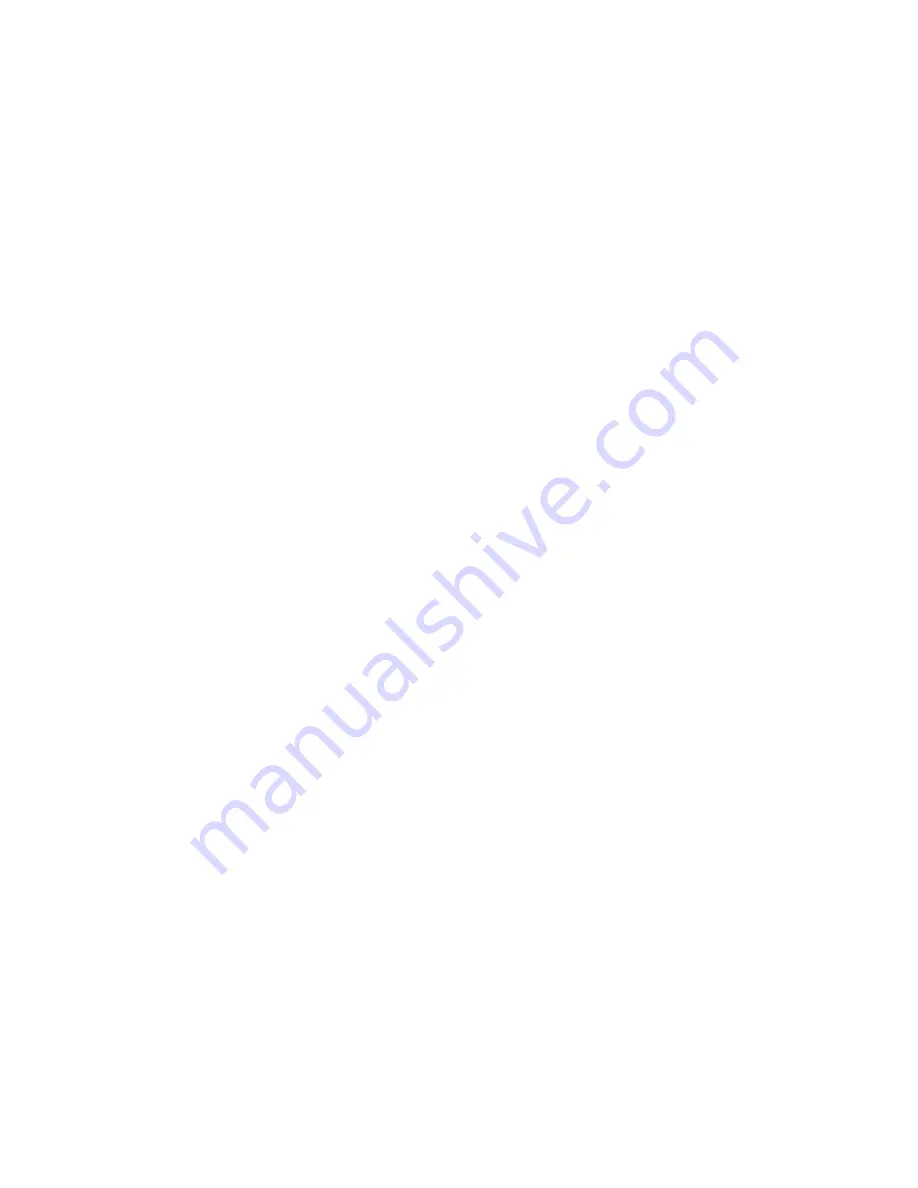
35
Me
mbrane Cl
eaning
For
normal
cleanin
g,
the
SC
-
3
Acid
C
leanin
g
Compound
is
used
fir
st,
then
the
SC
-
2
Alkal
ine
Cleanin
g Compound.
If known b
io
-
foul
in
g
is present, the
SC
-
2 may be used f
irst.
U
se hot water
if poss
ib
le, up to 120° F (45C)
is
recommended as it
greatly enhances the ability of the cleaners
to do their jobs.
