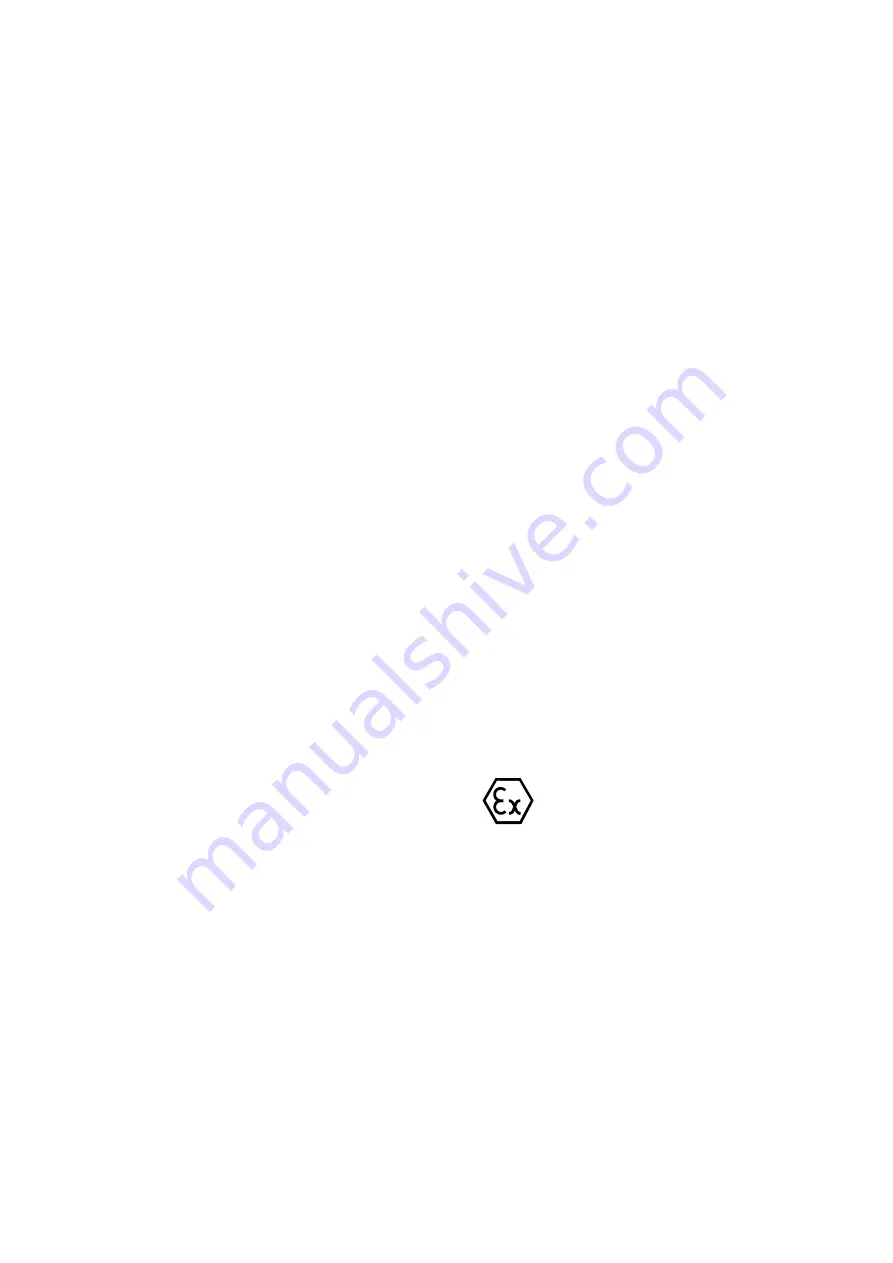
Installation and operating instructions Salmson-Rocsan SDL 55
APPENDIX English
the motor should be around 10 % more than the
power requirement of the pump. For frequency
converters with a low-harmonic output, it may be
possible to reduce the 10 % power reserve. This
is normally done by using output filters.
