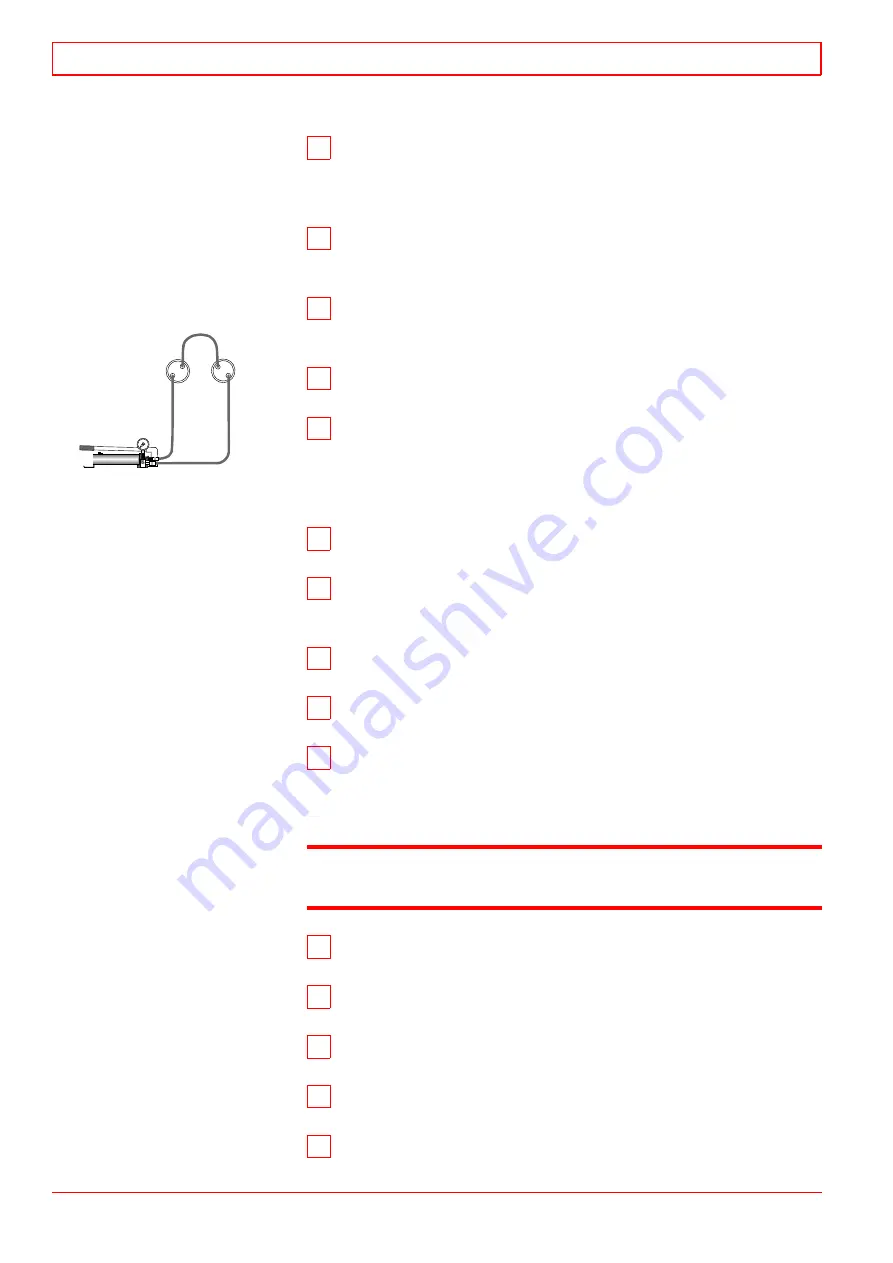
8 Remove the quick coupling from the return hose
and
reverse the oil feed to the hydraulic jack. Mount the quick
coupling male part to the free end of the hose and place it in
the crankcase.
9 Lift the main bearing cap
by pumping oil to the hydrau-
lic jack with the hydraulic pump. Mount the main bearing nuts
by hand. Remove the hoses from the hydraulic jack.
10 Mount the side screws
into the main bearing cap. Lubri-
cate those threads of the screw that enters the bearing cap.
