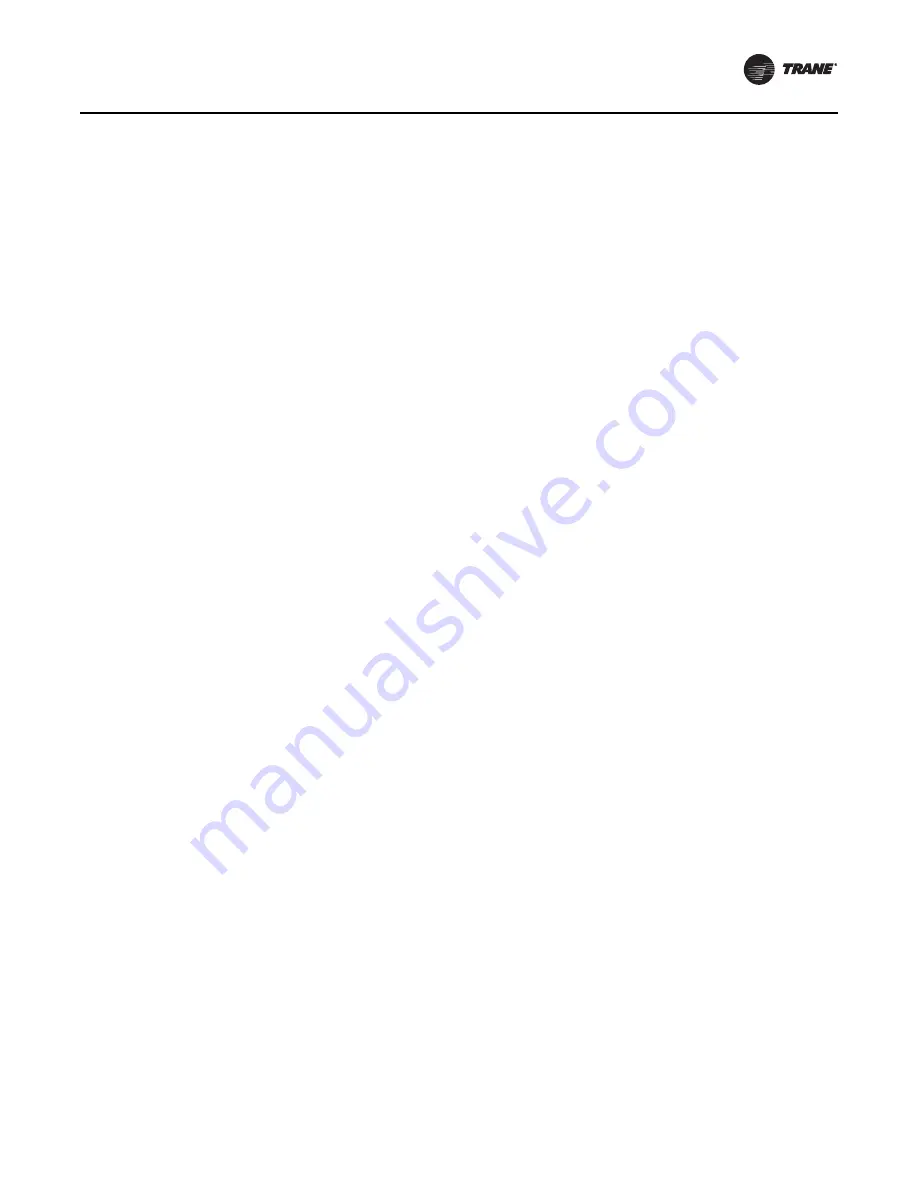
Startup
UNT-SVX07E-EN
117
Note:
The supply fan speed source can be configured for
BAS, local, or default value control using the Tracer
TU service tool.
AUTO Fan Operation; 1-, 2-, 3-speed Fans
When the controller receives a communicated auto signal
(or the associated fan speed switch is set to
AUTO
with no
communicated value present), the fan operates in the
AUTO
mode. In
AUTO
mode, the fan operates according
to the fan default (configurable using the Tracer TU service
tool). The fan speed has multiple speed configurations
(default is
AUTO
) or set to
OFF
for both heating and
cooling operation. When configured as
AUTO
(and with
multiple speeds available), the fan changes based on the
required capacity calculated by the control algorithm.
