The right pressure wave level
is reached by pumping
prepressure to the high pressure line to fuel injector. This is
done by opening the valve (4) and pumping with the test pump
the pressure little over 200 bar. After this the valve (4) should
be closed.
16
Injection System
32-200627-01
16 - 16
WÄRTSILÄ 32
Summary of Contents for PAAE051728
Page 4: ......
Page 18: ...Appendix B Welding Precautions 200640 00 6...
Page 26: ...01 Main Data Operating Data and General Design 32 200634 01 01 8 W RTSIL 32...
Page 60: ...Appendix A Environmental Hazards 200507 02A 10...
Page 68: ...Page 7 7 Document No 4V92A0645 Rev j...
Page 84: ...03 Start Stop and Operation 32 200402 04 03 12 W RTSIL 32...
Page 98: ...04 Maintenance Schedule 32 200623 01 04 14 W RTSIL 32...
Page 154: ...07 Tightening Torques and Use of Hydraulic Tools 32 200643 01 07 30 W RTSIL 32...
Page 162: ...08 Operating Troubles Emergency Operation 32 200402 01 08 8 W RTSIL 32...
Page 164: ...Specific Installation Data 2005 01 09 2...
Page 178: ...10 Engine Block with Bearings Oil Sump and Cylinder Liner 32 200150 10 14 W RTSIL 32 34SG...
Page 216: ...Appendix A Testing of cylinder tightness 32 200142 A 4 W rtsil 20 32 34...
Page 226: ...13 Camshaft Driving Gear 32 200546 02 13 10 W RTSIL 32...
Page 254: ...15 Turbocharging and Air Cooling 32 200549 10 15 20 W RTSIL 32...
Page 274: ...16 Injection System 32 200627 01 16 20 W RTSIL 32...
Page 280: ...Fuel System 32 200508 07 17 6 W RTSIL 32...
Page 314: ...19 Cooling Water System 32 200050 19 14 W RTSIL 32...
Page 394: ...23 Instrumentation and Automation 32 200115 II 23 60 W RTSIL 32...