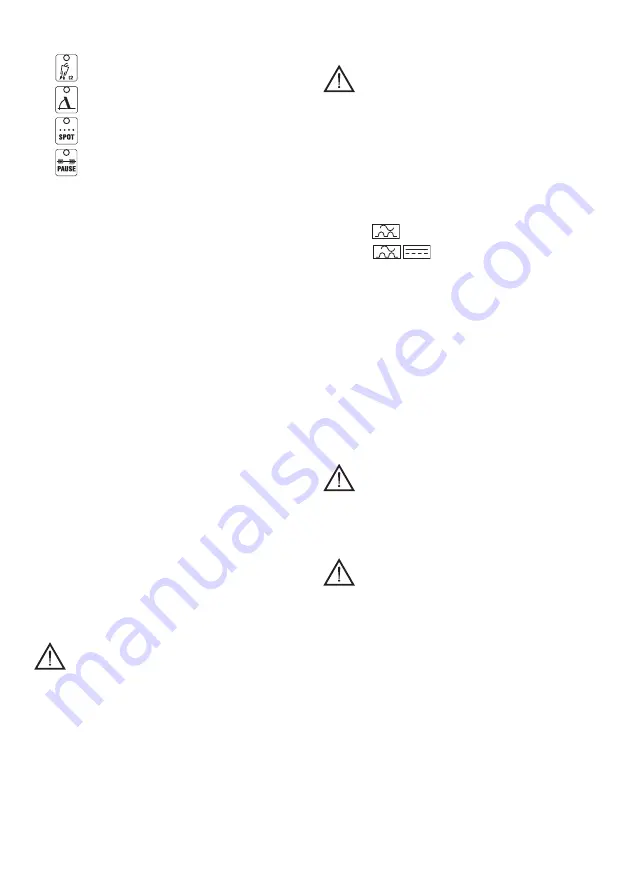
- 8 -
output current zeroes, available only in manual mode (key
(13)
disabled).
14f-
parameter 6: Postgas.
In MIG/MAG/FLUX it adjusts the
postgas time in seconds.
14g-
parameter 7: Downslope.
In
MIG/MAG it is the time of
the downslope, available only in synergy (key
(13)
enabled).
14h-
parameter 8: Spot time.
In MIG/MAG/FLUX it adjusts
the duration time of the spot welding current.
14i-
Parameter 9: MIG/MAG/FLUX spot pause time;
it
adjusts the duration of the pause between one spot
welding and the next. With the setting at 0 sec., release
the torch button and press it again to carry out the next spot
weld.
STORING AND RECALLING CUSTOMISED MIG/MAG
PROGRAMS
Introduction
The welding machine can be used to (STORE) customised work
programs relating to a set of valid parameters for a particular welding
job. Each stored program can be recalled (LOAD) at any time so
that the user finds the welding machine “ready-to-use” for a specific
job that has been optimised previously. It is possible to store 10
customised programmes in the welding machine.
Storage procedure (STORE)
After adjusting the welding machine for optimal operation with a given
type of weld proceed as follows
(FIG.C)
:
a) Press button
(7)
“STORE” for 3 seconds.
b) “
St_
”will appear on the display
(4)
with a number between 1 and
10.
c) Turn the knob
(5)
to choose the desired programme number for
storage.
d) Press key
(7)
again “STORE”:
- if the STORE key is pressed for more than 3 seconds, the
program has been stored correctly. “
YES
” appears on the
display;
- if the STORE key is pressed for less than 3 seconds, the
program has not been stored. “
no
” appears on the display.
Loading procedure (LOAD)
Proceed as follows
(
see
FIG.C)
:
a) Press button
(6)
“LOAD” for 3 seconds.
b) “
Ld_
”will appear on the display
(4)
with a number between 1
and 10.
c) Turn the knob
(5)
to choose the number used to store the
programme that is now to be used.
d) Press key
(6)
“LOAD” again:
- if the LOAD key is pressed for more than 3 seconds, the
program has been loaded correctly. “
YES
” appears on the
display;
- if the LOAD key is pressed for less than 3 seconds, the
program has not been loaded. “
no
” appears on the display.