Further-
more, the standard motors are not equipped
with shielded cables.
The frequency converter
and filter must be synchronized with each other.
Ask the manufacturer.
The configuration of the frequency converter de
-
pends on the rated motor current. Make sure that
the pump operates without jerking or vibrating,
especially in the lower speed range. Otherwise,
the mechanical shaft seals could be damaged and
start leaking. You must also consider the flow rate
in the pipe. The slower the flow rate, the greater
the risk of solids depositing in the pump and pip-
ing.
For applications covered by DIN EN 12050,
a minimum flow rate of 0.7 m/s at a pumping
pressure of 0.4 bar is required.
We also recom-
mend these figures for other applications.
It is important that the pump operates across
the entire control range without vibrations,
resonance, oscillation or excessive noise (ask the
manufacturer if necessary). Increased motor noise
caused by the harmonics of the power supply is
normal.
When configuring the frequency converter,
always make sure the quadratic curve (U/F pump
curve) for pumps and fans is correctly set! This
ensures that the output voltage at frequen-
cies greater than the rated frequency (50 Hz or
60 Hz) is adjusted to the power requirement of
the pump. Newer frequency converters feature
an automatic power optimization function which
achieves the same effect. For the frequency con-
verter setting, please refer to its installation and
operating instructions.
Faults with the motor monitor may occur on
motors fed by a frequency converter depending
on the frequency converter type used and instal-
lation conditions present. The following general
measures could help to reduce or avoid faults:
• Keeping within the thresholds stated in
IEC 60034-17 for the voltage peaks and rise
speed (output filters may be necessary).
• Varying the pulse frequency of the frequency
converter.
• Using our external double pencil electrode for
faults with the sealing chamber monitor.
The following construction measures could also
help to reduce or prevent faults:
• Using shielded power cables.
Summary
•
Continuous operation between 1 Hz and the rated
frequency (50 Hz or 60 Hz), while considering the
min. flow speed.
• Consider additional measures with regard to EMC
(choice of frequency converter, using filters, etc.).
• Never exceed the rated current or rated speed of
the motor.
• It must be possible to connect the motor’s own
temperature monitor (bimetallic strip or PTC
sensor).
10.3. Ex-approval
This section contains special information for
owners and operators of pumps which have been
built and certified for use in environments where
explosions may occur.
It expands on and therefore supplements the
standard instructions for this pump. It also ex-
pands on and supplements the “General safety
information” section and must be read and fully
understood by all users and operators of the
pump.
This section applies only to Ex-rated pumps
and contains additional instructions for these
pumps!
10.3.1.
Identification of Ex-rated pumps
Pumps that have been approved for use in an
explosive atmosphere are be marked as follows on
the rating plate:
• “Ex” symbol of the corresponding approval
•
Information on Ex classification
•
Certification number
10.3.2. ATEX approval
The motors are certified for use in potentially
explosive areas in accordance with EC direc-
tive 94/09/EC, which requires device group II,
category 2.
The motors can be used in both zone 1 and zone
2.
These motors may not be used in zone 0!
Non-electrical devices (e.g. hydraulics) also com-
ply with EC directive 94/09/EC.
ATEX classification
The Ex classification, for example,
II 2G Ex de IIB T4 Gb on the rating plate indicates
the following:
•
II = device group
•
2G = device category (2 = suitable for zone 1, G =
gas, vapour and mist)
•
Ex = explosion-protected device complying to
Euro norm
•
d = ignition protection type for motor casing:
Pressure-resistant encapsulation
•
e = ignition protection for terminals: Increased
safety
•
II = intended for places where explosions may
occur, with the exception of mines
•
B = intended for use with gases in sub-group B
(all gases excluding hydrogen, acetylene, carbon
disulphide)
•
T4 = max. surface temperature of the device is
135 °C
•
Gb = device protection level “b”