Note! Replace the O-rings on the side screws.
11 Tighten the side screws
using the stud tool 800044.
Mount the nuts by hand.
12 Mount the distance sleeves 800042
and the hydraulic
tool 800041 into position on the side screw (A
2
) on the rear side
on a in-line engine, and B-bank on a V-engine, i.e. the straight
side of the bearing cap, see Fig 10-2. One or two nuts can be
tightened simultaneously on the same side, see Fig 10-1.
13 Rise the hydraulic pressure in the tool
to 100 bar and
turn the nut to contact by the pin 800043.
14 Mount the distance sleeve
800095 into position on the
main bearing screw (B
1
) and insert the pin 800049, see Fig
10-1.
15 Mount the hydraulic tool
800046 on the same main
bearing screw, by using the tool 800051.
16 Apply the sleeve and hydraulic cylinder
onto main
bearing screw (B
2
) by the same procedure.
17 Tighten the nuts of the main bearing screws
as de-
scribed in adjacent figure. Both screws must be tightened at
the same time and in two steps. Turn the nuts with the pin
800049.
Note!
The hydraulic pressure in the tool must keep stable when
tightening the nuts.
18 Connect the hydraulic pump and hose
to the tool on
the already pretightened side screw (A
2
), see Fig 10-1.
19 Rise the hydraulic pressure in the tool
to 250 bar and
turn the nut to contact by the pin 800043.
20 Mount the distance sleeve 800042
and the hydraulic
tool 800041 into position on the opposite side screw (A
1
).
21 Rise the hydraulic pressure in the tool
to 250 bar and
turn the nut (A
1
) to contact.
22 Tighten the side screw (A
2
)
to full stated pressure.
Hydraulic oil
REASSEMBLY
1. Mount the nuts, the distance
sleeves and the cylinders.
2. Connect the hoses, open the
pressure release valve.
Tighten the cylinders to expel
oil out of these.
3. Close the valve and pump
pressure to stated value for
step 1.
4. Turn the nuts until close
contact is reached.
5. Release the pressure by
opening the valve.
6. Close the valve and pump
pressure to the full stated value.
7. Turn the nuts until close
contact is reached.
8. Open the valve and remove
the tool set.
10
Engine Block with Bearings, Oil Sump and Cylinder Liner
32-200150
10 - 6
WÄRTSILÄ 32/34SG
Summary of Contents for PAAE051728
Page 4: ......
Page 18: ...Appendix B Welding Precautions 200640 00 6...
Page 26: ...01 Main Data Operating Data and General Design 32 200634 01 01 8 W RTSIL 32...
Page 60: ...Appendix A Environmental Hazards 200507 02A 10...
Page 68: ...Page 7 7 Document No 4V92A0645 Rev j...
Page 84: ...03 Start Stop and Operation 32 200402 04 03 12 W RTSIL 32...
Page 98: ...04 Maintenance Schedule 32 200623 01 04 14 W RTSIL 32...
Page 154: ...07 Tightening Torques and Use of Hydraulic Tools 32 200643 01 07 30 W RTSIL 32...
Page 162: ...08 Operating Troubles Emergency Operation 32 200402 01 08 8 W RTSIL 32...
Page 164: ...Specific Installation Data 2005 01 09 2...
Page 178: ...10 Engine Block with Bearings Oil Sump and Cylinder Liner 32 200150 10 14 W RTSIL 32 34SG...
Page 216: ...Appendix A Testing of cylinder tightness 32 200142 A 4 W rtsil 20 32 34...
Page 226: ...13 Camshaft Driving Gear 32 200546 02 13 10 W RTSIL 32...
Page 254: ...15 Turbocharging and Air Cooling 32 200549 10 15 20 W RTSIL 32...
Page 274: ...16 Injection System 32 200627 01 16 20 W RTSIL 32...
Page 280: ...Fuel System 32 200508 07 17 6 W RTSIL 32...
Page 314: ...19 Cooling Water System 32 200050 19 14 W RTSIL 32...
Page 394: ...23 Instrumentation and Automation 32 200115 II 23 60 W RTSIL 32...