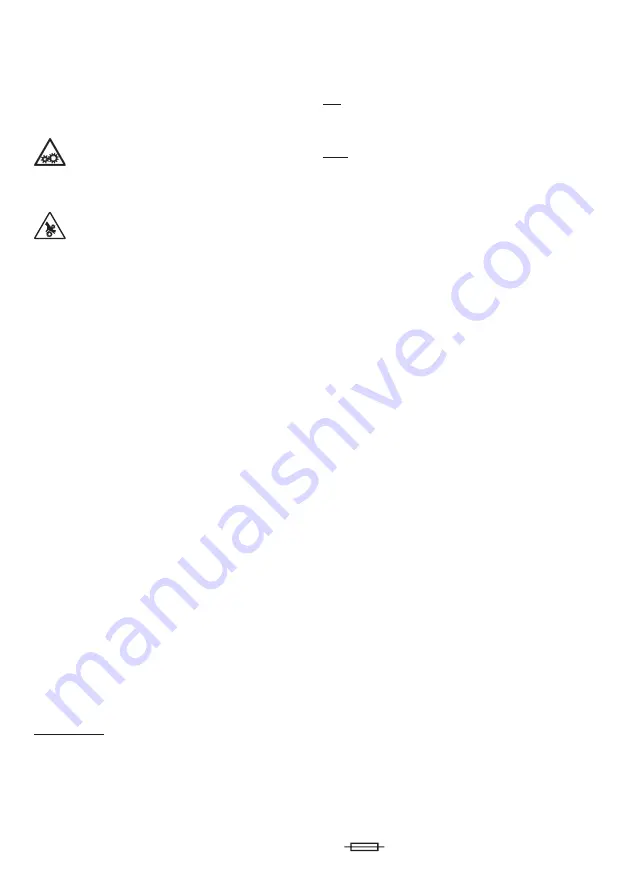
- 6 -
surface that is able to support the weight: otherwise (e.g.
inclined or uneven floors etc.) there is danger of overturning.
- IMPROPER USE: it is hazardous to use the welding machine
for any work other than that for which it was designed (e.g.
de-icing mains water pipes).
- MOVING THE WELDING MACHINE: always secure the gas
bottle, taking suitable precautions so that it cannot fall
accidentally.
The safety guards and moving parts of the covering of the
welding machine and of the wire feeder should be in their proper
positions before connecting the welding machine to the power
supply.
WARNING! Any manual operation carried out on the moving
parts of the wire feeder, for example:
- Replacing rollers and/or the wire guide;
- Inserting wire in the rollers;
- Loading the wire reel;
- Cleaning the rollers, the gears and the area underneath them
- Lubricating the gears
SHOULD BE CARRIED OUT WITH THE WELDING MACHINE
SWITCHED OFF AND DISCONNECTED FROM THE POWER
SUPPLY OUTLET.
2. INTRODUCTION AND GENERAL DESCRIPTION INTRODUCTION
These single phase welding machines are power sources based
on state-of-the-art IGBT inverter technology with completely digital
control, and are equipped with an integrated wire feeder.
The welding machines can be used for high quality welding in
continuous synergic MIG/MAG, TIG and MMA and in pulsed synergic
MIG/MAG when included.
The wire feeder is equipped with a 2-roller motorised wire puller unit
with independent adjustment of pulling pressure. The digital control
panel is integrated with the microprocessor adjustment board and it
contains fundamentally three condensed functions:
a) PARAMETER SETTINGS AND ADJUSTMENTS
With this user interface it is possible to set and adjust the
operating parameters, select previously stored programs, view
parameter status and values on the display.
b) RECALLING PRE-STORED SYNERGIC PROGRAMS FOR
MIG-MAG WELDING
These programs are pre-defined and stored by the manufacturer
(so cannot be modified); when the user recalls one of these
programs, he can select a specific job point (corresponding to
a set of various independent welding parameters), adjusting
a single magnitude. With this
SYNERGY
concept, it is very
easy to obtain the ideal adjustment for the welding machine
according to each individual operating condition.
c) STORING/RECALLING CUSTOMISED PROGRAMS
This function is available when working within a synergic
program and also when in manual mode (in this case the
setting for all the welding parameters is at the discretion of the
operator). This mode of operation allows the user to store and
later recall a specific welding procedure.
This welding machine is designed for use with the SPOOL GUN
torch, used for welding aluminium and steel when the power source
and piece to be welded are far apart.
