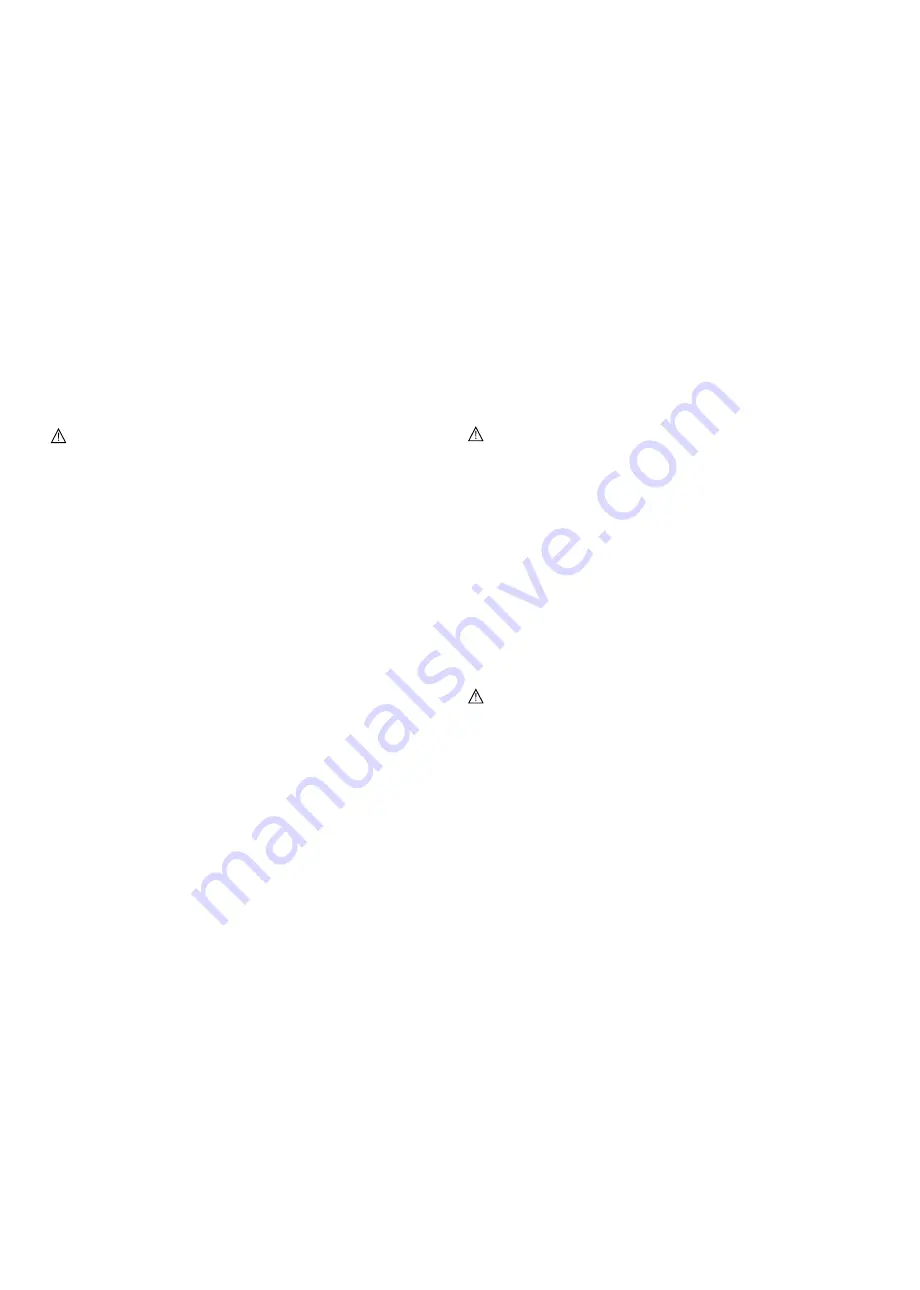
welder correspond to the mains voltage and frequency available at the place of
-
excessive voltage drops on the power line;
-
spot-welder overheating due to insufficient cooling or non-observance of the duty
installation.
cycle;
The spot-welder should only and exclusively be connected to a power supply system
-
shape and size of workpiece between the arms;
with the neutral conductor connected to earth.
-
gap between the arms (adjustable in PTE - PCP 28 models);
-
length of arms (see technical data).
5.4.2 Connecting the power supply cable to the spot-welder (FIG.F)
Failing precise knowledge, you should run some spot welding tests using sheets having
Remove the right side panel, assemble the supplied cable clip at the hole drilled on the
the same quality and thickness as the job to be performed.
back panel.
Whenever possible, use high currents (adjust using the ”POWER” potentiometer from
Pass the power supply cable through the cable clip and connect it to the power supply
20% to 100% of spot-welder capacity) and short periods (adjust using the ”CYCLES”
block (phases L1(N) L2) and to the screw terminal of the yellow-green earth protection
potentiometer from 1 to 100).
conductor.
