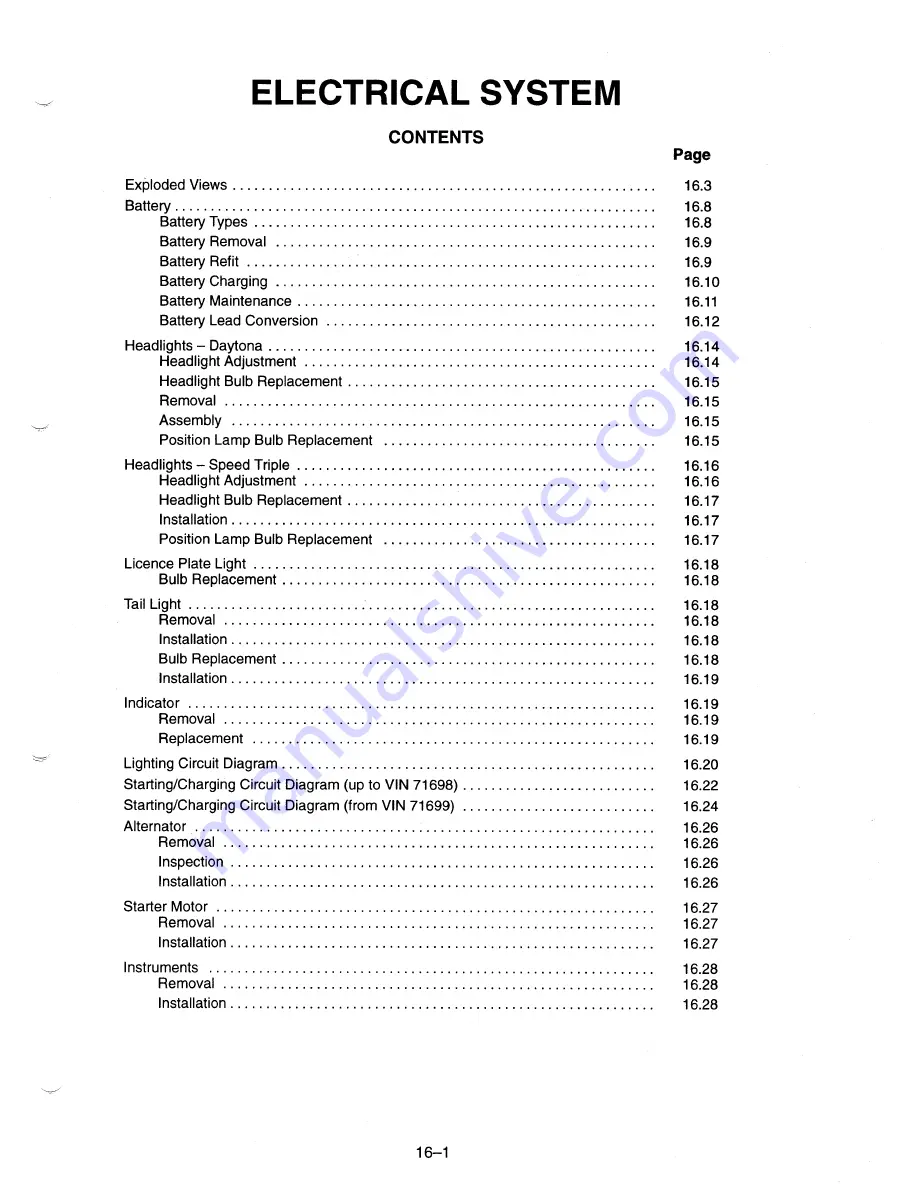
ELECTRICAL SYSTEM
CONTENTS
Page
Exploded
Views
...........................................................
16.3
Battery...................................................................
16.8
BatteryTy
p
es
........................................................
16.8
BatteryRemoval
.............
......................................
16.9
BatteryRefit
..........................................................
16.9
BatteryChar
g
in
g
.....
..............................................
16.10
BatteryMaintenance
..................................................
16.11
BatteryLead Conversion ..............................................
16.12
Headli
g
hts
-
Daytona ......................................................
16.14
Headli
g
htAd
j
ustment
.................................................
16.14
Headli
g
htBulb
Replacement ...........................................
16.15
Removal............................................................
16.15
Assembly
.........................................................
16.15
PositionLamp Bulb Replacement .......................................
16.15
Headli
g
hts
-
Speed Triple ..................................................
16.16
Headli
g
htAd
j
ustment
.................................................
16.16
Headli
g
htBulb
Replacement ...........................................
16.17
Installation...........................................................
16.17
PositionLamp Bulb Replacement
......................................
16.17
LicencePlate Light ........................................................
16.18
BulbReplacement ....................................................
16.18
TailLight ........................:........................................
16.18
Removal............................................................
16.18
Installation...........................................................
16.18
BulbReplacement ....................................................
16.18
Installation...........................................................
16.19
Indicator.................................................................
16.19
Removal............................................................
16.19
Replacement........................................................
16.19
Lighting Circuit Diagram ....................................................
16.20
16.20
Starting/Charging Circuit Diagram (up to VIN 71698) ...........................
16.22
Starting/Charging Circuit Diagram (from VIN 71699) ...........................
16.24
Alternator...............................................................
16.26
Removal............................................................
16.26
Inspection...........................................................
16.26
Installation..................... .....................................
16.26
StarterMotor .............................................................
