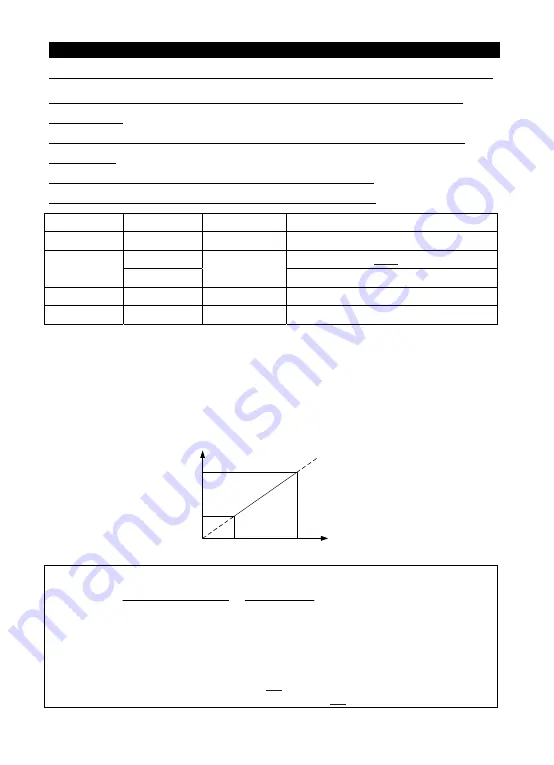
2
1
1
Parameter Description
Parameter Description
5.52 Input Signal across Terminal 4-5 (P.196~P.199)
P.196 “Frequency corresponds to the minimum input current/voltage across
terminal 4-5”
P.197 “Frequency corresponds to the maximum input current/voltage across
terminal 4-5
P.198 “Minimum input current/voltage across terminal 4-5”
P.199 “Maximum input current/voltage across terminal 4-5”
Parameter
Factory Setting
Setting Range
Remarks
-
-
-
z
H
0
6
~
0
0
6
9
1
50Hz
P.189
=1
197
60Hz
0~650Hz
P.189=0
-
-
-
0
2
~
0
0
8
9
1
-
-
-
0
2
~
0
0
9
9
1
<Setting>
•
Emendation steps:
1. Make sure that the current signal is correctly inputted.
2. Assume that the input current equals Value A and the expected output frequency is 20Hz. Adjust
the signal to Value A, and write 20 into P.196. Also, Value A will be written into P.198.
3. Assume that the input current equals to Value B, and the expected output frequency is 60Hz.
Adjust the signal to Value B, and write 60 into P.197. Also, Value B will be written into P.199.
Note: 1. The equation for the above figure is:
2. If the user can not provide the actual stability of the signal input, parameters P.198 and P.199 can be set up
manually. The value of P.198 corresponds to the frequency of the P.196 set. The value of P.199 corresponds
to the frequency of the P.197 set. When setting up the parameters manually, verify the range of P.196 and
P.197, and then adjust the voltage values of P.198 and P.199.
3. After any resetting of P.196~P.197, the curve of
P.39
becomes invalid.
4. For selecting the input signal across terminal 4-5, please refer to
P.17
.
P.197
P.196
Value A
Value B Signal across
terminal 4-5
R
un
ni
ng
fr
eq
ue
nc
y
se
t v
al
ue
Running frequency-P.196
Current value-Value A
P.197-P.196
Value B-Value A
=