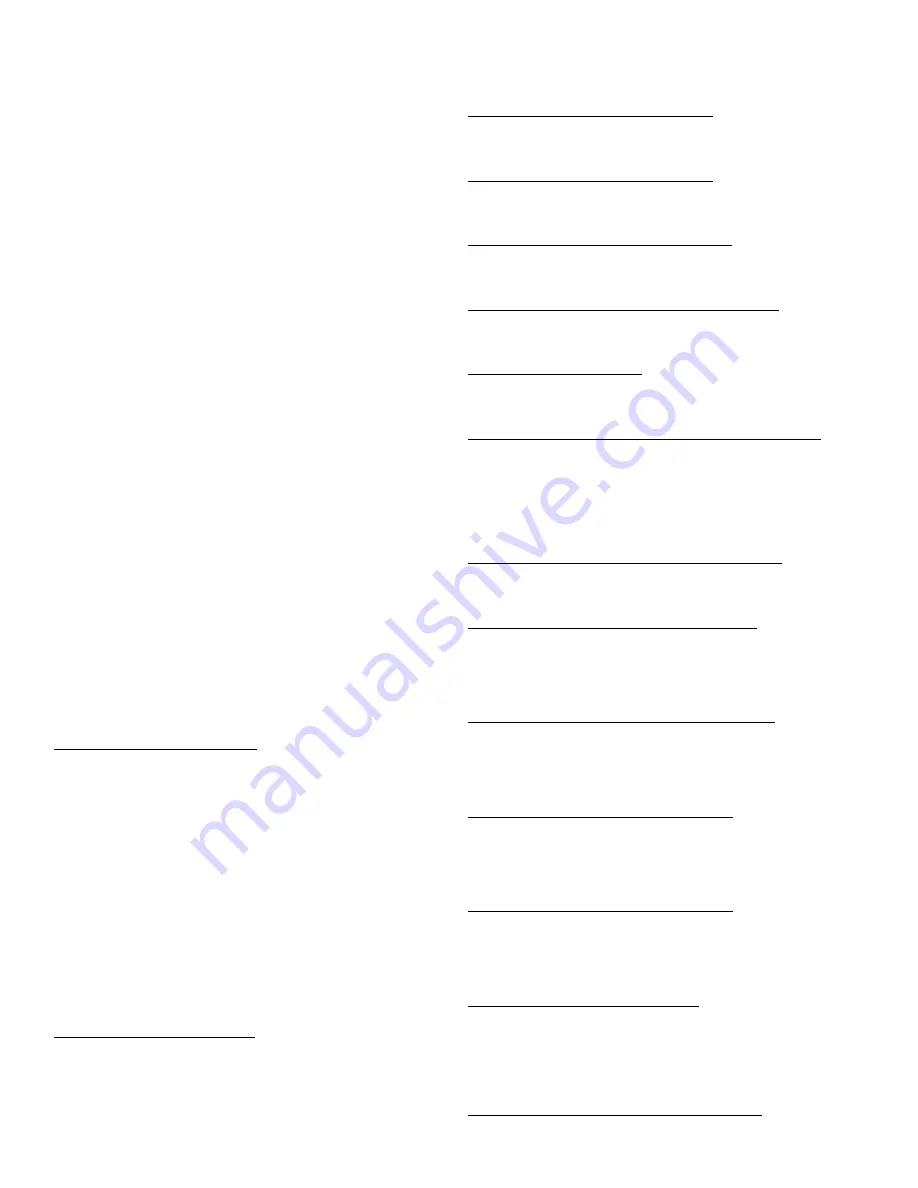
100
thermistor has measured a temperature above 268 F or the
thermistor is short circuited. The digital scroll compressor will
be shut down and alert T128 will be generated. The compres-
sor will be allowed to restart after a 30-minute delay and after
the thermistor temperature is below 250 F. If five high dis-
charge temperature alerts have occurred within four hours,
alarm A128 will be generated which will necessitate a manual
reset to start the compressor.
