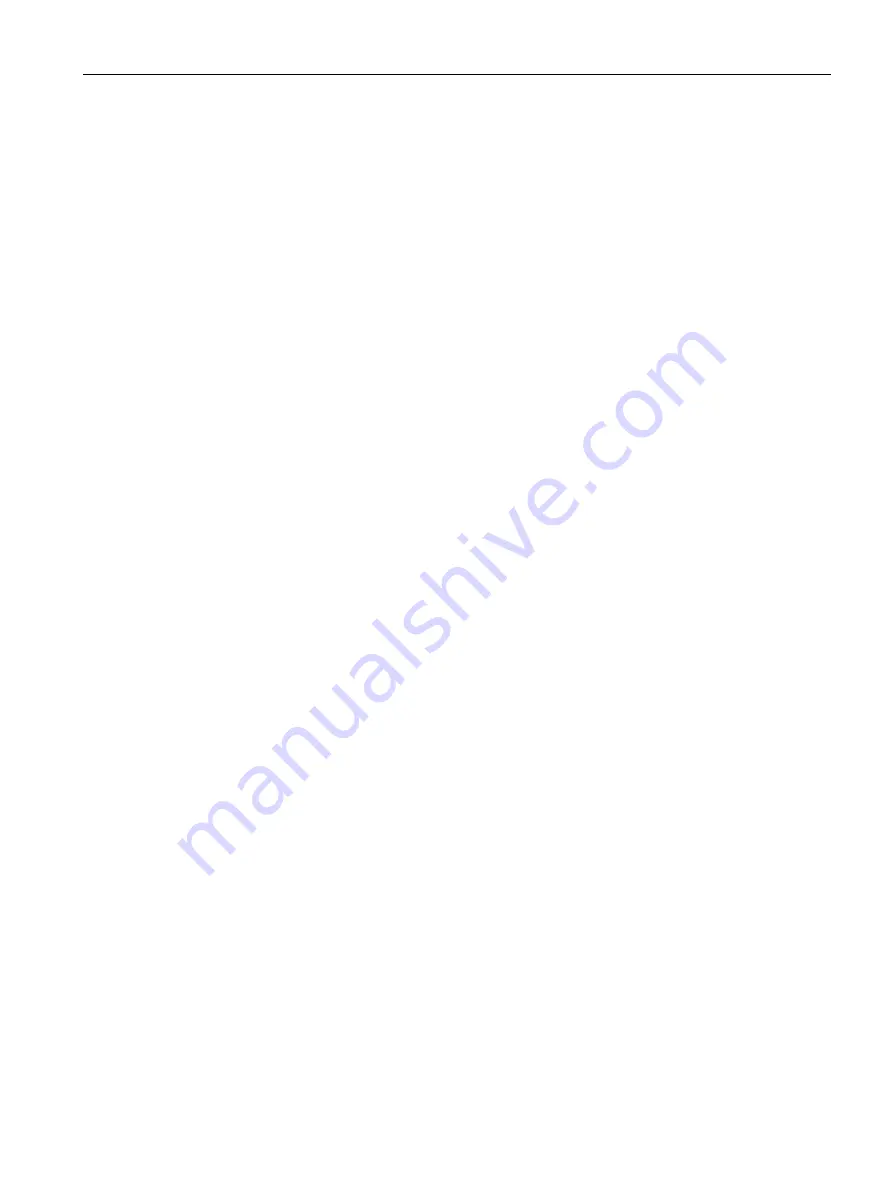
Inputs
10.4 Cyclic Receive
SIMOCODE PRO V PN FDI
Programming and Operating Manual, 05/2020, A5E44499659002A/RS-AA/001
73
Application examples
Among other things, you can monitor the following motor components:
●
Motor windings
●
Motor bearings
●
Motor coolant temperature
●
Motor gearbox oil temperature.
The individual temperatures of the three sensor measuring circuits can be monitored
independently of each other by connecting free Limit Monitors.
Settings Temperature Module Inputs
Sensor Type
PT100, PT1000, KTY83, KTY84, NTC
Response at sensor fault/out of range
Disabled, Signaling, Warning, Tripping
Number of active sensors
1 sensor, 2 sensors, 3 sensors
10.4
Cyclic Receive
Cyclic Receive
With the Cyclic Receive function block, you can specify which cyclic data from the
automation system will be further processed via PROFINET in SIMOCODE pro. These will
normally be PLC/PCS binary control commands. Connection with the Control Stations
function block in SIMOCODE pro will allow the motor to be controllable via PROFINET.
Direct connection of the analog value with the AM Output function block will result in, for
example, the cyclic output of the value sent via PROFINET at the output of the Analog
Module.
The "Cyclic receive" function blocks consist of:
●
Eight bits each (byte 0 and byte 1 for binary information)
●
One word (= two bytes, byte 2 to 3 for an analog value, freely programmable) for basic
type 1.
A total of three "Cyclic receive" function blocks (0, 1, 2/3) are provided.
PROFINET:
The Cyclic Send data are exchanged between the IO Device (SIMOCODE pro) and the IO
Controller (automation system). The IO Controller sends the Cyclic Receive data to
SIMOCODE pro in each case. In response, SIMOCODE pro returns the Cyclic Send data.