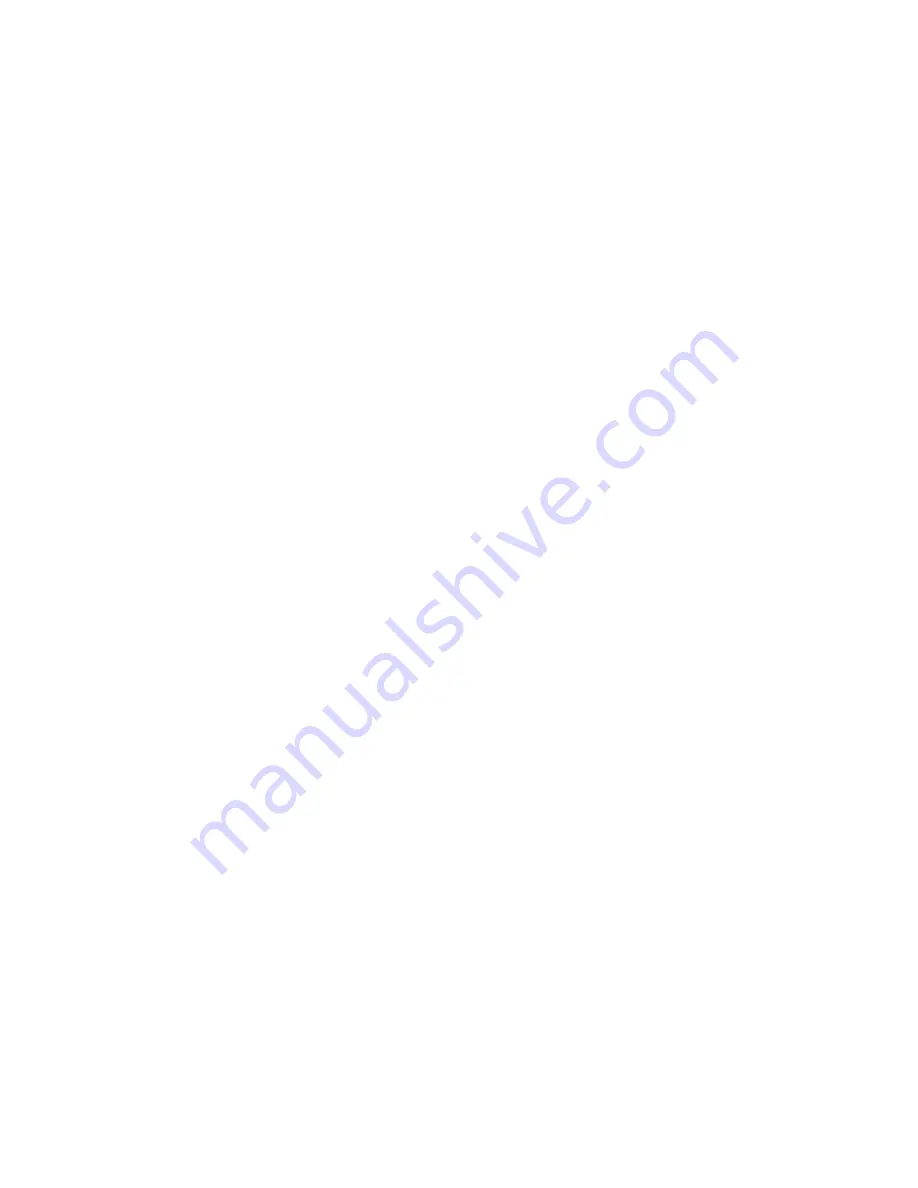
194
APPENDIX F — OPTIONAL LOW AMBIENT MOTORMASTER
®
V CONTROL (cont)
Unit size (
Configuration
UNIT
SIZE
), refrigerant type
(
Configuration
UNIT
RFG.T
), and condenser heat ex-
changer type (
Configuration
UNIT
CND.T
) are used to
determine if the second stage fans are configured to respond to
a particular refrigerant circuit (independent control) or both re-
frigerant circuits (common control). The 48/50A2, A3, A4, A5
060 units with microchannel (MCHX) condenser heat ex-
changers are the only units that utilize independent fan
controls.
There are configurations provided for head pressure and
motor master control that can be found at the local display
under
Configuration
COOL
.
Motormaster Control (M.M.) —
[MOTRMAST] The
condenser fan staging control for the unit shall be managed di-
rectly by the
Comfort
Link controls through the use of VFDs.
There shall be no VFDs installed in the standard unit. This con-
figuration must be set to YES if the optional condenser fan
VFDs are installed on the unit. Setting this configuration to
YES alters the condenser fan staging sequence to accommo-
date the Motormaster control algorithm.
The standard unit is capable of mechanical cooling opera-
tion down to 32 F outdoor temperature. With the addition of ac-
cessory Motormaster V speed control on the stage 1 condenser
fan(s), mechanical cooling operation down to –20 F outdoor
temperature is possible.
This configuration shall have a range of NO/YES and shall
default to NO.
NOTE: Setting Motormaster control to YES shall automati-
cally enable the SCB2 PCB at LEN address 0x62 and the 4 to
20 mA outputs to control the VFDs.
Head Pressure Setpoint (HPSP) —
[HPSP] This is
the head pressure setpoint used by the ComfortLink control
during condenser fan, head pressure control. This configuration
shall have a range of 80 to 150 F and a default of 110 F.
Compressor Lockout Temperature
(MC.LO) —
[OATLCOMP] This configuration defines the
outdoor air temperature below which mechanical cooling is
locked out. To make proper use of Motormaster control, it shall
be necessary for an operator to manually change this setting.
This configuration shall have a range of –20 to 55 F and a de-
fault of 40 F.
