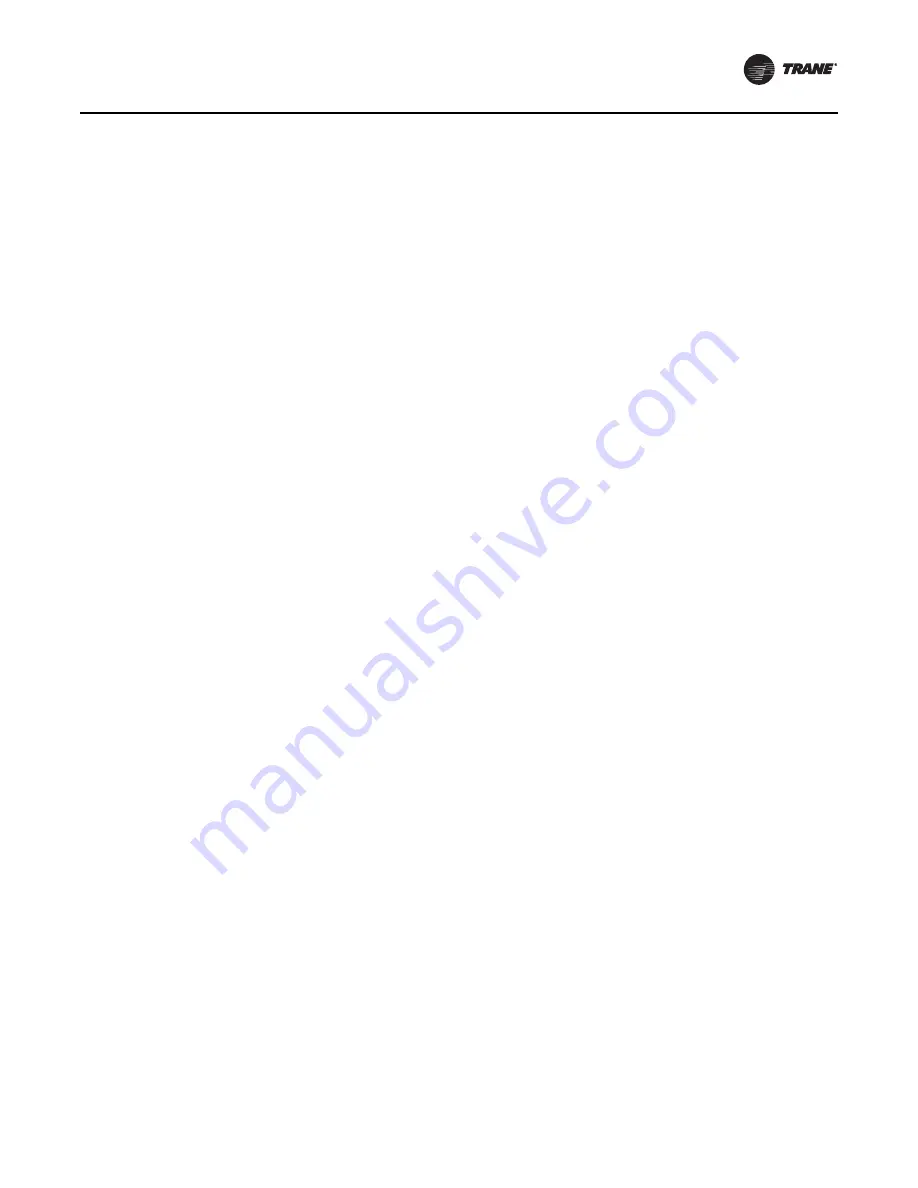
Startup
UNT-SVX07E-EN
107
the controller is determined by using time-of-day
scheduling of the building automation system. The result
of the time-of-day schedule can then be communicated to
the unit controller.
Tracer Summit with Supply Fan Control
If the unit is communicating with Tracer Summit and the
supply fan control programming point is configured for
Tracer (the factory configures as local), Tracer Summit will
control the fan regardless of the fan mode switch position.
