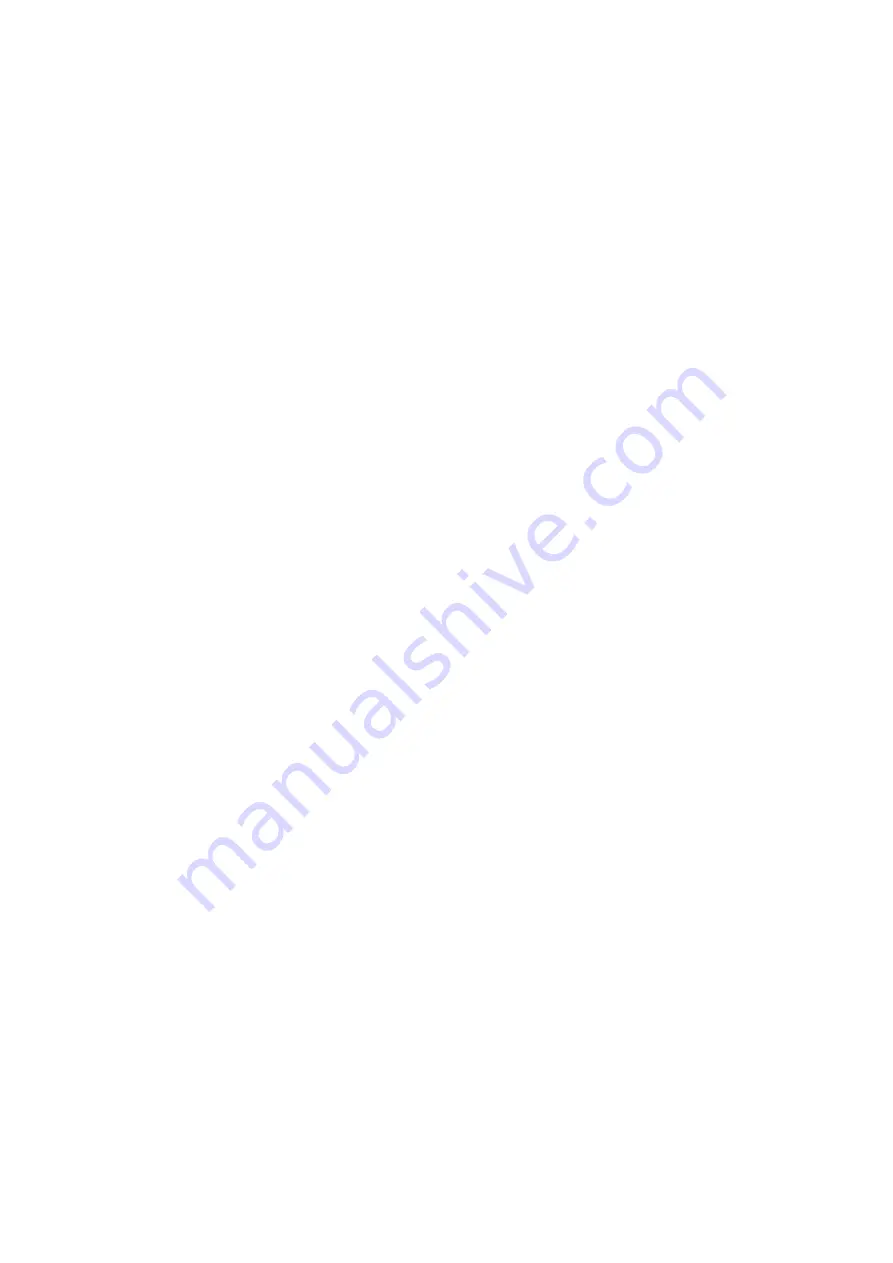
Engine Maintenance
9-27
4. Remove the rocker arm cover.
5. Place the engine at top dead center of the compression stroke for the number one cylinder.
e. Rotate the engine in the normal direction of rotation (clockwise viewed from the water pump end) until the 1-4 timing mark
on the flywheel lines up with the index mark in the timing mark access hole.
f. Check the rocker arms on the number one cylinder to see if they are loose.
g.If the rocker arms are loose, the engine is at top dead center of the compression stroke for the number one cylinder.
h.If the rocker arms are tight, the engine is at top dead center of the exhaust stroke for the number one cylinder. Rotate the
engine 360 degrees to place the engine at top dead center of the compression stroke for the number one cylinder.
