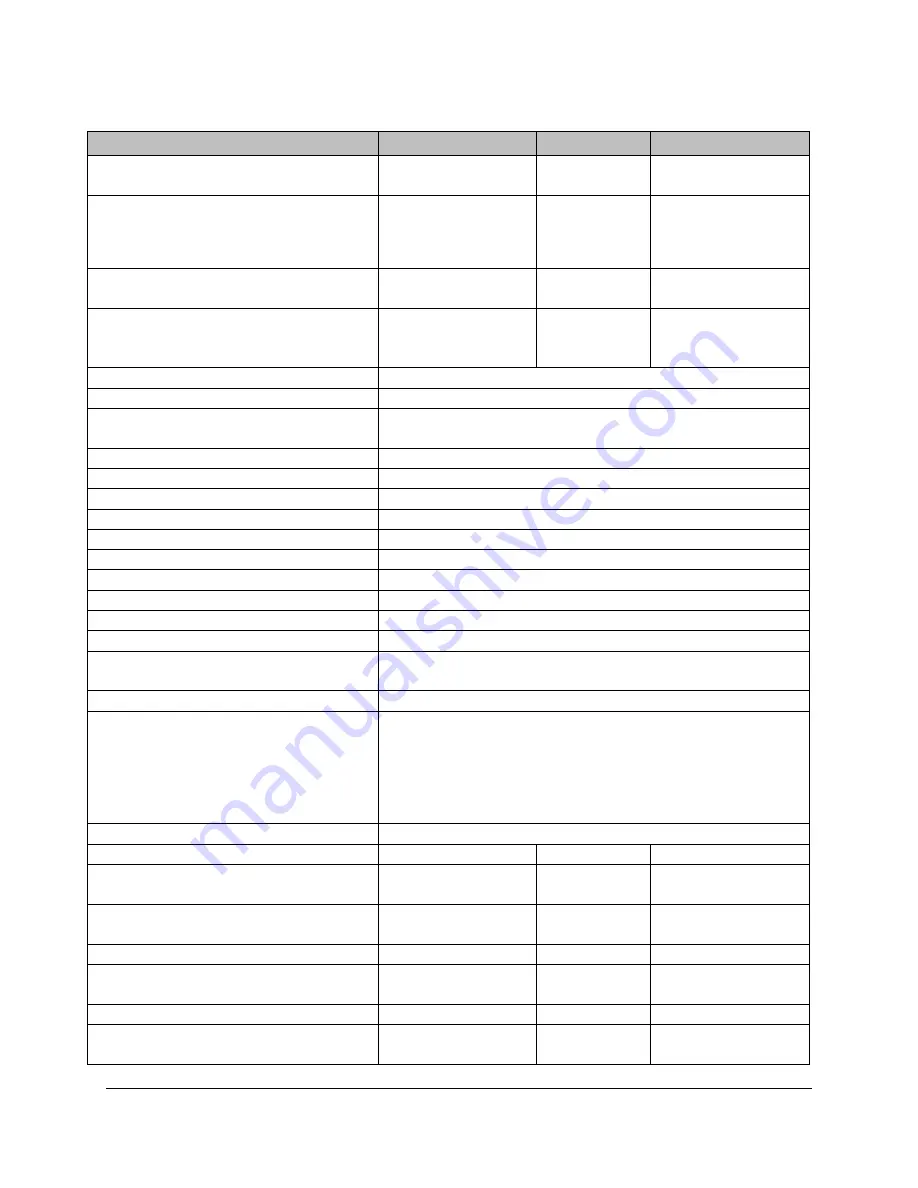
39
TRAK Machine Tools
Southwestern Industries, Inc.
TRAK TMC Mills with ProtoTRAK RMX CNC Safety, Installation, Maintenance, Service & Parts List
2.13
Machine Specifications
MODEL NAME
TMC5
TMC7
TMC10
Table Size
27.56” x 15.75”
35.43” X
19.69”
44.09” x 19.
69
”
T-Slots (number x width x pitch)
3 x 18 x 100 mm
3 x .709” x 3.937”
5 x 18 x 100
mm
5
x .709” x
3.937
”
5 x 18 x 100 mm
5
x .709” x 3.937”
Travel (X, Y, Z axis) with Soft Limits
20” x 16” x 20”
30” x 20” x
20”
40.75” x 20” x 20”
Travel (X, Y, Z axis) with No Soft Limits
*User may cause damage if they crash.
Travel distance is just shy of hard stops
21.25” x 17.50” x
21.25”
30.75” x
21.25” x
21.25”
42” x 21.25” x 21.25”
Spindle Taper
40 Taper
Spindle Speed Range
–
Production Ops
50-8000
Spindle Speed Range
–
Production Ops
with 12K spindle option
50-12,000
Spindle Speed Range
–
Tool Room Ops
50-5000
Spindle Nose Diameter
3”
Tool Clamping Force (90 psi)
1500 lbs.
Tool Holder Type
CAT 40 or BT40
ATC Tool Capacity
16
Maximum Tool Weight Including Holder
15 lbs.
Maximum Tool Diameter
3.14”
Carousel Speed
.8 sec from station to station
Tool Selection System
Bi-directional/ shortest path
Retention Knob
See drawing of retention knob
Spindle Motor Power (continuous)
10 HP
Full load amps 27.7
Spindle Motor Power (peak)
15 HP
Power Requirements (volts, phase,
current)
208V (200-240V is acceptable), 3P, 68A
Note
–
Current can be as high as 86 amps with all options
ordered: CTS (+12A), 4
th
axis (+5A), 12K spindle (+1A)
480V w/ transformer option (432-528V is acceptable), 3P, 46A
Note
–
46 amps based nominal rated current of transformer.
Maximum Weight of Workpiece
1000 lbs.
Height of Table from Bottom of Bed ***
38”
38”
38”
Minimum Spindle Nose to Table
Distance****
3.5”
3.5”
3.5”
Maximum Spindle Nose to Table
Distance****
23.50”
23.50”
23.50”
Distance of Tool Carousel to Table
18”
17.5”
17.5”
Spindle Center to Spindle Head Casting
Face
16.50”
18.25”
18
.25”
Minimum Machine Height ***
90”
90”
90”
Maximum Machine Height (head all the
way up) ***
106.50”
106.50”
106.50”