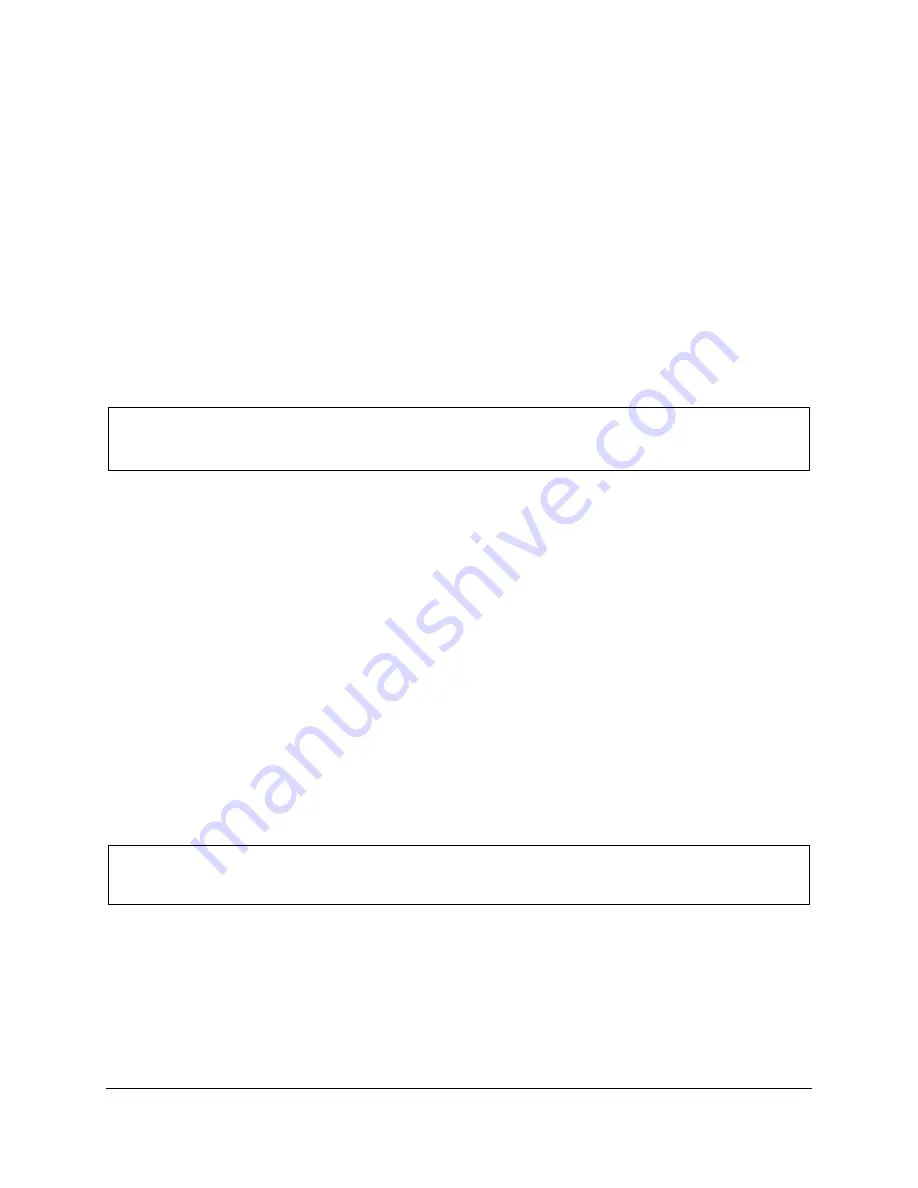
92
TRAK Machine Tools
Southwestern Industries, Inc.
TRAK TMC Mills with ProtoTRAK RMX CNC Safety, Installation, Maintenance, Service & Parts List
5.
Press E-Stop
6.
Turn off the power at the machines disconnect switch, and disconnect power.
7.
Remove the coupler cover from the motor mounting bracket located behind the spindle drive
motor as shown in figure 5.1.9.3d. The coupler slot should be facing outward toward the front of
the machine.
8.
Rotate the coupler
until the slot is at twelve o’clock and you have equal access to the jack screw
and the two clamping screws.
9.
Use scale or caliper to measure distance from coupler edge on ballscrew side to the motor
casting and take note of the measurement as shown on figure 5.1.9.3c. Loosen coupler lock
screws on ballscrew side of coupler. Tighten jackscrew to separate coupler from shaft as shown
on figure 5.1.9.3c.
10.
Disconnect two electric cables to motor. Remove four SHCS screws holding motor to mill.
CAUTION!
Do not touch the ball screw or linear ways with your bare hands. Wear latex or other suitable gloves to
protect precision surfaces from your hands.
11.
Remove the coupler from the old motor, examine the polyurethane spider element for excessive
wear (there should be no visible backlash). If it is suitable for reuse, set coupler distance on new
motor using recorded measurement before reinstalling motor in mill.
12.
Loosen the two SHCS that clamp the coupler, tighten the jack screw to open the coupler.
13.
Set a gap of approximately 0.050” between each coupl
er half where they come together.
14.
Install the motor onto the ball screw. Attach the four SHCS screws holding motor to mill to 30 ft
lbs.
15.
Loosen the jack screw (ball screw side), then tighten the two clamp screws opposite the jack
screw.
16.
Reconnect the power and encoder cables to the servo motor. Turn the power on the machine.
17.
Enable servos, perform Service Code 505, slowly jog Z axis into Z Axis hard stop. Back out one
ballscrew revolution and adjust home switch to trigger. Adjust index angle to 180 d/- 40
degrees at 0.500” from hard stop
.
18.
Set the tool change height, perform service code 501.
WARNING!
After completing the replacement of the servomotor or ballscrew on the Z axis, service code 505 and
501 MUST be performed.