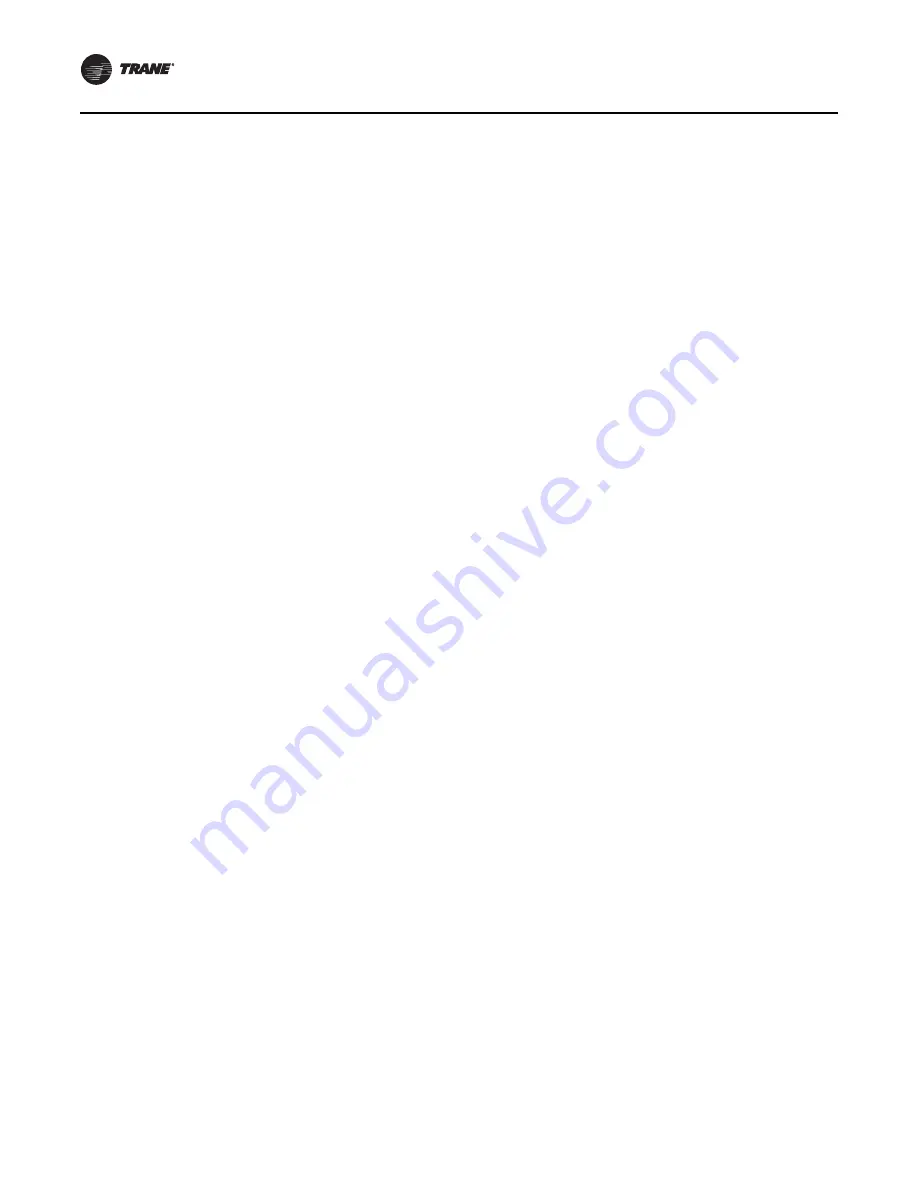
Startup
116
UNT-SVX07E-EN
Discharge Air Tempering
If the controller is in cooling mode, cascade zone control
initiates a discharge air tempering function when:
•
The discharge air temperature falls below the
discharge air temperature low limit setpoint
(configurable using the Tracer TU service tool)
•
All cooling capacity is at a minimum. The discharge air
tempering function allows the controller to provide
heating capacity (if available) to raise the discharge air
temperature to the discharge air temperature low limit
setpoint.