When the fan mode switch is set to Off or when power is
restored to the unit, all lockouts (latching diagnostics) are
manually reset. The last diagnostic to occur is retained
until the unit power is disconnected.
For specific instructions regarding Tracer ZN520
Controller, refer to:
CNT-SVX04A-EN Tracer ZN.520 Unit Controller
Installation, Operation and Programming Guide
Cooling Operation
The heating and cooling setpoint high and low limits are
always applied to the occupied and occupied standby
setpoints. During the cooling mode, the controller
attempts to maintain the space temperature at the active
cooling setpoint. Based on the controller’s occupancy
mode, the active cooling setpoint is one of the following:
•
Occupied cooling setpoint
•
Occupied standby cooling setpoint
•
Unoccupied cooling setpoint
The controller uses the measured space temperature, the
active cooling setpoint, and discharge air temperature
along with the control algorithm to determine the
requested cooling capacity of the unit (0 percent–
100 percent). The outputs are controlled based on the unit
configuration and the required cooling capacity. To
maintain space temperature control, the cooling outputs
(modulating hydronic valve, two-position hydronic valve,
or outdoor air economizer damper) are controlled based
on the cooling capacity output.
The cooling output is controlled based on the cooling
capacity. At 0 percent capacity, all cooling capacities are
off and the damper is at minimum position. Between
0 percent and 100 percent capacity, the cooling outputs
are controlled according to modulating valve logic
(modulating valves) or cycled on (2-position valves). As
the load increases, modulating outputs open further and
binary outputs are energized longer. At 100 percent
capacity, the cooling valve or damper is fully open
(modulating valves) or on continuously (and 2-position
valves).
Unit diagnostics can affect fan operation, causing
occupied and occupied standby fan operation to be
defined as abnormal. Refer to
“Diagnostics and
Troubleshooting,” page 129
for more information about
abnormal fan operation.
The controller operates the supply fan continuously when
the controller is in the occupied and occupied standby
modes, for either heating or cooling. The controller only
cycles the fan off with heating and cooling capacity in the
unoccupied mode.
The economizer is used for cooling purposes whenever
the outdoor temperature is below the economizer enable
setpoint and there is a need for cooling. The economizer is
used first to meet the space demand, and other forms of
cooling are used if the economizer cannot meet the
demand alone. See modulating outdoor air damper
operation for additional information.
Cascade cooling control initiates a discharge air tempering
function if the discharge air temperature falls below the
discharge air temperature control low limit, all cooling
capacity is at minimum, and the discharge control loop
determines a need to raise the discharge air temperature.
The controller then provides heating capacity to raise the
discharge air temperature to its low limit.
Discharge Air Tempering
The discharge air tempering function enables when cold
outdoor air is brought in through the outdoor air damper,
causing the discharge air to fall below the discharge air
temperature control low limit. The controller exits the
discharge air tempering function when heat capacity has
been at zero percent for five minutes.
Heating Operation
During heating mode, the controller attempts to maintain
the space temperature at the active heating setpoint.
Based on the occupancy mode of the controller, the active
heating setpoint is one of the following:
•
Occupied heating
•
Occupied standby heating
•
Unoccupied heating
During dehumidification in the heating mode, the
controller adjusts the heating setpoint up to the cooling
setpoint. This reduces the relative humidity in the space
with a minimum of energy usage.
The controller uses the measured space temperature, the
active heating setpoint, and discharge air temperature,
along with the control algorithm, to determine the
requested heating capacity of the unit (0 percent–
100 percent). The outputs are controlled based on the unit
configuration and the required heating capacity.
Unit diagnostics can affect the controller operation,
causing unit operation to be defined as abnormal. Refer to
“Diagnostics and Troubleshooting,” page 129
for more
information about abnormal unit operation.
The heating output is controlled based on the heating
capacity. At 0 percent capacity, the heating output is off
continuously. Between 0 percent and 100 percent
capacity, the heating output is controlled according to
modulating valve logic (3-wire modulating valves) or
cycled on (two-position valves). As the load increases,