6. Energise the fuel solenoid:
a. Disconnect the 8S wire from the starter solenoid to prevent the Cycle-Sentry system from cranking the engine. Then place
the On-Off switch in the ON position.
NOTE: Disconnect the 8S wire from the starter solenoid to prevent the engine from cranking. Otherwise, units with
Cycle-Sentry or MT µP-IV, µP-V, µP-VI, SR-2 and SR-3 controllers may start at any time when the unit On/Off switch is ON.
b.If the engine is not in the unit, use jumper wires to energise the fuel solenoid at the three pin fuel solenoid connector. Place
a jumper between the black wire (CH wire, pin C) and the negative terminal of a 12 Vdc power source. Place a jumper
between the red wire (8D wire, pin A) and the positive terminal of a 12 Vdc power source. Then momentarily place a jumper
between the white wire (8DP wire, pin B) and the positive terminal of a 12 Vdc power source.
CAUTION: Do not leave the jumper on the white wire (8DP wire, pin B) more than a few seconds or the fuel solenoid will be
damaged.
7. Rotate the engine backwards (counter clockwise viewed from the water pump end) until the injection timing mark is
positioned in the bottom of the timing mark access hole. The injection timing mark is a horizontal line stamped on the flywheel
approximately 30 mm (1.2 in.) before the top dead center mark.
8. Pump the priming pump by hand a few times, or energise the electric fuel pump if an electric fuel is being used.
9. Use a clean towel to remove the fuel from the top end of the delivery valve holder.
10. Slowly turn the engine in the normal direction of rotation until you see the fuel rise in the end of the delivery valve holder.
Stop as soon as you see the fuel rise.
11. Check position of the timing marks. The injection timing mark on the flywheel should be aligned with the index mark on the
side of the timing mark access hole. Repeat steps 8 and 12 to recheck the timing.
12. If the timing is off by more than 1 degree (2.5 mm), loosen the mounting nuts on the studs that fasten the injection pump to
the engine and rotate the injection pump to change the timing.
a. Pull the top of the injection pump away from the engine to advance the timing.
b.Push the top of the injection pump toward the engine to retard the timing.
13. Tighten the injection pump mounting nuts and recheck the timing. Repeat steps 8 through 14 until the timing is correct.
14. Install the cover in the timing mark access hole, install the injection line for the number one cylinder, install the rocker arm
cover, and tighten the other injection lines when finished with the procedure.
Injection Pump Timing (TK 486V Engine)
Use this timing procedure when installing a new injection pump on TK 486V engine. It is not necessaery to use this procedure
when removing or reinstalling the original injection pump. In that case, align the index marks on the injection pump and the gear
case as they were before removing the injection pump.
1. Before removing old injection pump, note the alignment of the index marks on the injection pump and the gear case. The
index mark on the injection pump is usually aligned with the indexmark on the gear case. If not, make a mark on gear case in
line with the index mark on the injection pump.
Summary of Contents for SLXi Spectrum
Page 17: ...Safety Precautions 2 5 Warning Decals...
Page 18: ...Safety Precautions 2 6 Warning Decals Information Decals...
Page 74: ...Unit Description 5 30...
Page 128: ...Controller Operation 7 28...
Page 156: ...Electrical Maintenance 8 28...
Page 234: ...Refrigeration Maintenance 10 22...
Page 309: ...13 Mechanical Diagnosis TK 482 TK 486 and TK 486V Engines 13 2...
Page 316: ...Mechanical Diagnosis 13 8...
Page 322: ...Refrigeration System Diagnosis 14 6...
Page 332: ...Single Temperature Refrigeration System Diagrams 15 10...
Page 339: ...Multi Temperature Refrigeration System Diagrams 16 7...
Page 340: ...Multi Temperature Refrigeration System Diagrams 16 8...