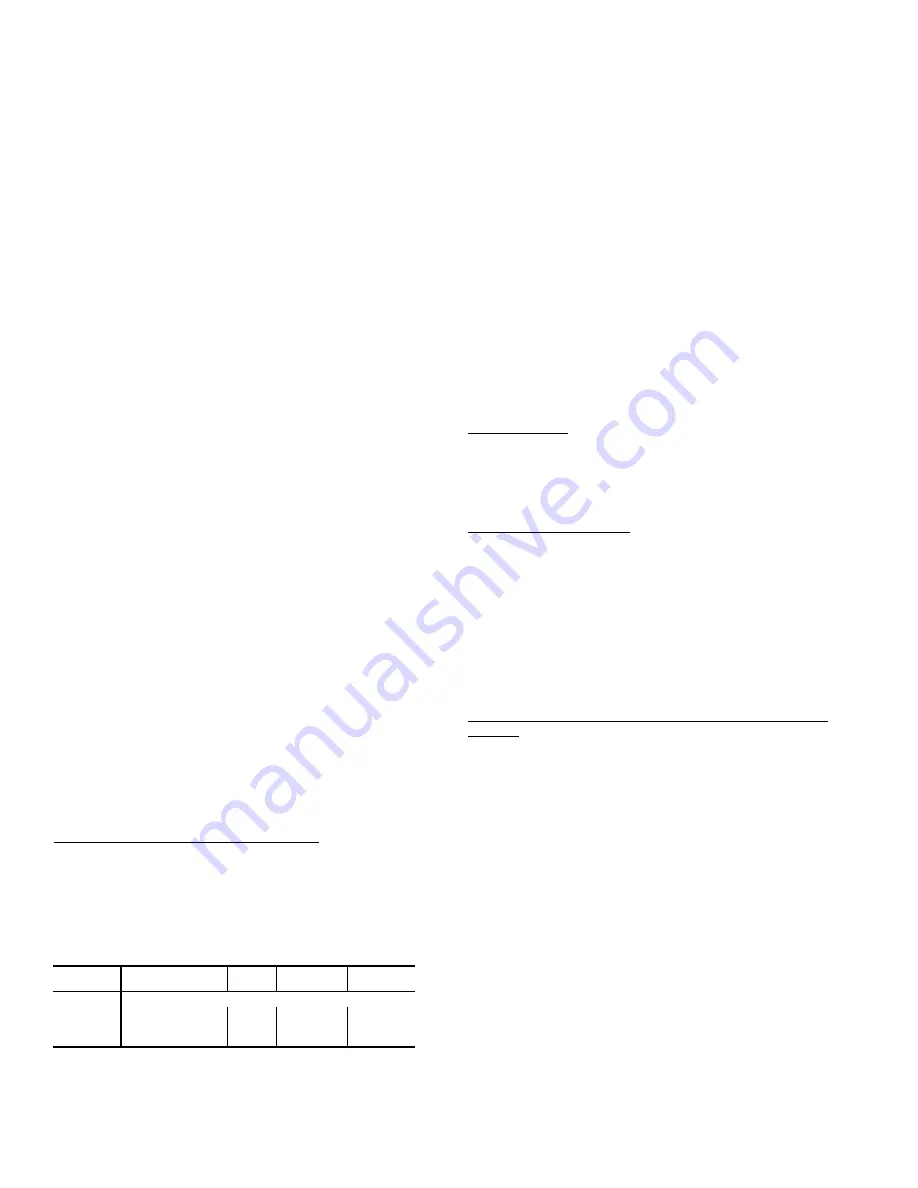
42
This “SUM” will be compared against the “Z” calculations
in determining whether cooling stages should be added or
subtracted.
Z Calculation
— For the “Z” calculation, the control attempts
to determine the entering and the leaving-air temperature of the
evaporator coil and based upon the difference between the two
during mechanical cooling, and then determines whether to
add or subtract a stage of cooling. This is the adaptive element.
The entering-air temperature is referred to as
MAT
(mixed-air temperature) and the leaving-air temperature of the
evaporator coil is referred to as
EDT
(evaporator discharge
temperature). They are found at the local display under the
Temperatures
CTRL
sub-menu.
The main elements to be calculated and used in the calcula-
tion of SumZ are:
1) the rise per percent capacity (
R.PCT
)
2) the amount of expected rise for the next cooling stage
addition
3) the amount of expected rise for the next cooling stage
subtraction
The calculation of “Z” requires two variables,
Z.PLU
used
when adding a stage and
Z.MIN
used when subtracting a stage.
They are calculated with the following formulas:
Z.PLU
=
Z.GN
* (10 + (4*(–
ADD.R
))) * 0.6
Z.MIN
=
Z.GN
* (–10 + (4*(–
SUB.R
))) * 0.6
Where:
Z.GN
= configuration used to modify the threshold levels used
for staging (
Configuration
COOL
Z.GN
)
ADD.R
=
R.PCT
*
(
C.CAP
– capacity after adding a cooling
stage)
SUB.R
=
R.PCT
* (
C.CAP
– capacity after subtracting a cool-
ing stage)
Both of these terms,
Z.PLU
and
Z.MIN
,
represent a thresh-
old both positive and negative upon which the “SUM”
calculation must build up to in order to cause the compressor to
stage up or down.
Comparing SUM and Z
— The “SUM” calculation is com-
pared against
Z.PLU
and
Z.MIN
.
• If “SUM” rises above
Z.PLU
, a cooling stage is added.
• If “SUM” falls below
Z.MIN
, a cooling stage is subtracted.
