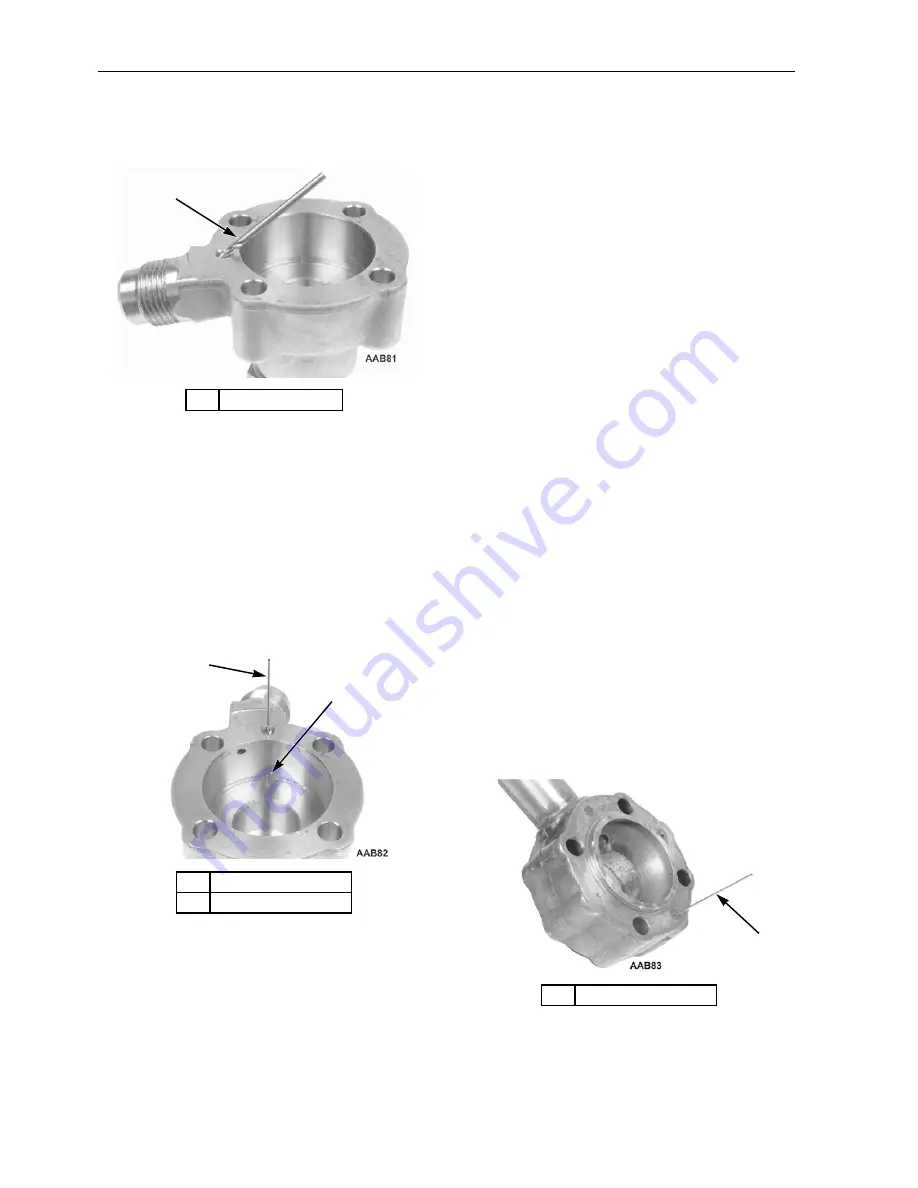
Refrigeration Service Operations
118
4. Deburr the hole in the check valve piston bore.
A used drill bit can be modified to use as a
deburring tool.
Piston Bleed Orifice Check
1. Use a number 66 (0.033 in. [0.84 mm]) drill
bit to check the orifice in the bleed hole from
the gasket surface to the groove in the bottom
of the piston bore.
2. Carefully check to see that the drill projects
down into the groove and that there are no
burrs at the end of the hole in the groove. Do
not enlarge this hole.
Check Valve Piston Check
1. Reassemble the end cap using a new check
valve piston, spring, stem, and snap ring (Kit
P/N 60-163).
2. Leave the stem back seated against the snap
ring. Use a paper clip bent into a 90 degree
angle to push the check valve piston back in
its bore. Make sure you can feel the piston
working against the spring.
3. With the piston pushed all the way back in its
bore, use a strong light to look down the
0.089 in. (2.26 mm) hole towards the back of
the piston and determine how much of the end
of the hole is covered by the piston. If the
piston covers more than three-quarters of the
hole replace the end cap.
NOTE: When front seating a condenser bypass
check valve DO NOT over-tighten the stem!
Excessive torque will deform the piston and the
deformed piston can increase the hole blockage.
Seat (Center Section) Orifice Check
There are three 0.033 in. (0.84 mm) holes located
in the three-way valve seat (center section). Only
one is used depending on how the valve is config-
ured. If the hole is too large the valve will be slow
to shift from heat to cool when the condenser
pressure is higher than discharge pressure because
gas will flow to the discharge line instead of
behind the piston. If the hole is too small the valve
will be slow to shift from heat to cool when dis-
charge pressure is higher than condenser pressure
because the flow is restricted. Do not enlarge this
hole larger than 0.033 in. (0.84 mm)! Whenever
you disassemble a three-way valve you should
check that all three of the holes are drilled cleanly.
1.
Number 43 Drill
Figure 103: Check Bleed Hole Diameter
1.
Number 66 Drill
2.
Check for Burr Here
Figure 104: Check Piston Bleed Orifice
1
1
2
1.
Number 66 Drill
Figure 105: Check Seat Orifice
1
Summary of Contents for SB-210
Page 4: ...4 ...
Page 12: ...List of Figures 12 ...
Page 31: ...Unit Description 31 Unit Photos Figure 6 Front View AJA1617 ...
Page 36: ...Unit Description 36 ...
Page 49: ...Operating Instructions 49 Figure 32 Viewing Sensors Screen Sequence ...
Page 54: ...Operating Instructions 54 Figure 40 Datalogger Screen Sequence ...
Page 101: ...Engine Maintenance 101 ...
Page 102: ...Engine Maintenance 102 ...
Page 140: ...Electric Standby Diagnosis 140 ...
Page 150: ...Index 150 ...
Page 152: ...Wiring Diagram Index 152 ...
Page 153: ...153 Model 30 and 50 Schematic Diagram Page 1 of 3 ...
Page 154: ...154 Model 30 and 50 Schematic Diagram Page 2 of 3 ...
Page 155: ...155 Model 30 and 50 Schematic Diagram Page 3of 3 ...
Page 156: ...156 Model 30 and 50 Wiring Diagram Page 1 of 4 ...
Page 157: ...157 Model 30 and 50 Wiring Diagram Page 2 of 4 ...
Page 158: ...158 Model 30 and 50 Wiring Diagram Page 3 of 4 ...
Page 159: ...159 Model 30 and 50 Wiring Diagram Page 4 of 4 ...