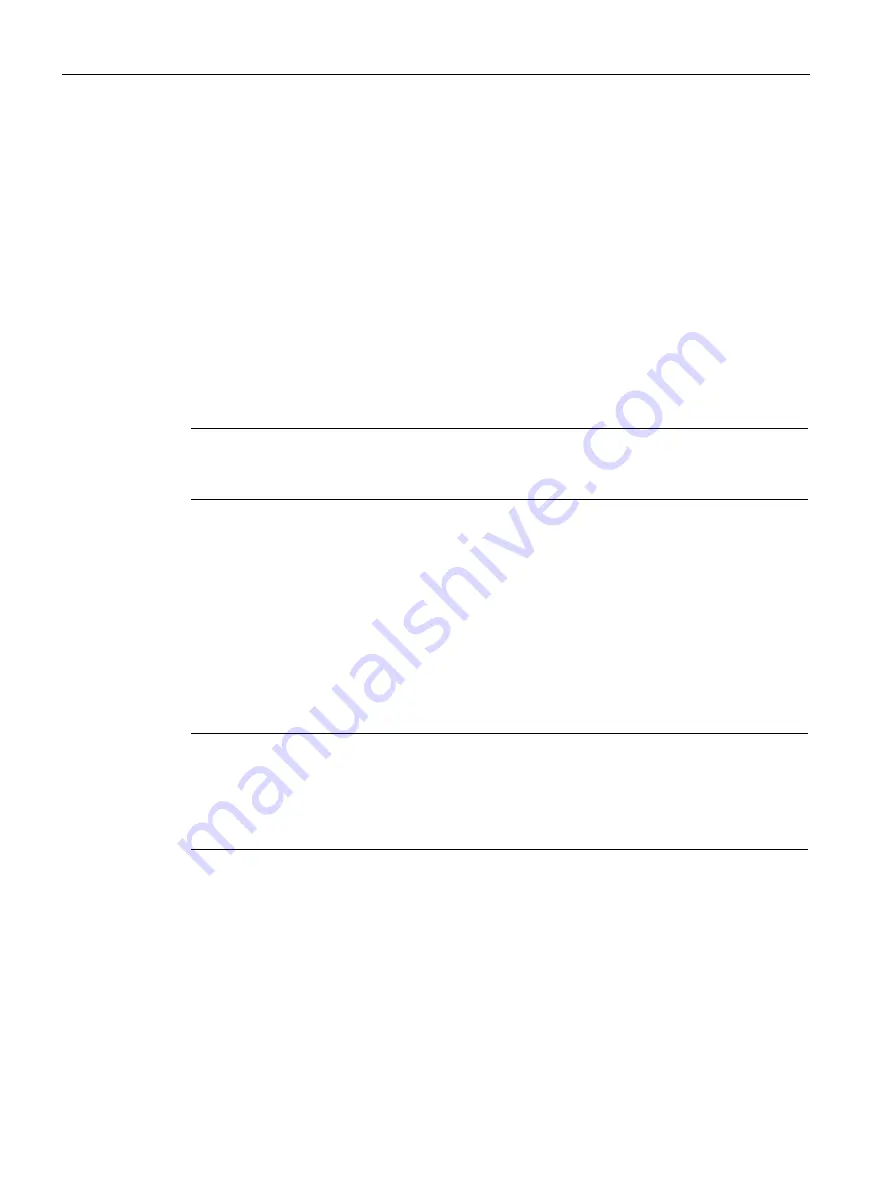
Outputs
11.2 Operator Panel LEDs
SIMOCODE PRO V PN FDI
76
Programming and Operating Manual, 05/2020, A5E44499659002A/RS-AA/001
Settings Basic Unit Outputs 1 to 3
Control of the BU Outputs function block via any signal (any sockets, e.g. device inputs,
control bits from PROFINET, etc. usually from the QE contactor controls).
11.2
Operator Panel LEDs
Operator Panel LEDs
SIMOCODE pro has an OP - LED function block for controlling the seven freely-assignable
LEDs. The LEDs are in the Operator Panel and can be used to display any status. For this,
the inputs (plugs) of the OP - LED function block must be connected to the respective
sockets (e.g. to the sockets for the status information of the control function.
Note
The OP - LED function block can only be used if the Operator Panel (OP) is connected and
configured in the device configuration!
The OP-LED function block consists of:
●
4 plugs, "OP LED Green 1" to "OP LED Green 4", corresponding to the green LEDs. The
green LEDs are optically/constructionally allocated to the buttons on the Operator Panel.
They will normally display feedback concerning the motor operating state.
●
3 plugs, "OP LED Yellow 1" to "OP LED Yellow 3", corresponding to the yellow LEDs.
●
4 green LEDs.
●
3 yellow LEDs (not for Operator Panel with Display (OPD)).
Overall, there is 1 OP LED function block for BU1 and BU2.
Note
The three yellow LEDs mentioned in this section are not available for the operator panel with
display. Status information can be read out here directly via the display. While it is still
possible to connect the corresponding three plugs via the software, they remain
nonfunctional.