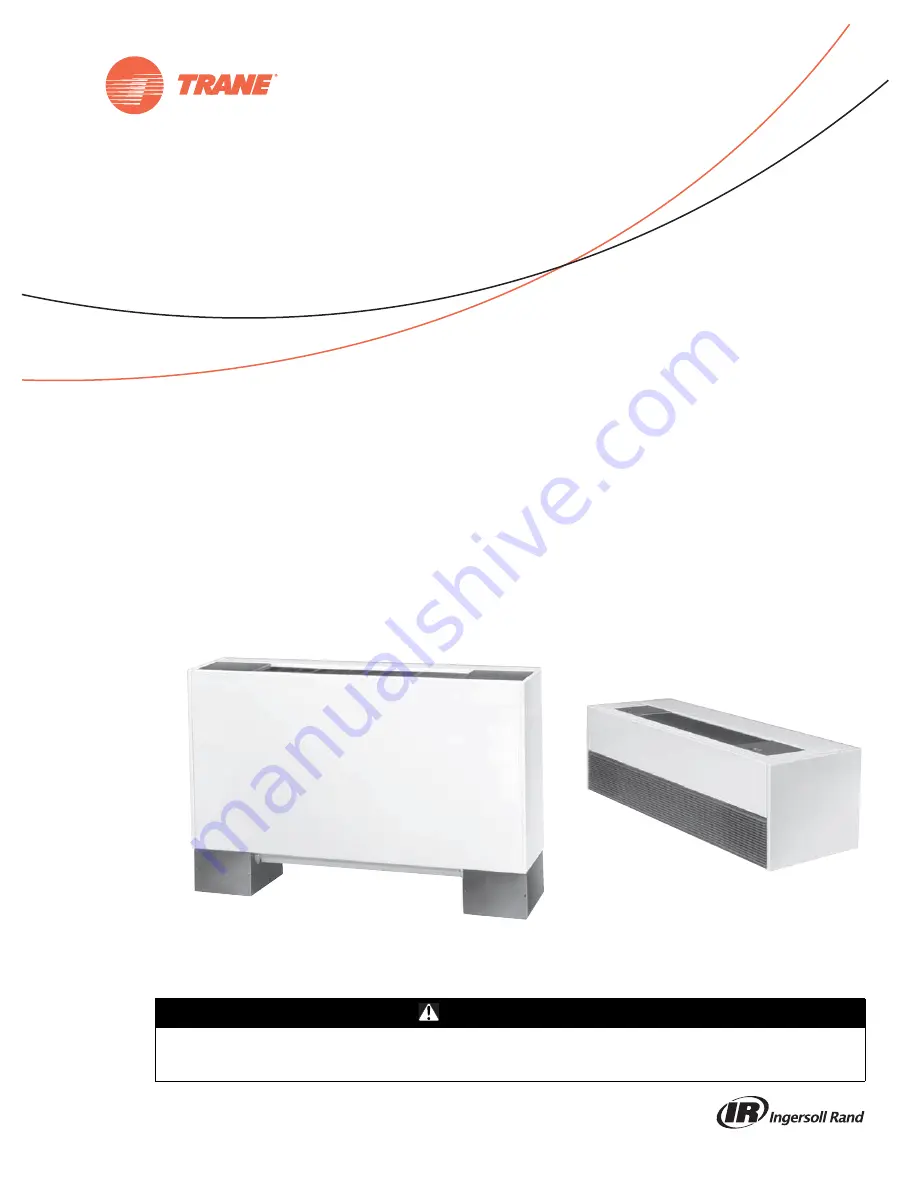
SAFETY WARNING
Only qualified personnel should install and service the equipment. The installation, starting up, and servicing of heating, ventilating, and air-
conditioning equipment can be hazardous and requires specific knowledge and training. Improperly installed, adjusted or altered equipment
by an unqualified person could result in death or serious injury. When working on the equipment, observe all precautions in the literature and
on the tags, stickers, and labels that are attached to the equipment.
Installation, Operation,
and Maintenance
UniTrane™ Fan Coil and Force-Flo™ Cabinet Heater
200 - 1200 CFM
Models FC and FF, Low Vertical Models FCKB and FCLB
UNT-SVX07E-EN
March 2014