16.27
Removal............................................................
16.27
Installation...........................................................
16.27
Instruments..............................................................
16.28
Removal............................................................
16.28
Installation...........................................................
16.28
16-1
Summary of Contents for Daytona 955i
Page 1: ...T595 DAYTONA T509 SPEED TRIPLE DAYTONA 955i SPEED TRIPLE 955cc...
Page 32: ...MAINTENANCE CONTENTS Page Introduction 2 2 ServiceCheck Sheets 2 2 MaintenaceChart 2 3 2 1...
Page 37: ...Exploded View Cam Cover 25 Nm ThUMI CYLINDER HEAD CAMSHAFT 3 3 3...
Page 38: ...Exploded View Camshaft and Camshaft Drive 10 Nm 9 Nm 18 Nm 3 CYLINDER HEAD CAMSHAFT T MPH 3 4...
Page 64: ...12 Nm 9Nm 12 Nm N 0 0 0 0 4 CLUTCH Exploded View Clutch Cover 9 Nm 5 Nm 9Nm 4 2...
Page 65: ...105 Nm 10 Nm 4 3 T MPH CLUTCH 4 Exploded View Clutch Assembly...
Page 66: ...6 Nm 4 CLUTCH Exploded View Clutch Controls 1 Nm 15 Nm V 4 4...
Page 75: ...5 2 5 BALANCERS Exploded View Balancer Shaft 40 Nm if fitted J 40 Nm...
Page 107: ...132 Nm 7 2 7 TRANSMISSION TkQ2WH Exploded View Input and Output Shafts...
Page 108: ...lONm 10 Nm 12Nm 16 40 Nm TIUMI MP1 TRANSMISSION 7 Exploded View Auxiliary Gears 12 Nm 7 3...
Page 109: ...12 10 Nm 7 TRANSMISSION Exploded View Selector Mechanism 12 Nm 7 4...
Page 110: ...7 5 TRANSMISSION 7 Exploded View Gear Pedal etc JJ 9Nm 9Nm 9Nm 28 Nm...
Page 128: ...O p 0 0 O o 8 Nm M WE 8 LUBRICATION TJMPH Exploded View Sump 28 Nm 0 10 Nm 12 Nm 10 Nm 8 2...
Page 129: ...9Nm l 12 Nm TwMaIi LUBRICATION 8 Exploded View Oil Pump and Gears 15 Nm 9Nm 8 3...
Page 130: ...2 8 4 8 LUBRICATION Exploded View Daytona Oil Cooler 25 Nm 25 Nm 25 Nm...
Page 132: ...8 LUBRICATION 3 Cylinder Oil Circuit Q D 0 D D D LI Li 6 9 11 gact 8 6...
Page 144: ...FUEL SYSTEM ENGINE MANAGEMENT 9 Exploded View Fuel Tank and Pump 12 Nm b I s JIII 6Nm 9 3...
Page 168: ...FUEL SYSTEM ENGINE MANAGEMENT 9 9 27...
Page 246: ...Exploded View Cooling System 12 Nm 0 0 5Nm 10 Nm 0 9Nm M 10 COOLING SYSTEM TiUiMII 10 2...
Page 257: ...Exploded View Rear Hub A K1 J I TIUMI MPII REAR SUSPENSION 11 11 3...
Page 258: ...11 REAR SUSPENSION Exploded View Rear Suspension Unit 48 Nm 11 4...
Page 259: ...48 Nm iiii REAR SUSPENSION 11 Exploded View Drop Drag Link C e 11 5...
Page 282: ...um 1 12 FRONT SUSPENSION STEERING Y jHn Exploded View Tall Handlebars 35 Nm I 12 4...
Page 294: ...Exploded View Rear Brake Master Cylinders 25 Nm N1 25 Nm 7 Nm 13 4 7N 13 BRAKING SYSTEM ThJPII...
Page 313: ...1 14 WHEELS TYRES _ Exploded view Front Wheel 60 Nm 14 2...
Page 314: ...i 1 UNI WHEELS TYRES 14 Exploded View Rear Hub 146 Nm ON 14 3...
Page 327: ...Exploded View Seat Rails 40 Nm 15 3 Nm 1 U 1 B OD YWORK FRAME 15...
Page 329: ...Nm 9 Nm 9 Nm 9Nm 9 Nm 15 5 9Nm i 9 Nm h I 1 1 U hI BODYWORK FRAME 15 Exploded View Rear Panels...
Page 344: ...Exploded View Instruments o ELECTRICAL SYSTEM 16 a _ 5 Nm 6Nm 6 Nm 16 3...
Page 345: ...16 ELECTRICAL SYSTEM Exploded View Alternator and Starter Motor Nlllllllllll 00 16 4...
Page 346: ...Nm tUnNt slut ELECTRICAL SYSTEM 16 Exploded View Daytona Headlight 6 Nm 9 Nm o 6Nm o 9 Nm 16 5...
Page 348: ...ELECTRICAL SYSTEM 16 Exploded View Rear Lights and Indicators U I I U I 18 Nm 16 7...
Page 366: ...Circuit Diagram Starting Charging from VIN 71699 TN z z 0 p8HIi N j 1 14 13 16 25...
Page 372: ......
Page 374: ......
Page 375: ...Triumph Motorcycles Limited Jacknell Road Hinckley Leicestershire LE10 3BS England...