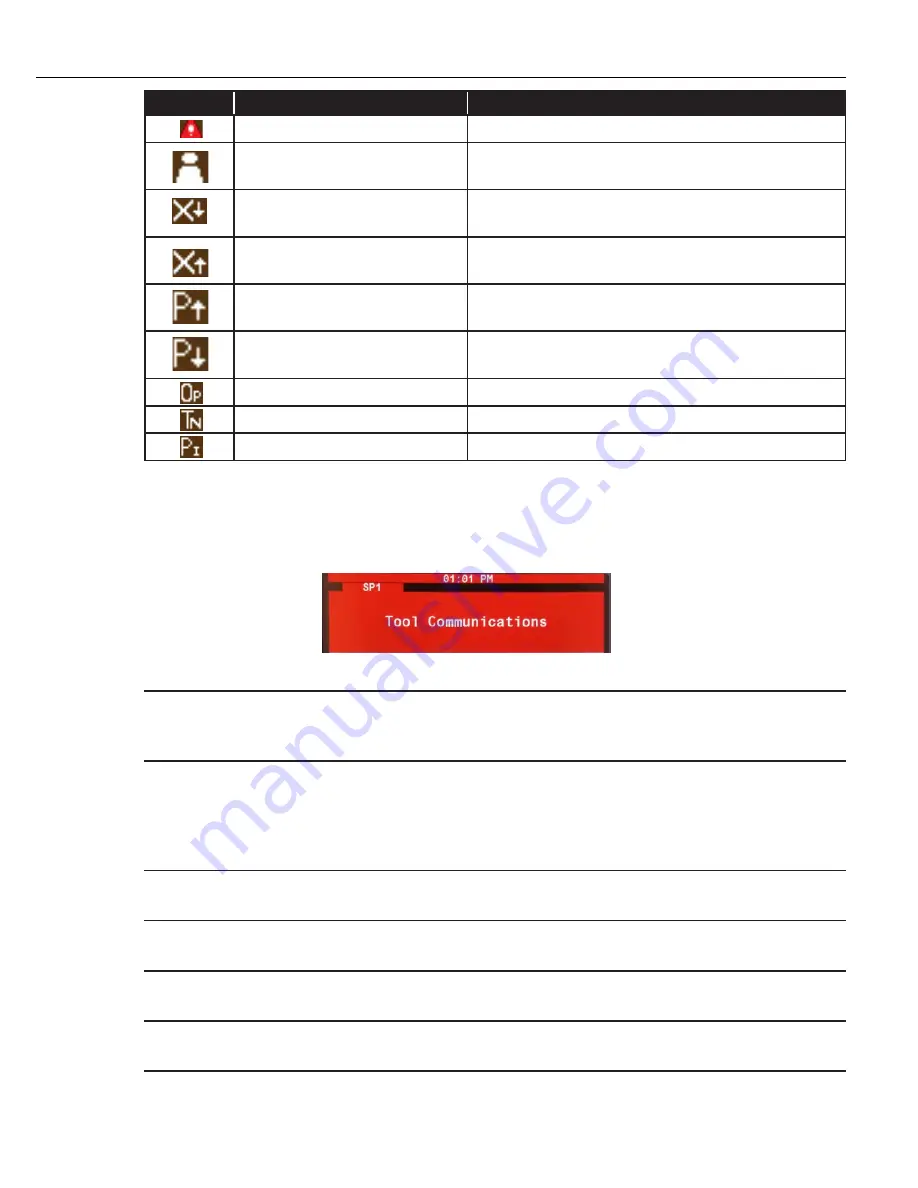
Controller Operation
Instruction Manual
25
Icon
Status
Description
Fault; system not operable
Check the run screen for Fault message.
Remote User
A user is editing the parameters in the controller
remotely, i.e. through Alpha Toolbox.
Audi Command Port Connected
The controller is connected to an AUDI XML protocol
server on the Command port.
Audi Results Port Connected
The controller is connected to an AUDI XML protocol
server on the Results port.
PFCS Solicited Port Connected
The controller is connected to a PFCS protocol server on
the Solicited port.
PFCS Un-Solicited Port Connected
The controller is connected to a PFCS protocol server on
the Un-Solicited port.
OPEN Connected
The controller is connected to an OPEN protocol server.
Toolsnet Connected
The controller is connected to a Toolsnet protocol server.
ToytotaPI Connected
The controller is connected to a ToyotaPI protocol server.
2.8 Faults
The display background color in normal operation is white. In the event of a fault, the spindle display and the time
display backgrounds turn red and the fault description appears on screen. The background color reverts to original
only when the fault is cleared.
Here is a list of the Faults in the QB Expert Alpha controller:
Overcurrent Fault!
Total Current – the controller software limits the current applied to any tool
based on what the tool can handle. This fault is asserted if the total current
applied is greater than allowed.
GFI Fault!
The Ground Fault Interrupter has exceeded its current trip point. A current
detector monitors the current through the three phases of the motor and asserts
this fault when the total current applied to the tool does not equal the total
current returned from the tool. All phases are turned off immediately to protect
the controller from shorts at the tool end.
Logic Voltage Fault!
The controller monitors the +5VDC, -5VDC and +12VDC of its onboard Power
Supply. This fault is asserted when those voltages fall outside of nominal range.
Position Feedback Fault!
The controller is constantly monitoring the resolver zero and span points and
asserts this fault if they go outside specification.
Transducer Span Fault!
This fault is asserted when the transducer zero point has shifted far enough to
prevent a full scale reading from the transducer.
Transducer Zero Fault!
This fault is asserted when the transducer zero point has shifted far enough to
prevent drift compensation at the zero point.
Summary of Contents for QB Expert
Page 8: ......
Page 23: ...Introduction Instruction Manual 15 ...
Page 24: ......
Page 36: ......
Page 37: ...3 QB Expert Alpha Controller Programming SETUP Area SERVICE Area ANALYZE Area ...
Page 94: ......
Page 109: ...Instruction Manual 101 ...
Page 110: ......
Page 123: ...Instruction Manual 115 Tool Operation ...
Page 124: ......
Page 132: ...Input and Output Connector QB Expert Alpha Controller 124 Inputs example ...
Page 133: ...Controller Connections Instruction Manual 125 Outputs Sourcing example ...
Page 157: ...Controller Connections Instruction Manual 149 ...
Page 158: ...MODBUS TCP QB Expert Alpha Controller 150 ...
Page 175: ...Embedded PLC Instruction Manual 167 ...
Page 176: ......
Page 183: ...Multiple Spindle Instruction Manual 175 ...
Page 184: ... QB Expert Alpha Controller 176 ...
Page 201: ...Instruction Manual 193 Maintenance ...
Page 202: ...QB Expert Alpha Controller 194 ...
Page 203: ...10 QB Expert Alpha Controller Appendix A Torsion Compensation Angle Validation ...
Page 206: ......
Page 207: ...11 QB Expert Alpha Controller Glossary ...
Page 210: ......