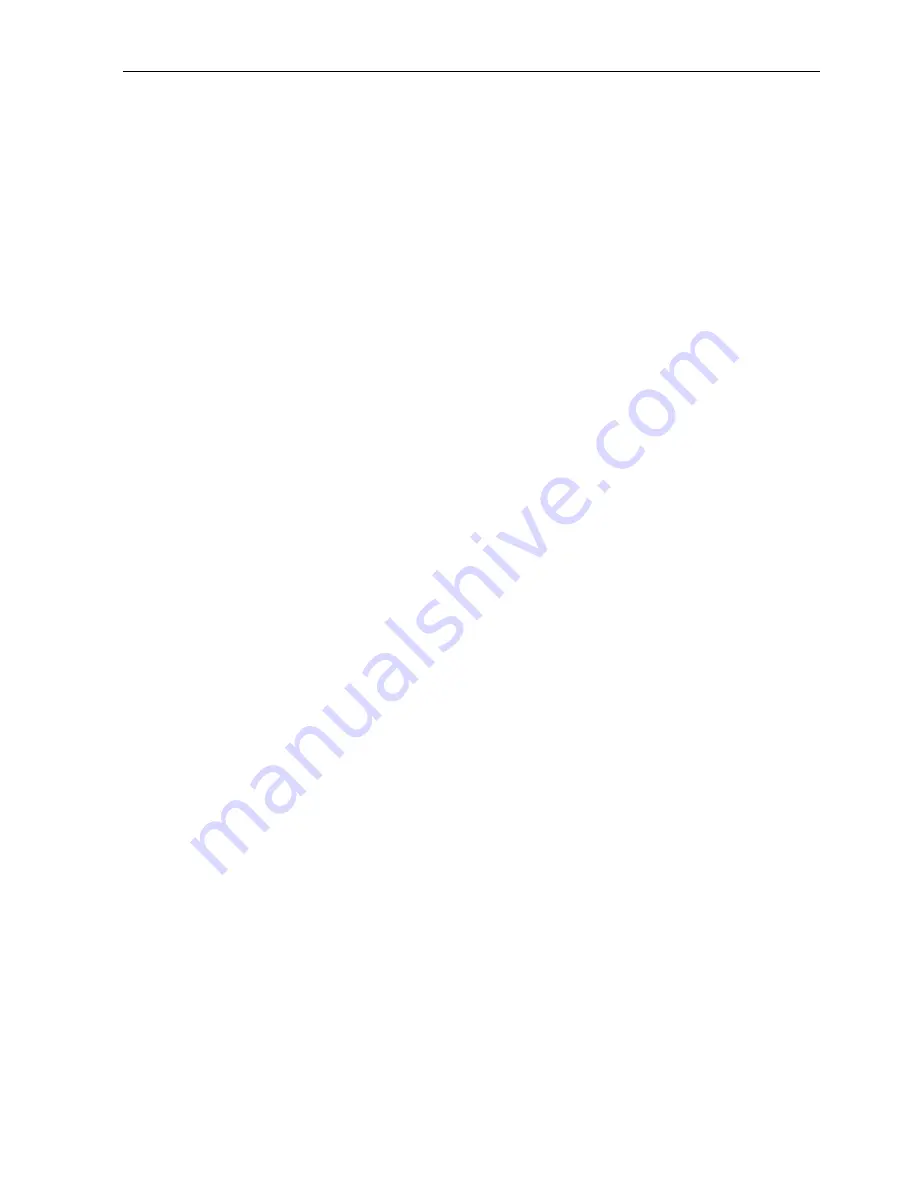
Engine Maintenance
87
a. Pull the top of the injection pump away
from the engine to advance the timing.
b. Push the top of the injection pump toward
the engine to retard the timing.
17. Tighten the injection pump mounting nuts and
recheck the timing. Repeat steps 10 through
17 until the timing is correct.
18. Install the cover in the timing mark access
hole, install the injection line for the number
one cylinder, install the rocker arm cover,
tighten the other injection lines and reconnect
the 8S wire to the starter solenoid when
finished with the procedure.
Injection Pump Removal
The injection pump drive gear will not fit through
the gear housing when removing the pump, the
gear must be separated from the pump. Using tool
P/N 204-1011, it will not be necessary to remove
the belts, fuel pump, crankshaft pulley, crankshaft
seal or front plate. See Figure 76 “Injection Pump
Gear Tool” on page 88.
1. Remove the starter for clearance, remove
throttle linkage, fuel lines, harness and
mounting hardware from injection pump.
2. Remove the cover plate from the gear case.
Remove the nut and lock washer which secure
the gear to the injection pump shaft. Use a
shop rag to prevent the lock washer or nut
from falling into the gear case.
3. Use the hardware from the cover plate to
attach the tool plate (with the marked side
pointing up and out) to the gear case.
4. Align the threaded holes in the injection pump
gear with the two holes in the tool plate by
rotating the engine crankshaft. Attach the gear
to the tool plate with the screws provided with
the tool plate.
5. Thread the long screw supplied with the tool
plate into the small end of the adapter, also
supplied with the tool plate. Insert the adapter
into the tool plate and rotate to provide a solid
position to force the injection pump shaft from
the gear. Caution should be made to align the
screw over the center of the injection pump
shaft.
6. Remove the screw and adapter leaving the tool
plate in place. This holds the gear in proper
tooth alignment until the injection pump is
re-installed.
Injection Pump Reinstallation
1. Position injection pump shaft into gear,
rotating shaft to mate key with keyway in
gear.
2. Secure injection pump to gear case with
previously removed hardware.
3. Remove hardware holding gear to tool plate,
then remove tool plate.
4. Secure gear to injection pump shaft with lock
washer and nut, use a shop rag, as before, to
prevent the lock washer or nut from falling
into the gear case. Torque the nut to 84 to 90
ft-lb (113 to 122 N•m)
5. Fasten cover plate to gear case and reinstall all
components removed previously to facilitate
injection pump removal.
Summary of Contents for SB-210
Page 4: ...4 ...
Page 12: ...List of Figures 12 ...
Page 31: ...Unit Description 31 Unit Photos Figure 6 Front View AJA1617 ...
Page 36: ...Unit Description 36 ...
Page 49: ...Operating Instructions 49 Figure 32 Viewing Sensors Screen Sequence ...
Page 54: ...Operating Instructions 54 Figure 40 Datalogger Screen Sequence ...
Page 101: ...Engine Maintenance 101 ...
Page 102: ...Engine Maintenance 102 ...
Page 140: ...Electric Standby Diagnosis 140 ...
Page 150: ...Index 150 ...
Page 152: ...Wiring Diagram Index 152 ...
Page 153: ...153 Model 30 and 50 Schematic Diagram Page 1 of 3 ...
Page 154: ...154 Model 30 and 50 Schematic Diagram Page 2 of 3 ...
Page 155: ...155 Model 30 and 50 Schematic Diagram Page 3of 3 ...
Page 156: ...156 Model 30 and 50 Wiring Diagram Page 1 of 4 ...
Page 157: ...157 Model 30 and 50 Wiring Diagram Page 2 of 4 ...
Page 158: ...158 Model 30 and 50 Wiring Diagram Page 3 of 4 ...
Page 159: ...159 Model 30 and 50 Wiring Diagram Page 4 of 4 ...