AUTO Fan Operation; ECM Energy Efficient
Mode
When the controller is configured for Energy Efficient
Mode, by means of the Fan Operating Mode Request MV
point, the controller and daughter board will minimize
energy use by running the fan at the lowest possible speed
while maintaining space temperature. The controller will
fully utilize valves, economizer, or electric heat which
increases fan speed to meet space temperature (unless the
fan has been manually controlled. Refer to the preceding
section,
“Manual Fan Speed Control”
).
AUTO Fan Operation; ECM Acoustical Mode
When the controller is configured for Acoustical Mode, by
means of the Fan Operating Mode Request MV point, the
controller and daughter board will minimize acoustical
nuisance by balancing changes in fan speed and total fan
noise. The controller will fully
OPEN
cooling and heating
valves before increasing fan speed to meet space
temperature (unless the fan has been manually controlled.
Refer to the preceding section,
“Manual Fan Speed
Control”
). If multiple stages of electric heat exist the
controller will use a single minimum air flow for each
stage.
Exhaust Control
Exhaust control is achieved by a single-speed exhaust fan
and controlled by binary output 2 (BO2). Exhaust control,
if not present, can be enabled by selecting
Yes
under the
Exhaust Fan Selection on the Tracer TU Configuration
page under the Equipment Options group.
Note:
Exhaust fan configuration cannot be selected with
3-speed fan operation.
Important:
If exhaust control is added to an existing
configuration, all other configuration
options should be verified to match the
correct equipment options.Temperature
and flow setpoints will revert to default
values.
The exhaust function is coordinated with the supply fan
and outdoor/return air dampers as follows:
•
The exhaust fan energizes when the fan is running and
when the outdoor air damper position is greater than
or equal to the exhaust fan enable position (or the
outside air damper position at which the exhaust fan
turns
ON
).
•
The exhaust fan turns
OFF
when the fan either turns
OFF
or the outdoor air damper closes to 10 percent
below the exhaust fan enable position.
•
If the exhaust fan/damper enable setpoint is less than
10 percent, the exhaust output is energized if the
outdoor air damper position is at the setpoint and de-
energized at 0.
Valve Operation
The controller supports one or two modulating or two-
position valves, depending on the application (refer
Table 59, p. 118
). The controller opens and closes the
appropriate valve(s) to maintain the active zone
temperature setpoint at the heating setpoint in heating
mode or the cooling setpoint in cooling mode (refer to
“Cascade Zone Control,”
p. 115
).
Three-Wire Modulating Valve Operation
The controller supports tri-state 3-wire modulating valve
control. Two binary outputs control each valve: one to
drive the valve open and one to drive the valve closed. The
stroke time for each valve is configurable using the Tracer
TU service tool. The controller supports the following:
•
Heating
•
Cooling
•
Heat/cool changeover with a single valve and coil for 2-
pipe applications
•
Cooling or heat, cool changeover with the main valve,
and coil
•
Only heating with the auxiliary valve and coil for 4-pipe
applications
The controller moves the modulating valve to the desired
positions based on heating or cooling requirements.
Three-Wire Modulating Valve Calibration
Modulating valve calibration is automatic. During normal
controller operation, the controller overdrives the actuator
(135 percent of the stroke time) whenever there is a
request for a position of 0 percent or 100 percent. At either
power-up, after a power outage, or when the occupancy
status changes to unoccupied, the controller first drives all
modulating valves (and dampers) to the closed position.
The controller calibrates to the fully
CLOSED
position by
over driving the actuator (135 percent of the stroke time).
Thereafter, the controller resumes normal operation.
Two-position Valve Operation
The controller supports two-position valves with a single
binary output for each valve. Controllers used for 2-pipe
applications support heating, cooling, or heat/cool
changeover with a single valve/coil. A controller used for