There is a variable called
SMZ
which is described in the
SumZ Cooling Algorithm section and which can simplify the
task of watching the demand build up or down over time. It is
calculated as follows:
If SUM is positive:
SMZ
= 100*(SUM/
Z.PLU
)
If SUM is negative:
SMZ
= –100*(SUM/
Z.MIN
)
Mixed Air Temperature Calculation (MAT)
— The mixed-
air temperature is calculated and is a function of the economiz-
er position. Additionally there are some calculations in the con-
trol which can zero in over time on the relationship of return
and outside air as a function of economizer position. There are
two configurations which relate to the calculation of “MAT.”
These configurations can be located at the local display under
Configuration
UNIT
.
MAT Calc Config
(
MAT.S
)
—
This configuration gives the
user two options in the processing of the mixed-air temperature
(MAT) calculation:
•
MAT.S
= 0
There will be no MAT calculation.
•
MAT.S
= 1
The control will attempt to learn MAT over time. Any time
the system is in a vent mode and the economizer stays at a
particular position for long enough, MAT = EDT. Using this
method, the control has an internal table whereby it can
more closely determine the true MAT value.
•
MAT.S
= 2
The control will not attempt to learn MAT over time.
To calculate MAT linearly, the user should reset the MAT
table entries by setting
MAT.R
to YES. Then set
MAT.S
= 2
.
The control will calculate MAT based on the position of the
economizer and outside air and return air temperature.
To freeze the MAT table entries, let the unit run with
MAT.S
= 1
. Once sufficient data has been collected, change
MAT.S
= 2
. Do not reset the MAT table.
Reset MAT Table Entries?
(
MAT.R
)
—
This configuration al-
lows the user to reset the internally stored MAT learned config-
uration data back to the default values. The defaults are set to a
linear relationship between the economizer damper position
and OAT and RAT in the calculation of MAT.
SumZ Overrides
—
There are a number of overrides to the
SumZ algorithm which may add or subtract stages of cooling.
• High Temp Cap Override (
H.TMP
)
• Low Temp Cap Override (
L.TMP
)
• Pull Down Cap Override (
PULL
)
• Slow Change Cap Override (
SLOW
)
Economizer Trim Override
—
The unit may drop stages of
cooling when the economizer is performing free cooling and
the configuration
Configuration
ECON
E.TRM
is set to
Yes. The economizer controls to the same supply air setpoint as
mechanical cooling does for SumZ when
E.TRM
= Yes. This
allows for much tighter temperature control as well as cutting
down on the cycling of compressors.
For a long cooling session where the outside-air tempera-
ture may drop over time, there may be a point at which the
economizer has closed down far enough were the unit could
remove a cooling stage and open up the economizer further to
make up the difference.
Mechanical Cooling Lockout (
Configuration
COOL
MC.LO
)
—
This configuration allows a configurable outside-
air temperature setpoint below which mechanical cooling will
be completely locked out.
DEMAND LIMIT CONTROL — Demand Limit Control
may override the cooling algorithm to limit or reduce cooling
capacity during run time. The term Demand Limit Control re-
fers to the restriction of machine capacity to control the amount
of power that a machine will use. This can save the owner
money by limiting peaks in the power supply. Demand limit
control is intended to interface with an external Loadshed De-
vice either through CCN communications, external switches,
or 4 to 20 mA input.
The control has the capability of loadshedding and limiting
in 3 ways:
• Two discrete inputs tied to configurable demand limit
setpoint percentages.
• An external 4 to 20 mA input that can reset capacity back
linearly to a setpoint percentage.
• CCN loadshed functionality.
NOTE: It is also possible to force the demand limit variable
(
Run Status
COOL
DEM.L
).
To use Demand Limiting, select the type of demand limiting
to use. This is done with the Demand Limit Select configura-
tion (
Configuration
DMD.L
DM.L.S
).
To view the current demand limiting currently in effect,
look at
Run Status
COOL
DEM.L
.
ITEM
EXPANSION
RANGE
CCN
POINT
DEFAULTS
UNIT
UNIT CONFIGURATION
MAT.S
MAT Calc Config
0 - 2
MAT_SEL
1
MAT.R
Reset MAT Table
Entries?
Yes/No
MATRESET
No
Summary of Contents for Carrier Weathermaker 48A2
Page 105: ...105 Fig 20 Typical Main Control Box Wiring Schematic 48 50A2 A3 A4 A5 Units...
Page 106: ...106 Fig 21 Typical Auxiliary Control Box Wiring Schematic...
Page 107: ...107 Fig 22 Typical 2 Stage Gas Heat Wiring Schematic Size 060 Units Shown a48 8357...
Page 108: ...108 TO NEXT PAGE Fig 23 Typical Staged Gas Heat Wiring Schematic Size 060 Units Shown A48 7296...
Page 109: ...109 Fig 23 Typical Staged Gas Heat Wiring Schematic Size 060 Units Shown cont A48 8358...
Page 110: ...110 Fig 24 Typical Electric Heat Control Schematic 50 Series Size 060 Units Shown a50 8228...
Page 111: ...111 Fig 25 Typical Power Schematic 48 50A2 A3 A4 A5 060 Unit Shown...
Page 112: ...112 Fig 26 Typical Low Ambient Controls Option Wiring...
Page 113: ...113 Fig 27 Typical Small Chassis Component Location Size 020 035 Units...
Page 114: ...114 Fig 28 Typical Large Chassis Component Locations Size 040 060 Units...
Page 118: ...118 Fig 30 Economizer Control Board ECB1 and VAV Control Board ECB2 A48 7706...
Page 142: ...142 A48 3733 Fig 56 Main Burner Removal...
Page 176: ...176 APPENDIX C VFD INFORMATION cont Fig F Internal Enclosure Fan Replacement A48 7716...