There will be a start-up delay if the outside-air temperature
is too low. When the outdoor ambient is below 60 F, during ini-
tial start-up, saturated suction temperature will be ignored for a
period of 5 minutes. When
Temperatures
REF.T
SSTA
or
Temperatures
REF.T
SSTB
is less than 20 F for 4 minutes,
less than 10 F for 2 minutes, less than 0° F for 1 minute or less
than –20 F for 20 seconds continuously, the second compressor
of the affected circuit, if it exists, will be shut down with a local
alert (P120, P121) and a 10-minute timeguard will be added to
the compressor. If saturated suction temperature continues to
be less than 20 F for 4 minutes, less than 10 F for 2 minutes,
less than 0° F for 1 minute or less than –20 F for 20 seconds
continuously then compressor no. 1 will be shut down and then
an alert or alarm will be issued.
This failure follows a 3 strike methodology whereby the
first two times a circuit goes down entirely, an alert will be gen-
erated which keeps the circuit off for 15 minutes before allow-
ing the circuit to try again. The third time this happens, an
alarm will be generated which will necessitate a manual reset
to get the circuit back running. It is important to note that a
“strike” is called out only if all compressors in the circuit are
off at the time of alert/alarm.
To prevent nuisance alerts, P120 and P121 show up in the
alarm history and locally at the display but are not broadcast to
the network. To recover from these alerts, a 10-minute holdoff
timer must elapse and the saturated suction temperature must
rise above 29.32 F. If recovery occurs, staging will be allowed
on the circuit again. Again, a “strike” is tied to the circuit going
off entirely, not reducing capacity and recovering. Therefore it
is possible that multiple P120 or P121 alerts may be stored in
alarm history but not broadcast.
If there are 1 or 2 strikes on the circuit and the circuit recov-
ers for a period of time, it is possible to clear out the strikes
thereby resetting the strike counter automatically. The control
must have saturated suction temperature greater than or equal
to 34 F for 60 minutes in order to reset the strike counters.
A140 (Reverse Rotation Detected) — A test is made once, on
power up, for suction pressure change on the first activated cir-
cuit. The unit control determines failure is as follows:
The suction pressure of both circuits is sampled 5 seconds
before the compressor is brought on, right when the
compressor is brought on and 5 seconds afterwards. The rate of
suction pressure change from 5 seconds before the compressor
is brought on to when the compressor is brought on is calculat-
ed. Then the rate of suction pressure change from when the
compressor is brought on to 5 seconds afterwards is calculated.
With the above information, the test for reverse rotation is
made. If the suction pressure change 5 seconds after compres-
sion is greater than the suction pressure change 5 seconds be-
fore compression – 1.25, then there is a reverse rotation error.
This alarm will disable mechanical cooling and will require
a manual reset. This alarm may be disabled once the reverse
rotation check has been verified by setting
Configuration
COOL
REV.R
= Yes.
A150 (Unit is in Emergency Stop)
—
If the fire safety input
condition occurs to indicate a fire or smoke condition, then
Alarm code 150 will occur and the unit will be immediately
stopped. Through separate inputs the unit can be put into purge,
evacuation, and pressurization. This requires a manual reset.
If the CCN point name “EMSTOP” in the System table is
set to emergency stop, the unit will shut down immediately and
broadcast an alarm back to the CCN indicating that the unit is
down. This alarm will clear when the variable is set back to
“enable.”
T153 (Real Time Clock Hardware Failure) — A problem has
been detected with the real timeclock on the MBB. Try reset-
ting the power and check the indicator lights. If the alert contin-
ues, the board should be replaced.
A154 (Serial EEPROM Hardware Failure)
— A problem has
been detected with the EEPROM on the MBB. Try resetting
the power and check the indicator lights. If the alarm continues,
the board should be replaced.
T155 (Serial EEPROM Storage Failure Error)
— A problem
has been detected with the EEPROM storage on the MBB. Try
resetting the power and check the indicator lights. If the alert
continues, the board should be replaced.
A156 (Critical Serial EEPROM Storage Failure Error)
— A
problem has been detected with the EEPROM storage on the
MBB. Try resetting the power and check the indicator lights. If
the alarm continues, the board should be replaced.
