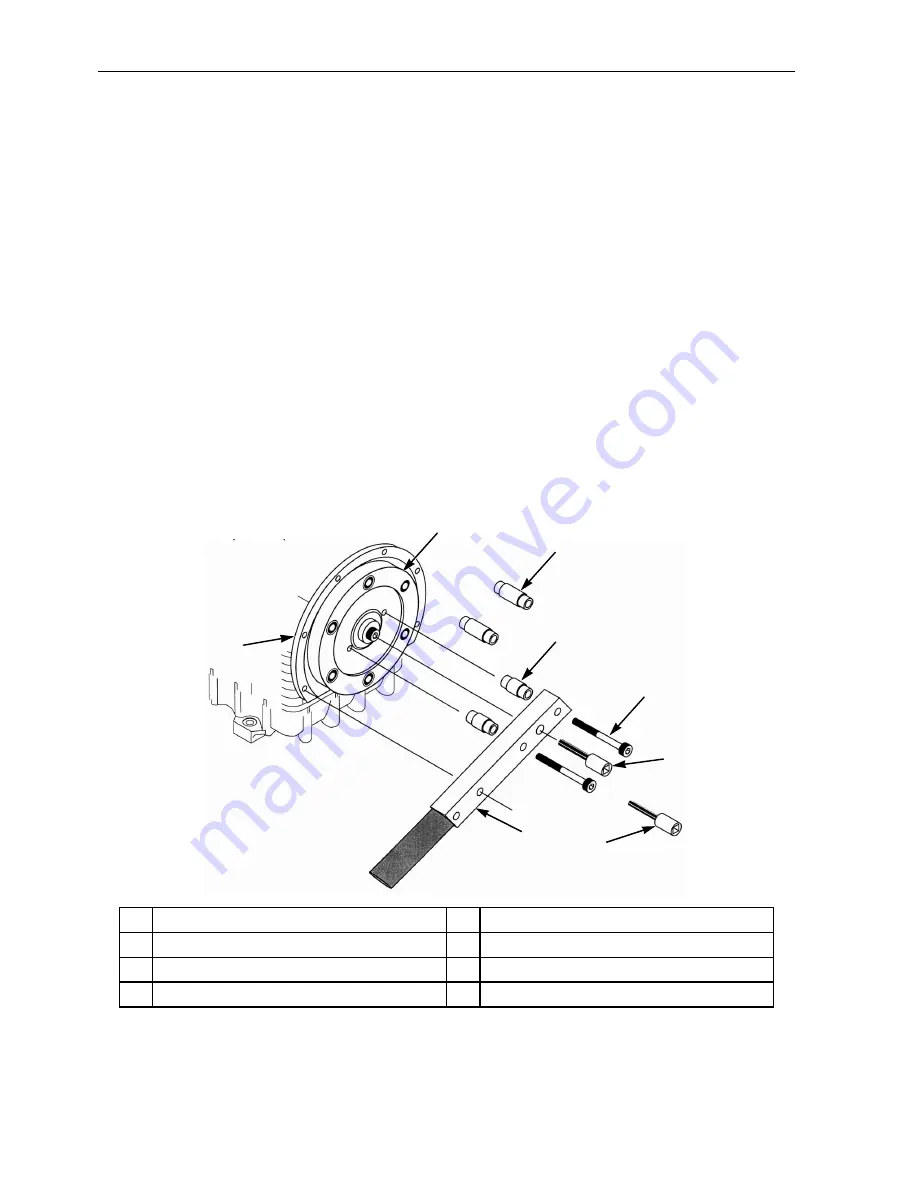
Refrigeration Service Operations
110
4. Use the appropriate Allen tool to loosen the
coupling mounting screw.
5. Once the center screw has been loosened,
back the head against the tool and it should
push the coupling off the crankshaft as you
continuing turning the center screw in a
counter-clockwise direction. Using this tool
will prevent the coupling from popping off
because the center bolt and flatwasher will
hold it in place.
Compressor Coupling Installation
(Model 30)
In a tapered fit joint the entire twisting load
should be handled by the friction fit between the
two tapered parts. The key is only a backup and is
used to index the parts correctly. When a taper fit
is machined and assembled properly a key is not
needed. In fact, if the key is not installed correctly
it may be worse than no key at all! If the key does
not fit easily into the keyway, it will push the
tapered components apart and the reduced friction
could lead to slippage and premature failure.
The following procedure requires the key to be
fitted after the tapers are pulled together with
20 ft-lb (27 N•m) torque. This insures that the key
cannot hold the tapers apart when the final bolt
torque is applied.
Use the following procedure to install a
compressor coupling on the compressor
crankshaft.
1. Clean the compressor shaft taper and coupling
bore taper with a solvent that leaves no oily
residue (such as naphtha, lacquer thinner,
brake cleaner or the like).
2. Inspect both mating surfaces for burrs,
oxidation and other surface imperfections.
Dress with crocus cloth if necessary and
re-clean as required.
AGA1059
1
3
4
8
5
6
7
2
1.
Coupling
5.
10 mm Allen Tool (for large shaft compressor)
2.
Long Spacers (supplied with tool)
6.
5/16 Allen Tool (for small shaft compressors)
3.
Short Spacers (supplied with tool)
7.
Coupling Removal Tool (P/N 204-991)
4.
Socket Head Bolts (supplied with tool)
8.
Engine Mounting Flange
Figure 95: Compressor Coupling Removal Tool
Summary of Contents for SB-210
Page 4: ...4 ...
Page 12: ...List of Figures 12 ...
Page 31: ...Unit Description 31 Unit Photos Figure 6 Front View AJA1617 ...
Page 36: ...Unit Description 36 ...
Page 49: ...Operating Instructions 49 Figure 32 Viewing Sensors Screen Sequence ...
Page 54: ...Operating Instructions 54 Figure 40 Datalogger Screen Sequence ...
Page 101: ...Engine Maintenance 101 ...
Page 102: ...Engine Maintenance 102 ...
Page 140: ...Electric Standby Diagnosis 140 ...
Page 150: ...Index 150 ...
Page 152: ...Wiring Diagram Index 152 ...
Page 153: ...153 Model 30 and 50 Schematic Diagram Page 1 of 3 ...
Page 154: ...154 Model 30 and 50 Schematic Diagram Page 2 of 3 ...
Page 155: ...155 Model 30 and 50 Schematic Diagram Page 3of 3 ...
Page 156: ...156 Model 30 and 50 Wiring Diagram Page 1 of 4 ...
Page 157: ...157 Model 30 and 50 Wiring Diagram Page 2 of 4 ...
Page 158: ...158 Model 30 and 50 Wiring Diagram Page 3 of 4 ...
Page 159: ...159 Model 30 and 50 Wiring Diagram Page 4 of 4 ...