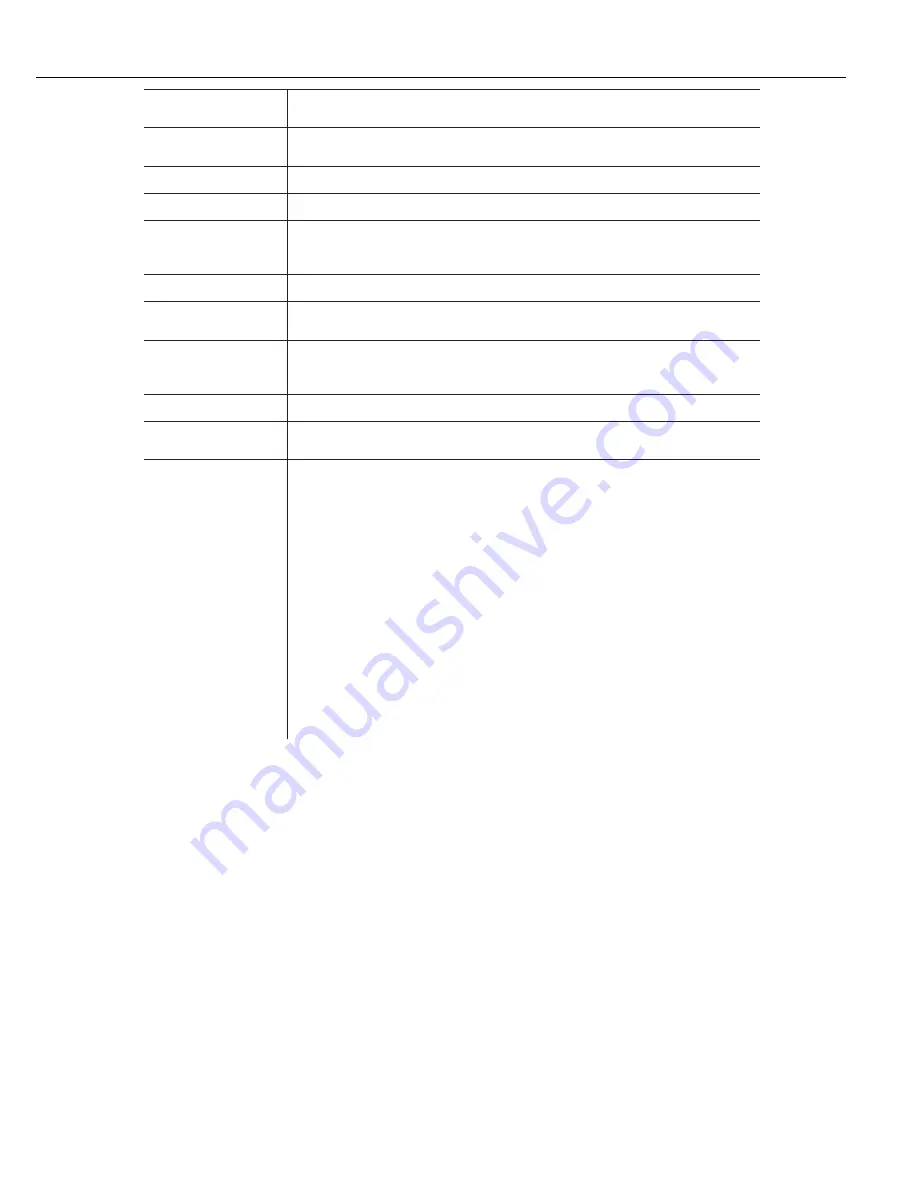
Glossary
Instruction Manual
201
Speed
The speed at which the tool operates during the initial portion of the Fastening cycle
prior to ATC or downshift.
Spindle
A spindle represents a connection to a hand held or fixtured tool connected to a
controller.
Strategy
Identifies what variables will be used to control the tool during a Fastening cycle.
Thread Direction
Sets assembly direction to clockwise (CW) or counter clockwise (CCW).
Threshold Torque
Sets the point at which the tool is "In Cycle". When the tool is "In Cycle" the tool and
controller Fastening cycle status lights turn off, the controller displays dashes (-) for data,
and the "In Cycle" output is turned on.
Tool Tones
Distinctive sounds assigned to tool functions.
Torque Calibration
Determines how torque values are assigned to the electrical signals from the torque
transducer on the tool. This value is unique to each tool and changes over time.
Torque Target
When the tool is being controlled for torque, the torque target instructs the controller
when to shutoff the tool. The torque target should be greater than Low Torque and less
than High Torque, and is required for torque control.
Trace
A display plot of torque vs time (or angle) of a Fastening cycle.
Trip Counter
Records the number of Fastening cycles completed since the last time it was reset. It is
usually used as a supplementary count of the PM Counter.
Units
The following torque units and associated labels are used with STANLEY controllers and
tools. The labels are derived from SP811, SI Unit rules and style conventions from the
National Institute of Standards and Technology
Abbreviation
Common Term
= 1 lbfft
= 1 Nm
Nm
Newton meter
1.355 818
1
Ncm
Newton centimeter
135.581 8
100
kgm
Kilogram meter
0.138 255 2
0.101 971 6
kgcm
Kilogram centimeter
13.825 52
10.197 16
ft lb
Foot pound
1
0.737 562 1
in lb
Inch pound
12
8.850 745
in oz
inch ounce
192
141.611 9
Summary of Contents for QB Expert
Page 8: ......
Page 23: ...Introduction Instruction Manual 15 ...
Page 24: ......
Page 36: ......
Page 37: ...3 QB Expert Alpha Controller Programming SETUP Area SERVICE Area ANALYZE Area ...
Page 94: ......
Page 109: ...Instruction Manual 101 ...
Page 110: ......
Page 123: ...Instruction Manual 115 Tool Operation ...
Page 124: ......
Page 132: ...Input and Output Connector QB Expert Alpha Controller 124 Inputs example ...
Page 133: ...Controller Connections Instruction Manual 125 Outputs Sourcing example ...
Page 157: ...Controller Connections Instruction Manual 149 ...
Page 158: ...MODBUS TCP QB Expert Alpha Controller 150 ...
Page 175: ...Embedded PLC Instruction Manual 167 ...
Page 176: ......
Page 183: ...Multiple Spindle Instruction Manual 175 ...
Page 184: ... QB Expert Alpha Controller 176 ...
Page 201: ...Instruction Manual 193 Maintenance ...
Page 202: ...QB Expert Alpha Controller 194 ...
Page 203: ...10 QB Expert Alpha Controller Appendix A Torsion Compensation Angle Validation ...
Page 206: ......
Page 207: ...11 QB Expert Alpha Controller Glossary ...
Page 210: ......