A157 (A/D Hardware Failure)
—
A problem has been detected
with A/D conversion on the boards. Try resetting the power
and check the indicator lights. If the alarm continues, the board
should be replaced.
A168 (Low Ambient Control Board (SCB2) Comm Failure)
— This alarm indicates that there are communications prob-
lems with the Low Ambient Option SCB2 board. Cooling on
the unit is disabled until communication with the SCB2 control
board is re-established. The alarm will automatically reset.
Reason for failure may be due to incorrect wiring, power loss
to the control board, or damage to the RS-485 drivers on the
LEN bus.
A169 (Expansion Valve Control Board Comm Failure)
—
Cooling is disabled until communication with the EXV control
board is re-established. Recovery is automatic. Reason for fail-
ure may be due to incorrect wiring, power loss to the control.
A171 (Staged Gas Control Board Comm Failure) — This
alarm indicates that there are communications problems with
the staged gas heat control board, which is located in the gas
section on units equipped with staged gas heat. If this alarm
occurs, the staged gas heat will be disabled. The alarm will
automatically reset.
A172 (Controls Expansion Module Comm Failure) — This
alarm indicates that there are communications problems with
the controls expansion board. All functions performed by the
CEM will stop, which can include demand limit, reset, fire
control modes, and the fan status switch. The alarm will auto-
matically reset.
A173 (ECB1 Board Communication Failure) — This alarm
indicates that there are communications problems with the
economizer control board. This will result in the economizer
and the power exhaust not working and the dampers to be fully
closed. The exhaust fans will stop. The alarm will automati-
cally reset.
A174 (ECB2 Board Communication Failure) — This alarm
indicates that there are communications problems with the
ECB2 which controls the VAV unit indoor fan inverter speed
and hot gas bypass on CV and VAV units. Because the control
of the fan is critical to unit operation, the unit will be stopped.
The alarm will automatically reset.
T177 (4-20 mA Demand Limit Failure)
—
This alert indicates
a problem with the optional remote 4 to 20 mA demand limit
signal (
Inputs
4-20
DLM.M
) that is connected to the CEM
module (if the signal reads less than 2 mA). If this occurs, then
demand limiting will be disabled. The unit must be configured
for 4 to 20 mA Demand Limiting using the Demand Limit
Select (
Configuration
DMD.L
DM.L.S
).
T178 (4-20 mA Static Pressure Reset/VFD Failure) — If this
transducer fails (if the signal reads less than 2 mA on the input
Summary of Contents for Carrier Weathermaker 48A2
Page 105: ...105 Fig 20 Typical Main Control Box Wiring Schematic 48 50A2 A3 A4 A5 Units...
Page 106: ...106 Fig 21 Typical Auxiliary Control Box Wiring Schematic...
Page 107: ...107 Fig 22 Typical 2 Stage Gas Heat Wiring Schematic Size 060 Units Shown a48 8357...
Page 108: ...108 TO NEXT PAGE Fig 23 Typical Staged Gas Heat Wiring Schematic Size 060 Units Shown A48 7296...
Page 109: ...109 Fig 23 Typical Staged Gas Heat Wiring Schematic Size 060 Units Shown cont A48 8358...
Page 110: ...110 Fig 24 Typical Electric Heat Control Schematic 50 Series Size 060 Units Shown a50 8228...
Page 111: ...111 Fig 25 Typical Power Schematic 48 50A2 A3 A4 A5 060 Unit Shown...
Page 112: ...112 Fig 26 Typical Low Ambient Controls Option Wiring...
Page 113: ...113 Fig 27 Typical Small Chassis Component Location Size 020 035 Units...
Page 114: ...114 Fig 28 Typical Large Chassis Component Locations Size 040 060 Units...
Page 118: ...118 Fig 30 Economizer Control Board ECB1 and VAV Control Board ECB2 A48 7706...
Page 142: ...142 A48 3733 Fig 56 Main Burner Removal...
Page 176: ...176 APPENDIX C VFD INFORMATION cont Fig F Internal Enclosure Fan Replacement A48 7716...