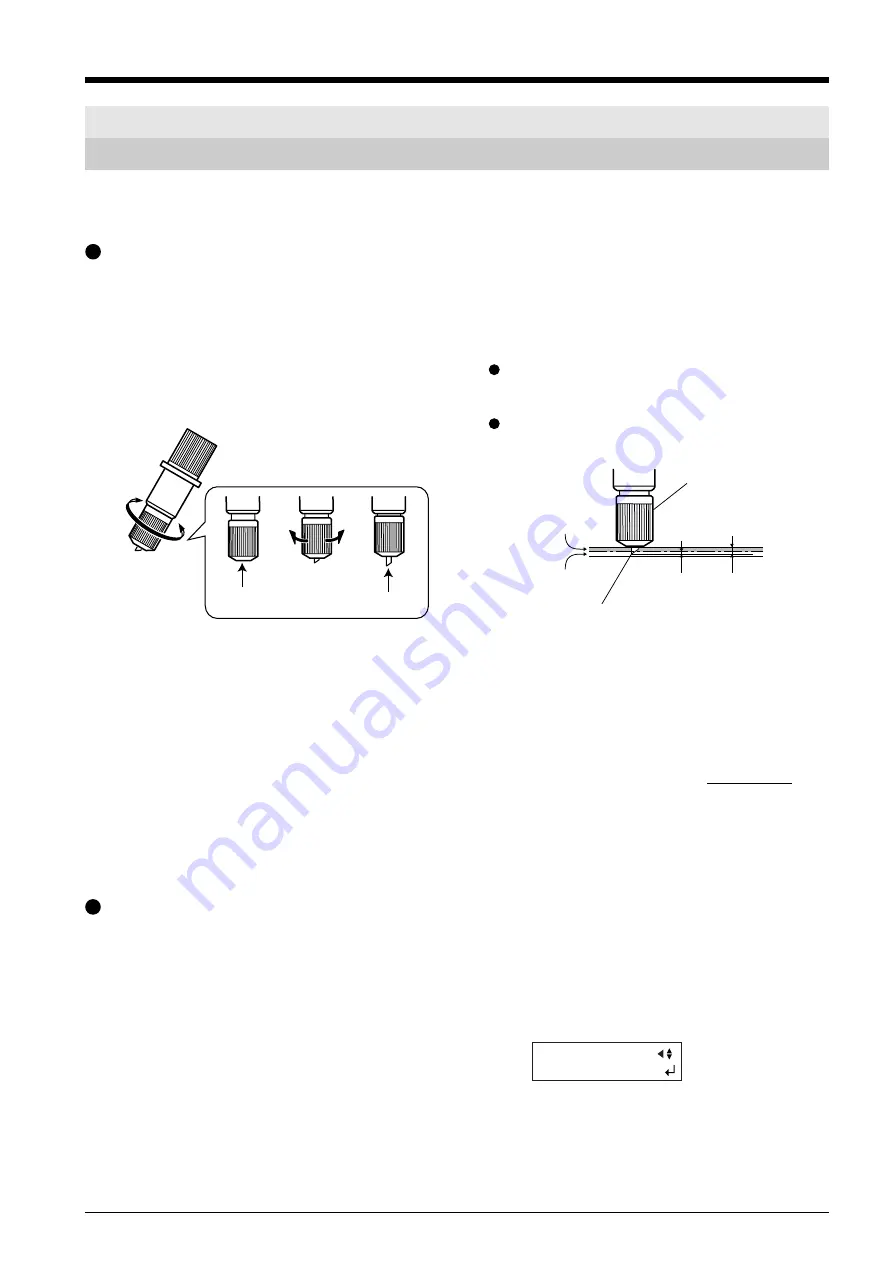
31
4 Advanced Operation
4-1 Detailed Cutting-condition Settings
Adjusting the Blade Extension
When you want to perform accurate and fine adjustment of the cutting-in amount, such as when cutting material with thin carrier
paper or when performing half-cutting of material having no carrier paper, you can obtain good results by adjusting the tip of the
blade.
Each indicator tick corresponds to 0.1 mm, and adjustment for
0.5 mm can be made by rotating the cap one full turn.
Turn the cap portion to adjust the amount of blade
extension, which is approximately equal to the cutting-in
amount.
Setting the blade force slightly higher than normal
achieves a stable cutting-in amount.
[Rough Estimate for the Amount of Blade
Extension]
Use the following dimension as a rough estimate for setting
the amount of blade extension.
Amount of
blade
extension
=
Thickness of
the material
portion
+
2
Thickness of
the carrier paper
Adjusting the Blade Offset
The blade offset is determined according to the blade. The included blade is designed to cut correctly at a setting of 0.25 mm, but
adjustment may be required when using another type of blade. For information about the optimal offset for each blade, see “5
Selecting the Material and Blade.” Good results can also be obtained by performing fine adjustment of blade offset according to the
material.
1
Press the [MENU] key several times until the screen
shown in the figure appears.
UNSETUP
Min.: 0 mm
Max.: 2.5 mm
Amount of blade
extension
Cap
Material portion
Carrier-paper
portion
Blade
Half of the
thickness of
the carrier
paper
Amount of blade
extension is
approximately equal
to cutting-in amount
Summary of Contents for Camm-1 Pro GX-300
Page 9: ...To Ensure Safe Use 7...
Page 16: ...14...
Page 54: ...52...
Page 66: ...64...
Page 70: ...68...
Page 81: ...79...
Page 82: ...80...
Page 83: ......
Page 84: ...R3 070216...