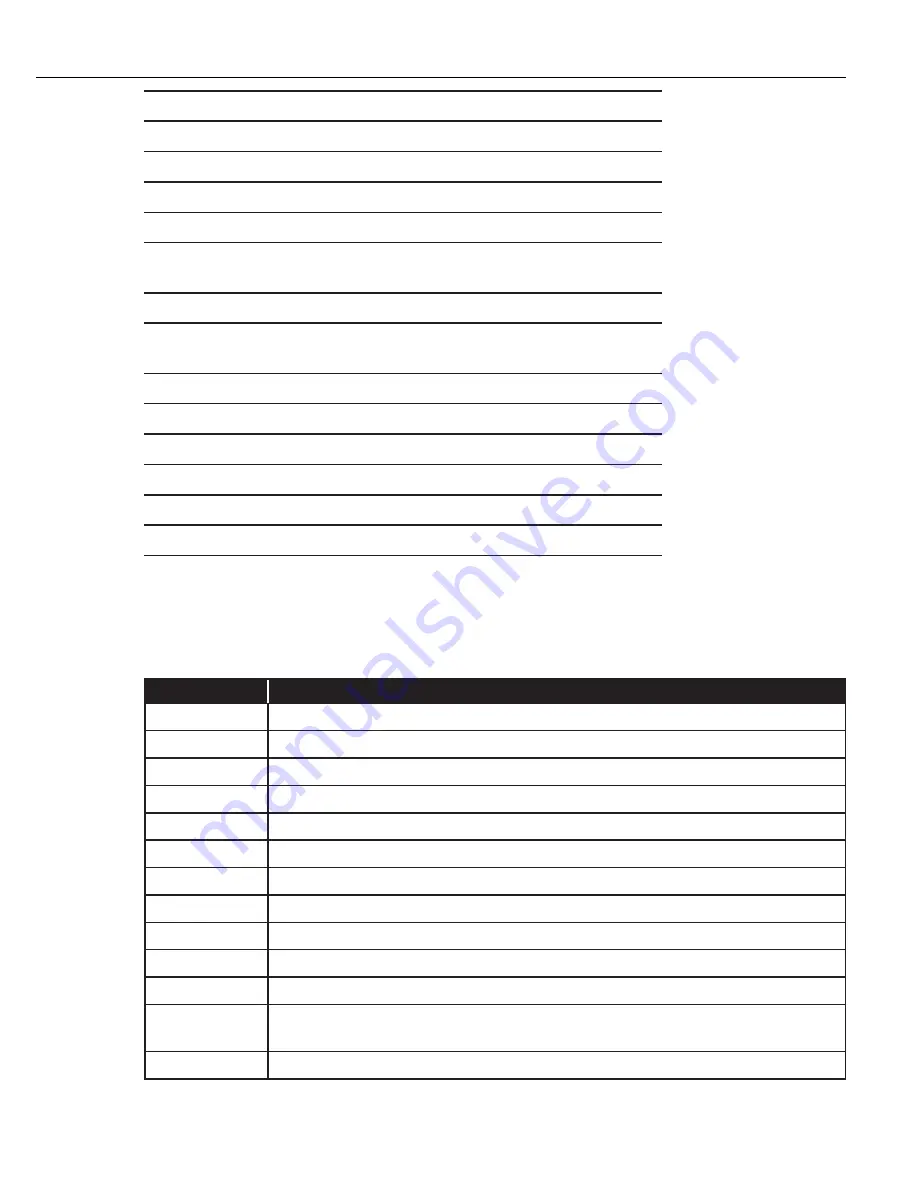
Controller Operation
Instruction Manual
23
SOC:
Shutoff Code, see section “2.7.7.2 Shutoff Codes” on page 23
Job Count:
The active fastener number for the Job.
Task Count:
The active fastener number for the Task.
Tool Model:
The model number of the tool used during this fastening cycle.
Tool Serial:
The serial number of the tool used during this fastening cycle.
Tool
Temperature:
The temperature of the tool at shutoff.
Part ID:
The value in the Part ID buffer when the fastening cycle ran.
Steps:
List the steps used during the fastening cycle. The Audit step
values are in
Bold
.
TC/AM
The Strategy or Smart Step used in the current step.
Torque:
The Torque value achieved in the current step.
Angle
The Angle value achieved in the current step.
Current
The Current value achieved in the current step.
Rate
The Rate value achieved in the current step (if enabled)
Deviation
The Rate Deviation achieved in the current step (if enabled)
Use the up/down arrows to scroll through the Details.
Press the interactive BACK button to return to the Fastening Cycle Log.
2.7.7.2
Shutoff Codes
Shutoff Codes on the display indicate why a fastening cycle terminates prior to completion.
Shutoff Code
Description
TIME
Fastening cycle time exceeds programmed Cycle Abort time value.
STOP
Spindle stopped by either the operator or other device.
>115%
Spindle stopped due to torque achieving greater than 115% torque limit for the tool.
FAULT
The tool shutoff due to a Fault. See section “2.8 Faults” on page 25.
STALL
Spindle stopped due to a stall.
SYNC
Spindle failed fastening cycle due to a synchronization error.
T1≠T2
Primary and secondary redundant transducer values are outside comparative limits.
A1≠A2
Primary and secondary redundant angle values are outside comparative limits.
TD
Spindle stopped due to torque dropping below Torque Drop Threshold
YIELD
Spindle stopped due to bailout on detecting yield during an Angle Control strategy.
[T]
A torque/angle window violation for the Torque Monitoring portion of the fastening cycle.
RATE
Torque Rate has exceeded the High Limit or not achieved the Low Limit during a Rate
Monitoring portion of the fastening cycle.
I
Current has exceeded the High Current Limit or not achieved the Low Current Limit.
Summary of Contents for QB Expert
Page 8: ......
Page 23: ...Introduction Instruction Manual 15 ...
Page 24: ......
Page 36: ......
Page 37: ...3 QB Expert Alpha Controller Programming SETUP Area SERVICE Area ANALYZE Area ...
Page 94: ......
Page 109: ...Instruction Manual 101 ...
Page 110: ......
Page 123: ...Instruction Manual 115 Tool Operation ...
Page 124: ......
Page 132: ...Input and Output Connector QB Expert Alpha Controller 124 Inputs example ...
Page 133: ...Controller Connections Instruction Manual 125 Outputs Sourcing example ...
Page 157: ...Controller Connections Instruction Manual 149 ...
Page 158: ...MODBUS TCP QB Expert Alpha Controller 150 ...
Page 175: ...Embedded PLC Instruction Manual 167 ...
Page 176: ......
Page 183: ...Multiple Spindle Instruction Manual 175 ...
Page 184: ... QB Expert Alpha Controller 176 ...
Page 201: ...Instruction Manual 193 Maintenance ...
Page 202: ...QB Expert Alpha Controller 194 ...
Page 203: ...10 QB Expert Alpha Controller Appendix A Torsion Compensation Angle Validation ...
Page 206: ......
Page 207: ...11 QB Expert Alpha Controller Glossary ...
Page 210: ......