•
The cold outdoor air is brought in through the outdoor
air damper and when the damper is at (high) minimum
position. This causes the discharge air temperature to
fall below the discharge air temperature low limit
setpoint.
Heating or Cooling Mode
The heating or cooling mode can be determined in one of
two ways:
•
By a communicated signal from a BAS or a peer
controller
•
Automatically, as determined by the controller
A communicated heating signal permits the controller to
only heat and a communicated cooling signal permits the
controller to only cool. A communicated auto signal
allows the controller to automatically change from heating
to cooling and vice versa.
In heating or cooling mode, the controller maintains the
zone temperature based on the active heating setpoint and
the active cooling setpoint, respectively. The active
heating and cooling setpoints are determined by the
occupancy mode of the controller.
For 2-pipe and 4-pipe changeover units, normal heat/cool
operation will not begin until the ability to conduct the
desired heating or cooling operation is verified. This is
done using the entering water temperature sampling
function, for which a valid entering water temperature is
required. When neither a hard wired nor a communicated
entering water temperature value is present on
changeover units, the controller operates in only heating
mode and assumes the coil water is hot. The sampling
function is not used.
The entering water temperature sampling function is used
only for changeover applications and for information and
troubleshooting. It does not affect the operation of the
controller. (For more information, refer to the following
section,
“Water Temperature Sampling Function”
.)
Water Temperature Sampling Function
The entering water temperature sampling function is used
with 2-pipe and 4-pipe changeover units and requires a
valid entering water temperature value. If the entering
water temperature value is less than 5°F (2.8°C) above a
valid zone temperature value for hydronic heating, and
greater than 5°F (2.8°C) below a valid zone temperature
value for hydronic cooling, the sampling function is
enabled. When the sampling function is enabled, the
controller opens the main hydronic valve to allow the
water temperature to stabilize. After 3 minutes, the
controller again compares the entering water temperature
value to the zone temperature value to determine if the
desired heating or cooling function can be accomplished.
If the entering water temperature value remains out of
range to accomplish the desired heating/cooling function,
the controller closes the main hydronic valve and waits 60
minutes to attempt another sampling. If the entering water
temperature value falls within the required range, it
resumes normal heating/cooling operation and disables
the sampling function.
Fan Operation
The controller supports 1-, 2-, 3-speed fans and variable-
speed fans. The fan always operates continuously while
either heating or cooling during occupied, occupied
standby, and occupied bypass operation. During
unoccupied operation, the fan cycles between
OFF
and
HIGH
, regardless of the fan configuration. When running
in
AUTO
mode, the fan operates differently based on the
mode and the type of fan.
For 1-, 2-, and 3-speed fans, each time the fan is enabled,
the fan begins operation and runs on high speed for a
period of time (0.5 seconds for fan coils and 3 seconds for
fan coils) before changing to another speed. Initially
running on high speed provides adequate torque to start
the fan motor from the
OFF
position.
Note:
In occupied mode, the controller requires
continuous fan operation because of cascade zone
control. In unoccupied mode, the fan cycles.
Manual Fan Speed Control
Regardless of the fan type, the fan runs continuously at the
desired fan speed during occupied, occupied standby, and
occupied bypass operation as follows:
•
When the controller receives a communicated fan
speed signal (
HIGH
,
MEDIUM
,
LOW
)
•
The associated fan speed switch is set to a specific fan
speed
•
The Supply Fan Speed Request point is overridden
During unoccupied operation, the fan cycles between
OFF
and
HIGH
, regardless of the communicated fan speed
signal or fan speed switch setting (unless either of these is
OFF
, which in turn, will control the fan
OFF
).
The fan turns OFF when:
•
The controller receives a communicated
OFF
signal
•
The fan speed switch is set to
OFF
•
Specific diagnostics are generated
•
The default fan speed is set to
OFF
and the fan is
operating in the
AUTO
mode