Depending on the terminal block model, fit the cable terminals as shown in the diagram
6.3 PROCEDURE
-
Close the general switch (position ”
I
”); the green LED lights up; power OK, spot-
(FIG.F1, F2).
welder ready.
Block the cable by tightening the screws on the cable guide.
-
PCP MODEL: press ”start-up”
push-button and turn the cycle selector
See the “TECHNICAL DATA” paragraph for the minimum allowed section of the
(
$
to welding position.
conductors.
-
Place the sheets to be welded on the lower electrode.
-
Press on the pedal at end-of-stroke (PTE models) or on the pedal valve (PCP
5.4.3 Plug and socket
models) to achieve:
Connect the power supply cable to a standardised plug (
3P+T : only two pins are used:
A) closing of the sheets between the electrodes with the preset force,
INTERPHASE CONNECTION!)
of adequate capacity and prepare a power outlet
B) passage of the welding current for a preset period (time) and at a preset
protected by fuses or by an automatic circuit-breaker; the appropriate earth terminal
intensity, indicated by the green LED
switching on and off.
should be connected to the earth conductor (yellow-green) of the power line.
%
-
Shortly (0.5-2 sec.) after the green LED switches off (end of welding operation)
The capacity and specifications of the fuses and circuit-breaker are given in the
release the pedal. This delay (holding) improves the mechanical characteristics of
paragraph on “TECHNICAL DATA”.
the spot weld.
Should several spot welders be installed, distribute the power cyclically among the three
The spot welding operation is deemed correct when, after having run a tensile
phases in order to obtain a more balanced load; e.g.:
strength test, the spot welding core comes out from one of the two sheets.
spot-welder 1: power supply L1-L2;
spot-welder 2: power supply L2-L3;
spot-welder 3: power supply L3-L1.
7. MAINTENANCE
_____________________________________________________________________________________________________________________
_____________________________________________________________________________________________________________________
WARNING! BEFORE CARRYING OUT ANY MAINTENANCE OPERATION
WARNING! Failure to observe the rules given above will invalidate the (class
MAKE SURE THE SPOT-WELDER HAS BEEN SWITCHED OFF AND
I) safety system provided by the manufacturer causing serious risks to people
DISCONNECTED FROM THE MAIN POWER SUPPLY.
(e.g. electric shock) and objects (e.g. fire).
_____________________________________________________________________________________________________________________
In the versions driven by pneumatic cylinder (PCP models) it is necessary to lock
the main switch in the “O” position with the supplied padlock.
5.5 PNEUMATIC CONNECTION (FIG. G )
_____________________________________________________________________________________________________________________
(PCP models only)
- Set up a compressed air line with working pressure of at least 6 bar.
7.1 ROUTINE MAINTENANCE
- Screw the pressure GAUGE (supplied with the spot-welder) into the special threaded
ROUTINE MAINTENANCE CAN BE CARRIED OUT BY THE OPERATOR
hole located on the pressure reducing valve.
-
adjustment/reset of electrode tip diameter and profile;
- electrode alignment checks;
-
electrode and arm cooling checks
(NOT INSIDE THE SPOT-WELDER)
;
- checking the spring load (electrode force);
5.6 CONNECTING THE COOLING CIRCUIT (FIG.H)
It is necessary to set up a water delivery pipe for maximum temperature 30 °C, with
7.2 EXTRAORDINARY MAINTENANCE
minimum flow rate not less than that specified in TECHNICAL DATA. It is possible to set
EXTRAORDINARY MAINTENANCE OPERATIONS SHOULD BE CARRIED OUT
up an open cooling circuit (discarding the return water) or a closed circuit as long as the
ONLY AND EXCLUSIVELY BY SKILLED, AUTHORISED ELECTRICAL-
temperature and water flow rate parameters are respected.
MECHANICAL TECHNICIANS.
Remove the left side panel in order to reach the flexible delivery and return water pipes
and then pass them through the special openings located on the rear panel. Connect the
_____________________________________________________________________________________________________________________
delivery pipe (marked by a label) to the external water supply, ensuring correct
discharge and flow rate in the return pipe.
WARNING! BEFORE REMOVING THE SPOT-WELDER PANELS AND WORKING
INSIDE THE SPOT-WELDER MAKE SURE THE MACHINE IS SWITCHED OFF AND
WARNING!
Welding operations performed without or with insufficient water flow could
DISCONNECTED FROM THE MAIN POWER SUPPLY OUTLET.
cause the spot-welder to break down due to overheating.
_____________________________________________________________________________________________________________________
If checks are made inside the spot-welder while it is live, this may cause serious
6. SPOT WELDING
electric shock due to direct contact with live parts and/or injury due to direct
6.1 PRELIMINARY OPERATIONS
contact with moving parts.