If
the
history
of
the
system
is
unknown
or
has
be
en
left
“unpickled”
for
an
extend
ed
length
of
time
and
bio
lo
g
ical
growth
is
present,
it
is
recom
mended
that
the
system
is
cleaned
with
S
C
-
2,
usin
g
an
alternat
e
source
of
un
chlorinated
fresh
wa
ter
before
the
system
is
run
under
pr
essure.
A
s
imp
le
test
can
be
performed
to
see
if
bio
lo
g
ical
growth
has
occurred.
Before
runnin
g
the
system,
remove
the
prefilters
and examine
their
condition
If
the
housing
s
are
full
of
smel
ly
di
s-
colored water, the system was
not properly
stored. Install
clean prefi
lters
if they were bad. Next
check
the
membrane.
At
tach
the
brine
discharge
service
hose
and
lead
to
a
buck
et.
Op
en
the
pressure
relief
valve
one
turn,
and
manually
run
th
e
system
for
30
seconds.
Examine
the
brine
water:
if
it’s
di
scolored
and
sme
ll
s
bad,
perform
an
SC
-
2
cleanin
g
w
ith
an
alternate
sourc
e
of
unchlorinated
water
before
runnin
g
the
sy
stem
pressur
i
zed.
If
the
br
ine
is
fa
irly
clean,
the
sy
s-
tem
can
be
purged,
run
normal
ly,
and
checked
for
performance.
Clean
th
e
membranes
only
if
performance is reduced.
Heating
the
water
i
s
preferable.
One
way
to
do
this
i
s
to
f
ind
a
camp
stove
and
use
a
lar
ge
stainless
steel
pot
to
hea
t
the
solution
in.
The
cleanin
g
so
lution
throu
ghout
the
system
wi
l
l
heat
as
it
circulates
in
and
out
of
the
pot.
An
altern
ative
is
to
heat
the
one
or
two
gallon
s
of
in
itia
l
water
to
120°
on
the
main
stove
before
mixin
g
in
the
cleaner
and
circulating
it
into
the
system.
Periodically stop and reheat the solution.
Perform the cleaning procedu
res while the ship is
in acc
eptable sea
water for purg
ing and testing
.
There are two types of cleaners: acid and alkaline.
The acid cleaner (SC
-
3)
wi
l
l remove m
in-
eral
scalin
g.
The
alkal
ine
cleaner
(SC
-
2)
is
u
sed
to
remove
biolo
gical
by
-
products,
oi
l,
and
dirt
particles
that
get
past
the
prefilters.
If
me
mbrane
performance
is
reduced
and
they
h
ave
not
been
pickled
rec
ently,
cleaning
w
ith
both
chemicals
is
recommended.
The
acid
cleaner
should
be
used
first.
If
the
membrane
f
ails
to
respond
to
both
cleanings,
this
is
an
indication
of
another
problem
with
the
system,
or
that
it
is
time
to
replace
th
e
membrane.
Conta
ct
Spectra Watermakers befor
e removing a me
mbrane.
The
me
mbranes
need
to
be
cleaned
only
when
operatin
g
pressures
have
r
isen
more
than
10%
or
the
produc
t
quality
degrades.
The
leadin
g
cause
of
foulin
g
in
mar
ine
use
is
fro
m
biolo
g
ical
growth
that
occurs
when
the
system
is
left
unused
w
ithout
flush
in
g
or
p
ickl
in
g.
Foul
in
g
from
m
ineral
scal
in
g
can
happen
during
operation
under
cert
ain
sea
wat
er
condi-
tions,
and
from
rust.
Monitor
the
produ
ct
salinity
and
fe
ed
pressure
b
ar
graphs
for
higher
than
normal
readin
gs
for
the
condit
ions.
Other
condit
ions
can
cause
hi
gh
pressure
such
as
cold feed water or clo
g
ged fi
lters. Low product f
low
is
usual
ly due to
lo
w vo
ltage, dama
ged
feed
pump
or
Clark
Pump
issues.
Look
for
all
other
causes
b
efore
cleaning
the
membrane.
Membrane life can be shortened by exc
essive cleaning.
The M
e
mbranes
Summary of Contents for NEWPORT 400 Mk II
Page 2: ...2 ...
Page 15: ...15 John Guest Super Speedfit ...
Page 22: ...22 ...
Page 49: ...49 Z BRANE OPERATION MANUAL ...
Page 53: ...53 ...