METAL WELDABILITY
MIG/MAG-FLUX:
The welding machine is suitable for MIG welding
of aluminium and its alloys, MIG brazing is typically carried out
on galvanised plate and MAG welding on carbon, low alloy and
stainless steels. It is also possible to weld Flux with tubular wire,
without protective gas (self-shielding) by adjusting the torch polarity
according to the instructions given by the wire manufacturer.
MIG welding of aluminium and its alloys should be carried out using
flux core wire with a composition that is compatible with the material
being welded and pure Ar (99.9%) protective gas.
MIG brazing can be carried out, typically, on galvanised plate
using flux core wire in copper alloy (e.g. copper silicon or copper
aluminium) with pure Ar (99.9%) protective gas.
MAG welding of carbon and low alloy steel should be carried out
using flux core or tubular wire with a composition that is compatible
with the material being welded and CO
2
and Ar/CO
2
or Ar/CO
2
/O
2
mixtures as the protective gas (Ar-Argon normally > 80%).
For welding stainless steel Ar/O
2
or Ar/CO
2
gas mixtures are normally
used (Ar normally> 98%).
TIG:
The welding machine is suitable for TIG welding in direct current
(DC) with Lift arc strike, and is suitable for use with all steels (carbon,
low and high alloys) and heavy metals (copper, nickel, titanium and
their alloys) with pure Ar (99.9%) protective gas or, for particular
operations, using Argon/Helium mixtures.
MMA:
The welding machine is suitable for MMA electrode welding in
direct current (DC) with all types of coated electrodes.
MAIN FEATURES:
- Power supply voltage monitor.
- Spot, 2/4-stroke operation.
- Automatic torch recognition.
- Regulation of wire slope up, post-gas time, wire burn-back time.
- Memorizzazione/Richiamo di programmi personalizzati.
- Ready for use with SPOOL GUN torch.
- Thermostatic protection.
- Inversione della polarità (Saldatura FLUX)
OPTIONAL ACCESSORIES
- Adapter for ARGON IT bottle.
- Trolley
- Manual remote control 1 pot.
- Manual remote control 2 pot.
- Connecting cables kit.
- Aluminium welding kit.
- Tubular wire welding kit.
- Welding kit MMA.
- Welding kit TIG DC.
- MIG torch.
- TIG torch.
3. TECHNICAL DATA
DATA PLATE
The most important data regarding use and performance of the
welding machine are summarised on the rating plate and have the
following meaning:
Fig. A
1-
EUROPEAN standard of reference, for safety and construction
of arc welding machines.
2-
Symbol for internal structure of the welding machine.
3-
Symbol for welding procedure provided.
4-
Symbol
S
: indicates that welding operations may be carried out
in environments with heightened risk of electric shock (e.g. very
close to large metallic volumes).
5-
Symbol for power supply line:
1~ : single phase alternating voltage
3~ : 3-phase alternating voltage
6-
Protection rating of the covering.
7-
Technical specifications for power supply line:
- U
1
: Alternating voltage and power supply frequency of
welding machine (allowed limit ±10%):
- I
1 max
: Maximum current absorbed by the line.
- I
1eff
: effective current supplied
8-
Performance of the welding circuit:
- U
0
: maximum no-load voltage (open welding circuit).
- I
2
/U
2
: current and corresponding normalised voltage that the
welding machine can supply during welding
- X
: Duty cycle: indicates the time for which the welding
machine can supply the corresponding current (same
column). It is expressed as %, based on a 10 min. cycle (e.g.
60% = 6 minutes working, 4 minutes pause, and so on)
.
If the usage factors (on the plate, referring to a 40°C
environment) are exceeded, the thermal safeguard will
trigger (the welding machine will remain in standby until its
temperature returns within the allowed limits).
- A/V-A/V
: shows the range of adjustment for the welding
current (minimum maximum) at the corresponding arc
voltage.
9-
Manufacturer’s serial number for welding machine identification
(indispensable for technical assistance, requesting spare parts,
discovering product origin).
10-
:
Size of delayed action fuses to be used to protect
Summary of Contents for Technomig 200
Page 192: ... 192 Ø0 8 8 0 Ø 200mm Ø 300mm 1 a b 2 a b c 3 a b 4 FIG G Ø0 6 0 6 ...
Page 196: ... 196 ...