Before carrying out any spot-welding operation it is necessary to make a series of
Depending on how often the spot-welder is run and on the environment conditions,
checks and adjustments, which should be carried out with the general switch in the “O”
make regular checks inside the machine and remove the dust and the metallic
position (with the padlock closed in PCP versions) and with the compressed air supply
particles deposited on the transformer, the thyristor module, the terminal box, etc., by
switched off (DISCONNECTED).
means of dry compressed air (5 bar maximum).
- Ensure that the electric connection is done according to the previous instructions.
Do not direct the compressed air jet on the electronic boards:
clean them using a
- Put the cooling water into circulation.
very soft brush or with appropriate solvents.
- Adjust diameter ”d” of the electrode contact surface according to the thickness ”s” of
- ensure that the wiring insulation is not damaged and the connections are tight and
the sheet to be spot welded, according to relationship
d = 4 ÷ 6 ·
Ö
s.
free of oxidation.
- Between the electrodes slide a shim equivalent to the thickness of the sheet to be
- ensure that the transformer secondary connection screws to the arm holder castings
spot welded; ensure that the arms, brought together manually, are parallel and that
are tightly secured and that there are no signs of oxidation or overheating; make the
the electrode holders are centred.
same checks on the arm-locking and electrode holder screws.
If necessary, make some adjustments by loosening the electrode holder locking
- lubricate all joints and pins.
screws until you find the most suitable position for the job to be performed; secure the
- ensure correct cooling water flow (minimum flow required) and perfect pipe seals.
locking screws tightly.
- check for any air leakages (PCP models).
In models PTE and PCP28, the gap between the arms can also be regulated by
- if necessary reduce the approach speed of the electrodes, regulate the throttling at the
adjusting the fastening screws of the lower armholder casting (see technical data).
pneumatic cylinder release by adjusting the appropriate screws on the cylinder heads.
- Open the safety gate located on the rear of the spot-welder by loosening the four
fastening screws to get at the electrode force adjustment nut (wrench No.30).
IF THE SPOT-WELDER DOES NOT RUN PROPERLY AND BEFORE PERFORMING A
Compressing the spring (screw the nut clockwise) will cause the electrodes to exert
THOROUGH MACHINE CHECK OR GETTING IN TOUCH WITH THE AFTER SALES
gradually increasing force with values between the minimum and the maximum (see
SERVICE CENTER, CHECK WHETHER:
technical data).
- with the spot-welder general switch closed (position ”
I
”), the green LED
is on; if
Such force will increase in proportion to the increase in the thickness of the sheets to
*
be welded and to the diameter of the electrode tip.
this is not the case, check for failures in the power supply line (cables, outlets, plugs,
- Close the gate to prevent extraneous matter from entering and to prevent accidental
fuses, excessive drop in voltage, etc.)
contact with live or moving parts.
- Check the compressed air connection in PCP models, connect the feed pipe to the
- the yellow LED is on
(thermal safeguard); wait until the LED goes off before re-
pneumatic system, adjust the pressure by turning the reducer knob until the gauge
&
starting the spot-welder (PCP models, push-button
); ensure correct cooling
reads 6 bar (90 PSI).
water flow and, if necessary, reduce duty cycle.
(
- with the pedal or the cylinder activated, the electric control actuator has indeed closed
6.2 ADJUSTING THE PARAMETERS
The parameters determining the diameter (section) and the mechanical resistance of
the terminals (contacts) giving the OK to the electronic board: green LED
on for
%
spot welding are:
the preset time.
- force exerted by the electrodes (daN); 1 daN = 1.02 Kg.
- the elements making up the secondary circuit (arm holder castings - arms - electrode
-
diameter of the electrode contact surface (mm);
holders) are inefficient due to loose screws or oxidation.
-
welding current (kA);
- welding parameters (electrode force and diameter, time and welding current) are
-
welding time (cycles): at 50Hz 1 cycle = 0.02 sec.
suitable for the job to be performed.
In summary, all the above factors must be taken into consideration in adjusting the spot-
In PCP models check also whether:
welder given that they interact between each other with relatively ample margins.
- the compressed air pressure is lower than the triggering limit of the safeguard device;
Furthermore, other factors that could modify the results should not be neglected. These
are:
- the cycle selector is erroneously in position
(pressure only - spot-welder does not
#
- Connect a flexible pipe for compressed air (internal diameter 8-9) through the special
opening located on the rear of the machine to the lubricator-reducer-filter group
connector located on the left side; seal off with suitable hose clamps. Pour ISO FD22
oil into the lubricator cup through the special cap (screw).
- drain the condensate collected inside the filter cup and tap up the oil level (ISO FD22)
in the compressed air entrance lubricator (PCP models).
- 7 -