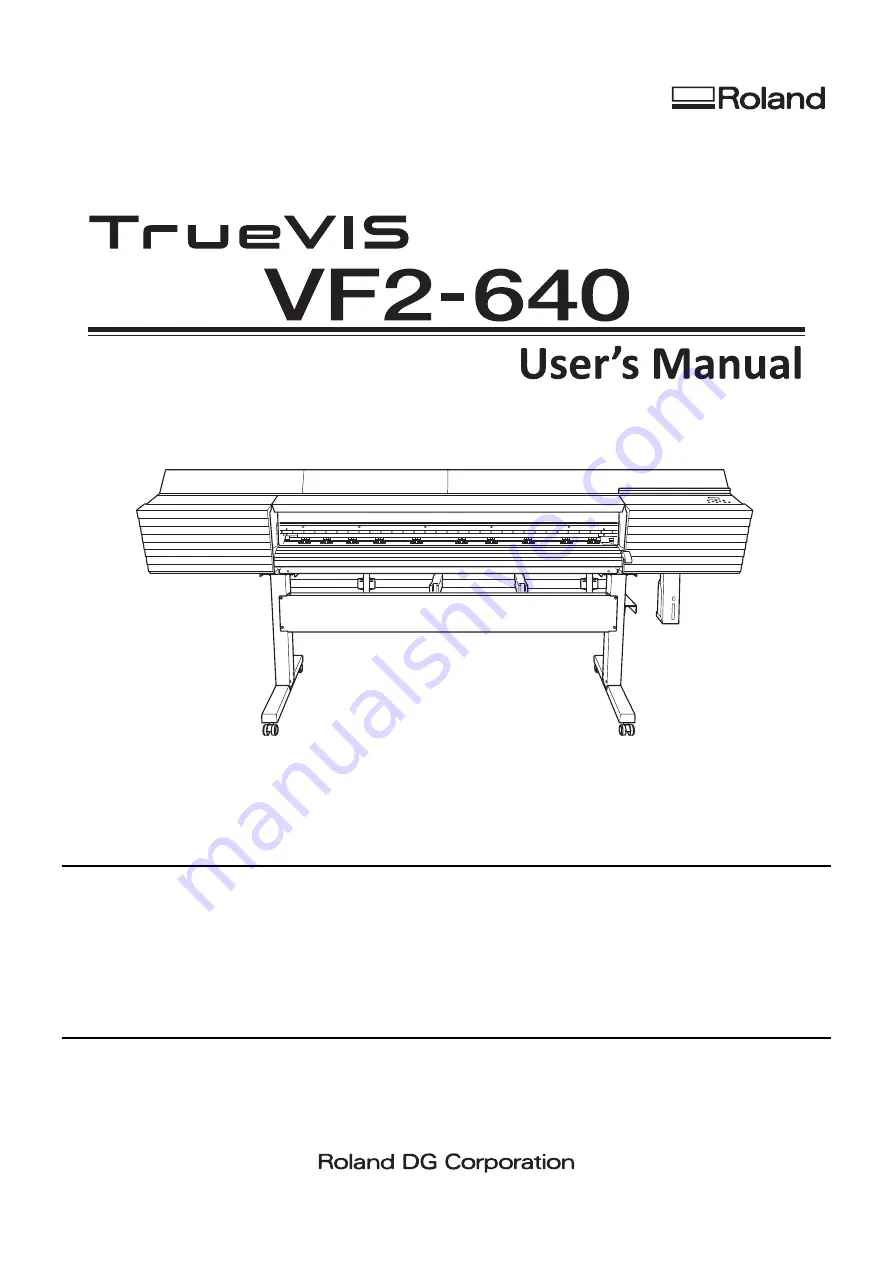
Thank you very much for purchasing this product.
• To ensure correct and safe usage with a full understanding of this product's performance, please be sure to read through this manual completely and
store it in a safe location.
• Unauthorized copying or transferal, in whole or in part, of this manual is prohibited.
• The specifications of this product and the contents of this operation manual are subject to change without notice.
• The operation manual and the product have been prepared and tested as much as possible. If you find any misprints or errors, please inform us.
• Roland DG Corporation assumes no responsibility for any direct or indirect loss or damage that may occur through use of this product, regardless of any
failure to perform on the part of this product.
• Roland DG Corporation assumes no responsibility for any direct or indirect loss or damage that may occur with respect to any article made using this
product.
FA02013/R1-200611
Copyright © 2020 Roland DG Corporation
Summary of Contents for TrueVIS VF2-640
Page 7: ...1 Basic Handling Methods 6...
Page 51: ...Ink Pouch TR2 Cleaning Liquid Pouch Replacement 50 2 Basic Operations...
Page 52: ...2 Output Method 51...
Page 61: ...REDO ADJ YES DONE 10 Press ENTER to confirm your entry Printing Output 60 1 Printing Method...
Page 68: ...3 Optimizing Quality and Effi ciency 67...
Page 99: ...W1100mm B Adjusting the Output start Location 98 2 Optimizing Work Efficiency...
Page 121: ...4 Maintenance 120...
Page 169: ...5 Troubleshooting Methods 168...
Page 196: ...6 Appendix 195...