Motormaster Setpoint Offset (MM.OF) —
[MMSPOFST] This value is added to HPSP in order to calcu-
late the Motormaster Setpoint MM_SP. This value shall have a
range of –20 to 20 and a default of –10.
Motormaster PD Run Rate (MM.RR) —
[MM_RATE] This is the number of seconds between execu-
tion of the Motormaster ComfortLink PD routine. This value
shall have a range of 10 to 120 and a default of 5.
Motormaster Proportional Gain (MM.PG) —
[MM_PG] This is the proportional gain for the Motormaster
control PD control loop. This value shall have a range of 0.0 to
5.0 and a default of 1.0.
Motormaster Integration Time (MM.TI) —
[MM_TI] This is the integration time constant for the Motor-
master control PD control loop. This value shall have a range
of 0.5 to 50 and default of 30.
Motormaster Setpoint (MM.SP) —
[MM_SP] If the
unit is configured for Motormaster control, then this is the set-
point to which the ComfortLink PD routine will modulate
VFD fan speed. The Motormaster setpoint is calculated as HP-
SP+MMSPFOST. This setpoint shall be used by both the A
and B circuits.
Condenser Fan Control Outputs —
There are two
outputs (MBB Relays) provided to control head pressure:
CD.F.A
Condenser Fan Circuit A CONDFANA
CD.F.B
Condenser Fan Circuit B CONDFANB
MM.F.A
Motormastr Fan Circuit A MM_A_RUN
MM.F.B
Motormastr Fan Circuit B MM_B_RUN
Outputs
FANS
CD.F.A
(Condenser Fan Circuit A) (MBB
Relay 6 - OFC1,4) — For size 60 ton units with MCHX con-
densers, MBB - Relay 6 drives OFC4 and compressor contac-
tor B1 or B2 auxiliary contacts drive OFC1.
Outputs
FANS
CD.F.B
(Condenser Fan Circuit B) (MBB
Relay 5 - OFC2).
Outputs
FANS
MM.F.A
(Motormastr Fan Circuit A) (SCB
Relay 1) — This output shall be used as the run enable of cir-
cuit A Motormaster VFD.
Outputs
FANS
MM.F.B
(Motormastr Fan Circuit B) (SCB
Relay 2) — This output shall be used as the run enable of the
circuit B Motormaster VFD.
In addition, if Motormaster control is enabled, there shall be
two 4 to 20 mA analog outputs to modulate fan speed for Mo-
tormaster operation:
A.VFD
MtrMaster A Commanded % MM_A_VFD
B.VFD
MtrMaster B Commanded % MM_B_VFD
For Motormaster fan of Circuit A to modulate,
MM_A_RUN must be ON.
For Motormaster fan of Circuit B to modulate,
MM_B_RUN must be ON.
Condenser Fan Inputs —
The control loop uses the
following inputs for head pressure control:
SCT.A
Cir A Sat.Condensing Tmp SCTA
SCT.B
Cir B Sat.Condensing Tmp SCTB
OAT
Outside Air Temperature OAT
SCTA and SCTB are calculated using the corresponding
discharge pressure transducer:
DP.A
Cir A Discharge Pressure DP_A
DP.B
Cir B Discharge Pressure DP_B
A description of operation during the failure of a sensor can
be found in P44 Failure Mode Operation. A description of the
thermistor and transducer alarms/alerts can be found in P.98
Alerts/Alarms.
Condenser Fan Staging —
For 48/50A020-035 size
units, there are two outdoor fans that are common to both re-
frigerant circuits. The control cycles two stages of outdoor
fans, one fan per stage, to maintain acceptable head pressure.
For 48/50A040 and 050 size units, there are four outdoor
fans that are common to both refrigerant circuits. The control
cycles two stages of outdoor fans, two fans per stage, to main-
tain acceptable head pressure.
For 48/50A060 size units, there are six outdoor fans that are
common to both refrigerant circuits (size 060 MCHX units
have 4 fans). The control cycles three stages of outdoor fans,
two fans for stage one, four fans for stage two, and six fans for
stage three to maintain acceptable head pressure.
Summary of Contents for Carrier Weathermaker 48A2
Page 105: ...105 Fig 20 Typical Main Control Box Wiring Schematic 48 50A2 A3 A4 A5 Units...
Page 106: ...106 Fig 21 Typical Auxiliary Control Box Wiring Schematic...
Page 107: ...107 Fig 22 Typical 2 Stage Gas Heat Wiring Schematic Size 060 Units Shown a48 8357...
Page 108: ...108 TO NEXT PAGE Fig 23 Typical Staged Gas Heat Wiring Schematic Size 060 Units Shown A48 7296...
Page 109: ...109 Fig 23 Typical Staged Gas Heat Wiring Schematic Size 060 Units Shown cont A48 8358...
Page 110: ...110 Fig 24 Typical Electric Heat Control Schematic 50 Series Size 060 Units Shown a50 8228...
Page 111: ...111 Fig 25 Typical Power Schematic 48 50A2 A3 A4 A5 060 Unit Shown...
Page 112: ...112 Fig 26 Typical Low Ambient Controls Option Wiring...
Page 113: ...113 Fig 27 Typical Small Chassis Component Location Size 020 035 Units...
Page 114: ...114 Fig 28 Typical Large Chassis Component Locations Size 040 060 Units...
Page 118: ...118 Fig 30 Economizer Control Board ECB1 and VAV Control Board ECB2 A48 7706...
Page 142: ...142 A48 3733 Fig 56 Main Burner Removal...
Page 176: ...176 APPENDIX C VFD INFORMATION cont Fig F Internal Enclosure Fan Replacement A48 7716...