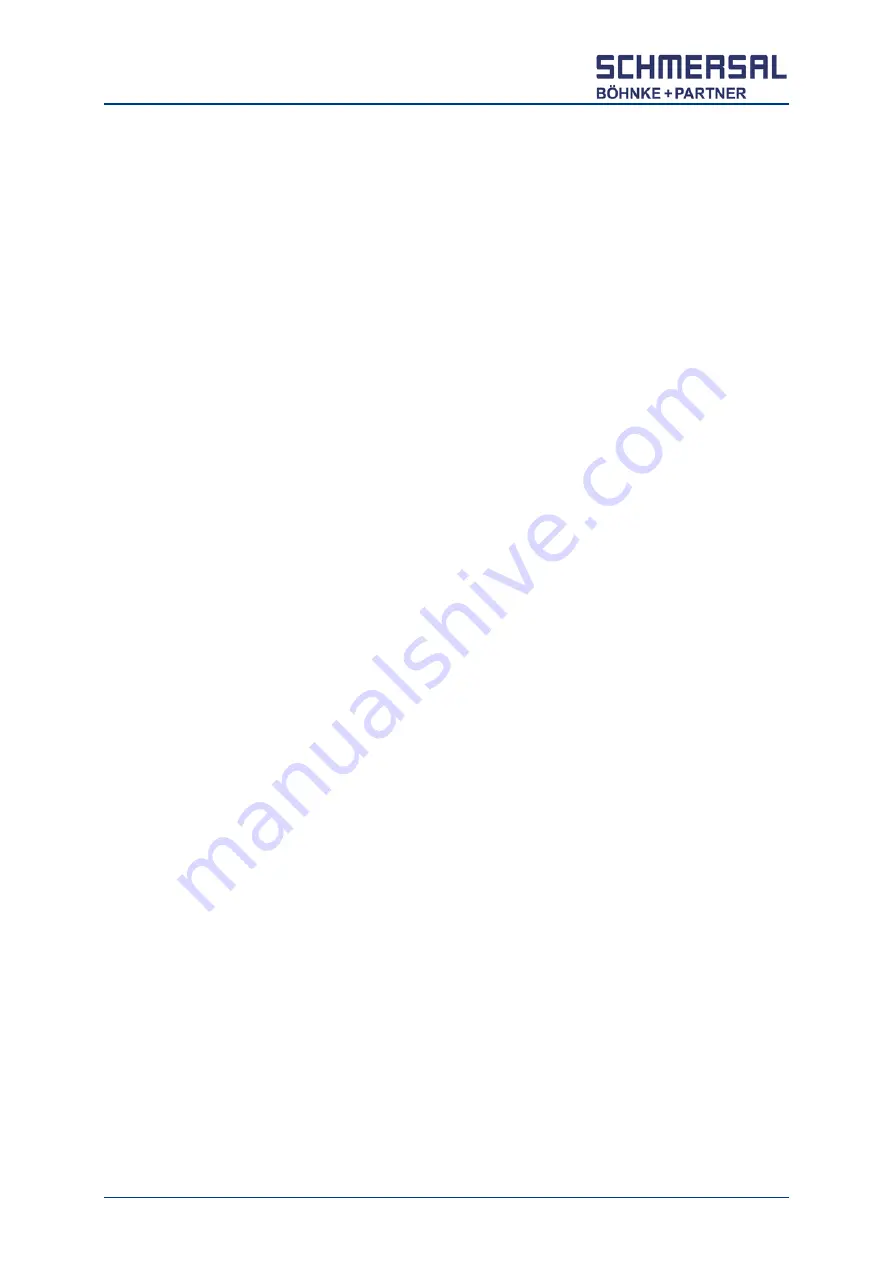
Installation manual of system “bp408” - Electrical connection
61
To ensure compliance with the EMC guidelines, a suitable single-phase mains
filter must be connected to the 230 V AC control circuit with the connected signal
circuit.
The control lines should be routed away from the load lines as far as possible
using separate cable ducts. When intersecting, an angle of 90° should be
maintained wherever possible.
Control units are always connected using choke, filter and shielded cables
according to the assembly and installation instructions of the manufacturer.
Make sure that all devices in the cabinet are well grounded using short
grounding wires with a large cross-section, which are connected to a common
grounding point or ground rail. It is particularly important that each control unit
(e.g. a speedometer) connected to a inverter is connected to the same
grounding point as the inverter itself via a short cable with a large cross-section.
Flat leads (e.g. metal holders) are preferred because they have lower
impedance at high frequencies.
Use shielded or armoured cables for the load connections between the drive
and inverter or control system and ground the shield / armour at both ends.
Data connections (group, DFÜ, printer port etc.) are generally established using
shielded lines. The shield of the data lines should be earthed on one side.
Mounting plates consist of galvanised steel plates in order to be able to produce
large-area ground connections to all control components.
Use of fail-safe components causes increased insensitivity to environmental
influences.
The car must be grounded by means of the green / yellow cable, which also
leads through the travelling cable.
The free travelling cable cores should be earthed on one side of the control
cabinet.
The components used in the control systems comply with the regulations of DIN
EN 81 as well as VDE 0100 / 0101 / 0551 / 0660 and BGV A2. The control
cabinets comply with the installation standard VDE 0660 / part 500.
The main and auxiliary contactors used in the control system comply with DIN
EN 81-20, 5.10.3 and VDE 0660, but at least device class D3.
Voltage fluctuations that are within the tolerance range (+10%; -20%) of energy
supply companies (RUs) are permissible.
Faults caused by an impermissible increase in voltage cannot lead to claims for
damages against the manufacturer.
If the user attaches additional coils (inductors) on his own initiative, it is of utmost
importance that these are also suppressed.
For DC-powered inductors such as contactors, relays, brake magnets, bolt
magnets and hydraulic valves, always place a diode (1000 V / 1 A) anti-parallel
and as close as possible to the coil. (Free-wheeling diode at
Böhnke + Partner GmbH)
For AC-powered contactors, relays, brake magnets, bolt magnets and hydraulic
valves, it is always necessary to install an RC combination, matched to the coil
type, parallel and as close as possible to the coil. (RC combination of
Böhnke + Partner GmbH can be used universally.)
Summary of Contents for bp408
Page 2: ......
Page 24: ...24 Installation manual of system bp408 Safety instructions...
Page 52: ...52 Installation manual of system bp408 The control system bp408...
Page 58: ...58 Installation manual of system bp408 Installation and assembly...
Page 80: ...80 Installation manual of system bp408 Electrical connection...
Page 118: ...Installation manual of system bp408 Appendix 118 Appendix A Menu navigation bp408...
Page 119: ...119 Installation manual of system bp408 Appendix B Update of the firmware via USB stick...