NOTE:
during operations with the “store” and “load” keys the prg.
5. INSTALLATION
WARNING! CARRY OUT ALL INSTALLATION
OPERATIONS AND ELECTRICAL CONNECTIONS WITH THE
WELDING MACHINE COMPLETELY SWITCHED OFF AND
DISCONNECTED FROM THE POWER SUPPLY OUTLET.
THE ELECTRICAL CONNECTIONS MUST BE MADE ONLY AND
EXCLUSIVELY BY AUTHORISED OR QUALIFIED PERSONNEL.
Assembling the protective mask
Fig. D
Assembling the return cable-clamp
Fig. E
Assembling the welding cable-electrode holder clamp
Fig. F
POSITION OF THE WELDING MACHINE
Locate the welding machine in an area where openings for cooling air
are not obstructed (forced circulation with fan), leave at least 250mm
free space around the welding machine
; check that conductive dusts,
corrosive vapours, humidity etc., will not enter welding machine.
WARNING: Position the welding machine on a flat
surface with sufficient carrying capacity for the weight of the
welding machine, to prevent tipping or hazardous movement.
CONNECTION TO THE MAIN POWER SUPPLY
Warning
- Before making any electrical connection, make sure the rating
data of the welding machine correspond to the mains voltage and
frequency available at the place of installation..
- The welding machine should only be connected to a power supply
system with the neutral conductor connected to earth.
- To ensure protection against indirect contact use residual current
devices of the following types:
- Type A (
) for single phase machines;
- Type B (
) for 3-phase machines.
- To comply with the requirements of the EN 61000-3-11 (Flicker)
standard we recommend connecting the welding machine to
interface points of the power supply that have an impedance of
less than Zmax =0.18 ohm.
- The welding machine does not fall within the requisites of IEC/EN
61000-3-12 standard.
Should it be connected to a public mains system, it is the installer’s
responsibility to verify that the welding machine itself is suitable
for connecting to it (if necessary, consult the distribution network
company).
PLUG AND OUTLET
Connect a normalised plug
(2P + T)
having sufficient capacity- to
the power cable and prepare a mains outlet fitted with fuses or an
automatic circuit-breaker; the special earth terminal should be
connected to the earth conductor (yellow-green) of the power supply
line. Table 1
(TAB. 1)
shows the recommended delayed fuse sizes in
amps, chosen according to the max. nominal current supplied by the
welding machine, and the nominal voltage of the main power supply.
WARNING!
Failure to observe the above rules will make the (Class 1)
safety system installed by the manufacturer ineffective with
consequent serious risks to persons (e.g. electric shock) and
objects (e.g. fire).
CONNECTION OF THE WELDING CABLES
WARNING! BEFORE MAKING THE FOLLOWING
CONNECTIONS MAKE SURE THE WELDING MACHINE IS
SWITCHED OFF AND DISCONNECTED FROM THE POWER
SUPPLY OUTLET.
Table 1
(TAB. 1)
gives the recommended values for the welding
cables (in mm
2
) depending on the maximum current supplied by the
welding machine.
MIG/MAG WELDING
Connection to the gas bottle
- The gas bottle can be loaded onto the supporting platform of the
trolley
max. 60 kg
.
- Screw the pressure reducing valve onto the gas bottle valve,
inserting the appropriate adapter supplied as an accessory, for
when the gas used is Argon or an
Argon /CO
2
mixture.
- Connect the gas inlet pipe to the pressure-reducing valve and
tighten the band supplied.
- Loosen the adjustment ring nut on the pressure-reducing valve
before opening the bottle valve.
Connecting the welding current return cable
Connect the welding current return cable to the piece to be welded
or to the metal bench on which it rests, as close as possible to the
join being made.
Summary of Contents for Technomig 200
Page 192: ... 192 Ø0 8 8 0 Ø 200mm Ø 300mm 1 a b 2 a b c 3 a b 4 FIG G Ø0 6 0 6 ...
Page 196: ... 196 ...