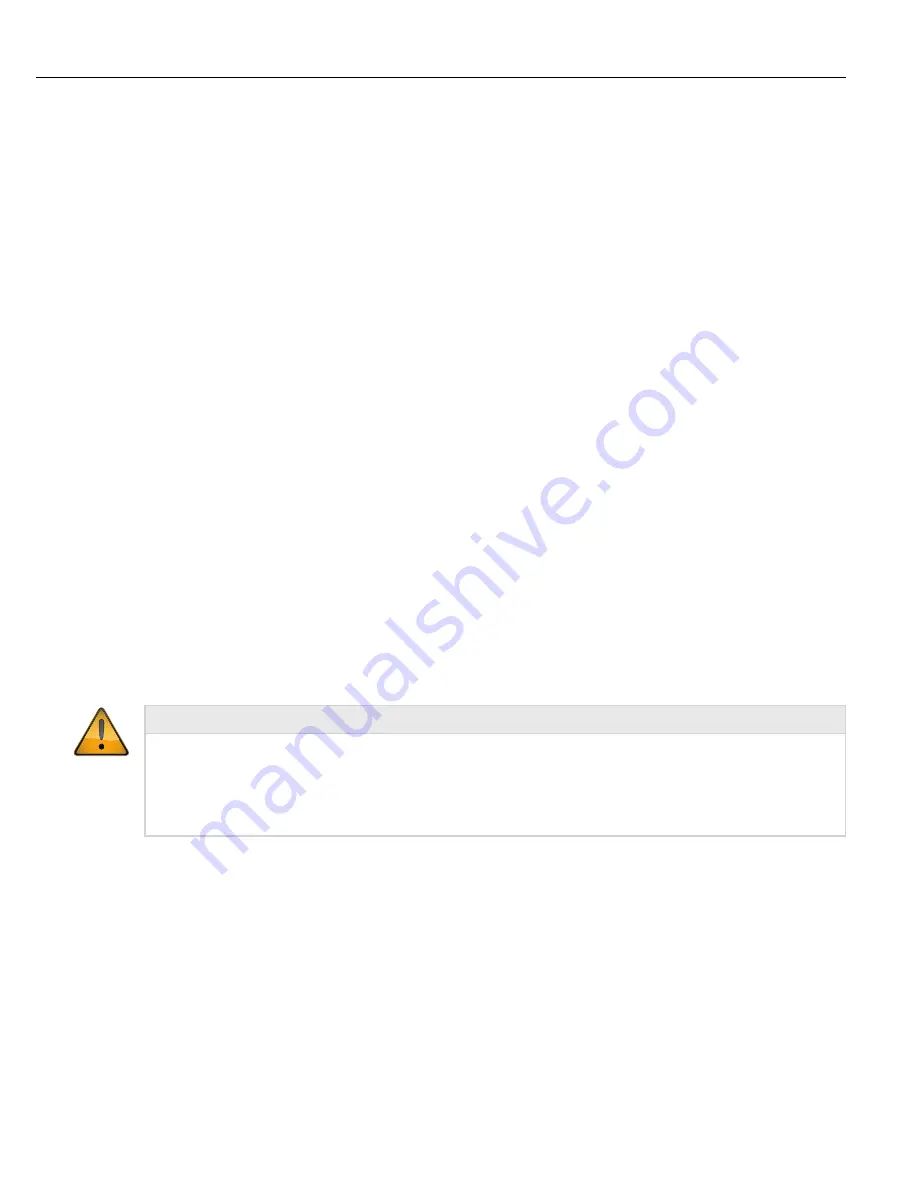
Multiple Spindle
Instruction Manual
173
To synchronize the Alpha controllers simply assign a START input on the lead controller and configure the Spindle
number as ALL.
8.3.1 Operation
The fixtured tools must be started with a remote start switch connected to the START input of the lead Alpha. The
lead controller will apply a start to the synchronized trailing spindles in the system.
When the remote start switch is depressed all tools will start. All tools will run the first step in the selected Job/
Task. Once each tool has completed the first step it will stop and wait for all tools to finish the step. If all tools
finished the step OK then all tools start the next step in the multi-step strategy. This process continues until all
steps are complete or any tool times out or is stopped or aborted.
All multi-step rules still apply in that the tool must meet the programmed OK window to move on to the next
step. If a tool fails a step it will stop which causes all other tools to stop immediately. Once they stop the In-Cycle
indicator on the run screen will go away and a SYNC shutoff code is indicated for all controllers except the one
that failed to complete a step OK. All tools will be stopped immediately if any single tool is stopped due to an
abort event.
When in synchronization mode any Reverse, Job Select, Task Select or PartID input from any of the synchronized
spindles will cause all spindles to react to the input.
All spindles are required to maintain the same number of accumulated bolt count. If one spindle has a bolt count
different from the other the controllers will not run from the START:ALL input. Individual spindles must be ran in
recovery operations to get all spindles on the same bolt count to continue or reset the Job to recover.
8.3.2 Recovery
In certain stations the system is allowed to retry fastening cycles or to perform a recovery operation. The logic for
these recovery operations can become very complex especially if Error Proofing is enabled and the user wishes to
maintain equal bolt counts on the controllers.
It is important to understand that the START: ALL input cannot be used to start individual spindles for forward or
reverse operations if a spindle is disabled through the STOP command. Individual Starts, Stops and Reverses must
be applied to the spindles required to run in recovery operations.
8.4 Networking
WARNING
NETWORK INTERRUPTION
To Avoid Issues:
• Never connect an Alpha Toolbox port to a plant network.
• Never connect the SPINDLE port to a plant network.
The lead controller in a multiple spindle system can communicate to a plant network via the embedded protocols,
see section “3.1.3 COMMUNICATIONS Menu” on page 48. The lead controller will collect and transmit the
fastening cycle data after each fastening cycle from each controller in the system via the selected protocol.
Connecting the multiple spindle lead Expert controller to a facility network using the ETHERNET port. Use
customer’s supplied values and enter the IP Address, Subnet Mask and Gateway into the lead Expert controller.
Summary of Contents for QB Expert
Page 8: ......
Page 23: ...Introduction Instruction Manual 15 ...
Page 24: ......
Page 36: ......
Page 37: ...3 QB Expert Alpha Controller Programming SETUP Area SERVICE Area ANALYZE Area ...
Page 94: ......
Page 109: ...Instruction Manual 101 ...
Page 110: ......
Page 123: ...Instruction Manual 115 Tool Operation ...
Page 124: ......
Page 132: ...Input and Output Connector QB Expert Alpha Controller 124 Inputs example ...
Page 133: ...Controller Connections Instruction Manual 125 Outputs Sourcing example ...
Page 157: ...Controller Connections Instruction Manual 149 ...
Page 158: ...MODBUS TCP QB Expert Alpha Controller 150 ...
Page 175: ...Embedded PLC Instruction Manual 167 ...
Page 176: ......
Page 183: ...Multiple Spindle Instruction Manual 175 ...
Page 184: ... QB Expert Alpha Controller 176 ...
Page 201: ...Instruction Manual 193 Maintenance ...
Page 202: ...QB Expert Alpha Controller 194 ...
Page 203: ...10 QB Expert Alpha Controller Appendix A Torsion Compensation Angle Validation ...
Page 206: ......
Page 207: ...11 QB Expert Alpha Controller Glossary ...
Page 210: ......